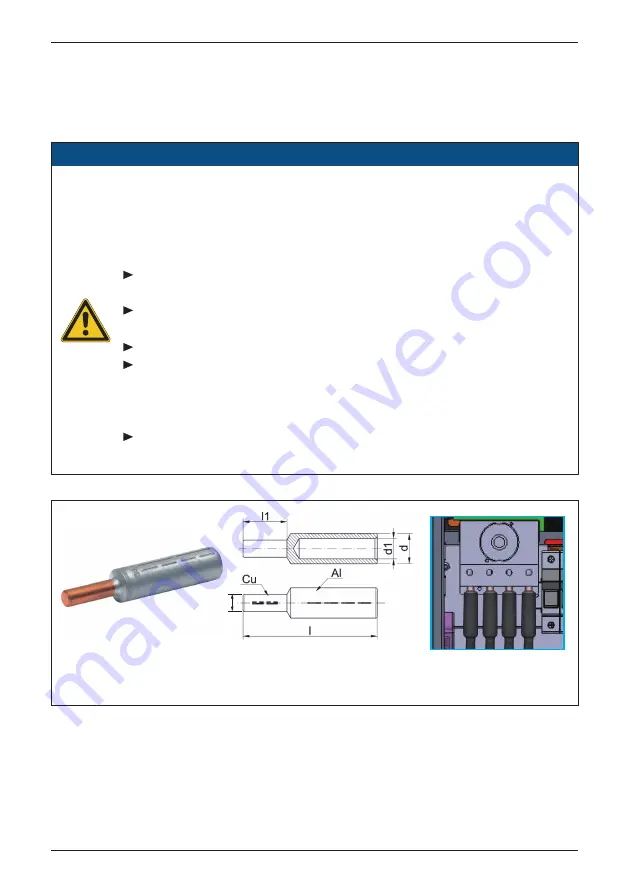
For AL AC wires:
To make sure good conductivity, bi-metal adapter must be used in conjunction
with aluminum wires.
Extreme temperature rise at the clamping point
If the contact resistance between the aluminum conductor and clamping point is too
high, the clamping point can become very hot and even catch fire in extreme cases.
To ensure a safe and reliable contact,
always
perform the following work steps:
Use a conductor cross-section at least one number larger due to the lower
current-carrying capacity.
Keep the installation location as free as possible from moisture or corrosive
atmospheres.
Connect the aluminum cables quickly.
Mechanically clean the stripped end of the aluminum conductor (using for instance
a knife blade to scrape off the oxide layer). Then immediately dip the aluminum
conductor into acid-fee and alkaline-free (=neutral) Vaseline and directly crimp
the aluminum wire with bi-metal adapter.
Tighten the clamping screw in the clamping body with the maximum permissible
tightening torque.
NOTICE
Figure 3-18 : Guideline for bi-metal adapter
Type: Compression joints
with Cu bolts, Al
For M80/60U, d
≦
18mm, e
≦
10mm
Heat-Shrinkable tube must be applied on Al part
e
41
Installation
Summary of Contents for M60U
Page 2: ......
Page 89: ...Figure 5 6 Remove screws as indicated unplug connectors DC SPDs AC SPDs 89 Maintenance...
Page 128: ......
Page 129: ......