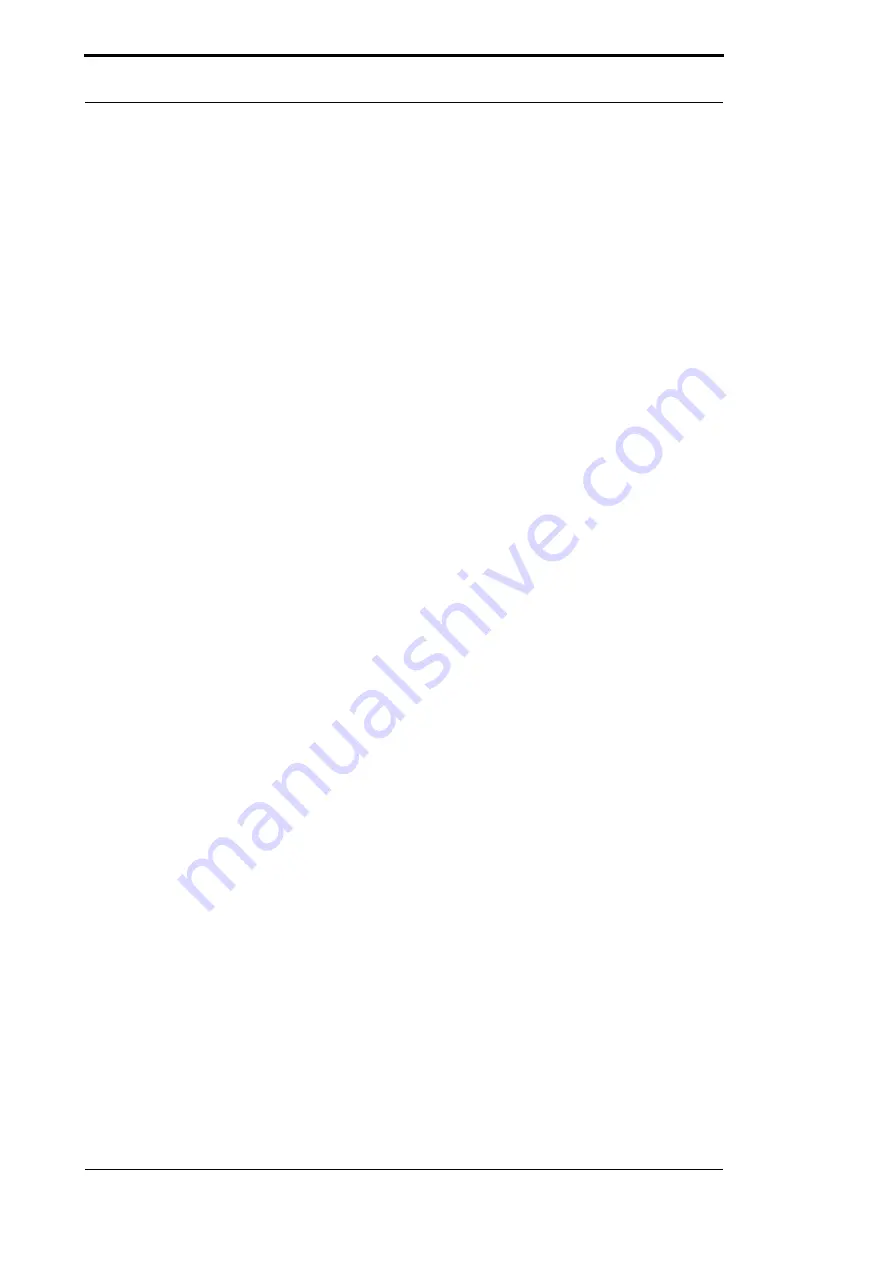
Basic device ROTARNOCK
Deutschmann Automation GmbH & Co. KG
12
Instruction manual ROTARNOCK 100 V. 3.6
4.12.20
3 Basic device ROTARNOCK
3.1 ROTARNOCK 100 (singleturn)
ROTARNOCK is a cam control integrated into the encoder housing, which, depending on the
device version, has 12 to 16 hardware outputs and, if supported, 32 software outputs. The tech-
nical data can be found in the appendix.
The programming takes place via a PC in connection with the software package "WINLOC32" or
via an external control unit, which however is not necessary for operation.
The connection between ROTARNOCK and a terminal or a PC is made either via an RS232
interface or via the DICNET bus (RS485) according to the chapter "Networking terminals with
cam controls and PCs". The devices of the ROTARNOCK series are also available with a
PROFIBUS or PROFINET connection. You can find more detailed information on this in the
"Cam controls with Fieldbus connection" user manual.
ROTARNOCK 100 with other bus systems on request.
3.1.1 Configuration via WINLOC 32
The ROTARNOCK 100 has, depending on the device version, a serial RS232 or an RS485
(DICNET) interface. With these, the ROTARNOCK can be configured using the WINLOC 32 soft-
ware. These include:
•
Dead time compensation: bit-wise, block-wise, block-wise I/O and bit-wise I/O. The delivery
status is bit-wise dead time compensation.
•
Logic inputs: (only ROTARNOCK with bus system)
•
Speed display: The scaling is freely adjustable, the default value is 60 revolutions/min.
•
Angle-time outputs: 16 available
•
Direction cams: This can be used to define whether cams of an output switch only in the
positive direction or only in the negative direction or in both directions (default).
3.1.2 ROTARNOCK 100-PB (PROFIBUS)
ROTARNOCK 100-PROFIBUS is a device optimized for Fieldbus connections with a high-end
performance range. 16 hardware outputs are supplemented by 32 software outputs available via
PROFIBUS to a total of 48. Angle-time cams and optionally 16 software inputs with logic functi-
ons and numerous other performance features characterize this device.
3.1.2.1
GSD file (PROFIBUS)
The ROTARNOCK can be preconfigured via the GSD file when it is integrated into the network
will. This creates a plug-and-play functionality. All parameters are exchanged
sent directly from the master to the new ROTARNOCK. Find the GSD file "R100.GSD"
On our homepage (www.deutschmann.de).
3.1.2.2
Configuration via PROFIBUS interface
The configuration via PROFIBUS is done directly via the communication profile for Deutschmann
Cam controls (see corresponding manual V2064) carried out.
Summary of Contents for ROTARNOCK 100
Page 2: ...Manual Art No V3408E...
Page 4: ...Deutschmann Automation GmbH Co KG 4 Instruction manual ROTARNOCK 100 V 3 6 4 12 20...
Page 57: ......
Page 58: ......