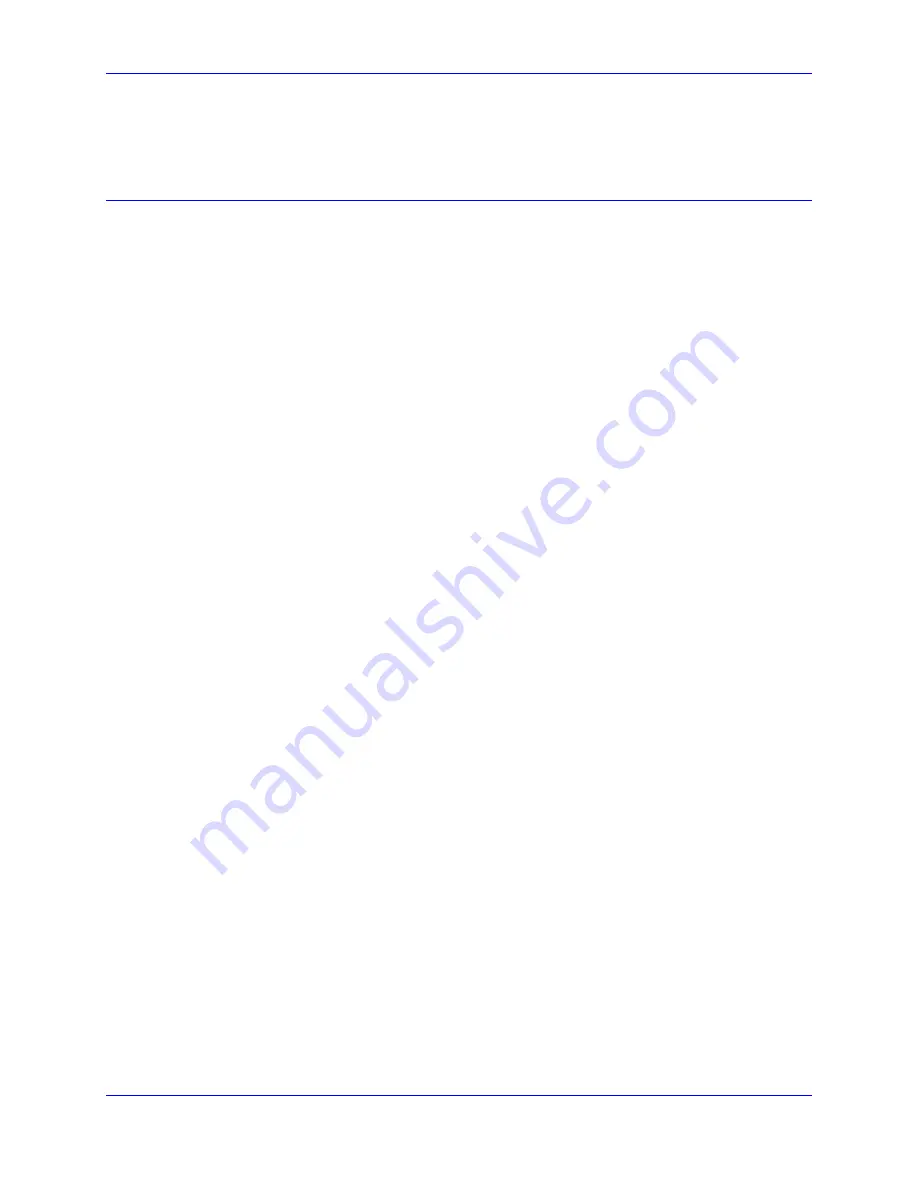
PMAC Quick Reference Guide
6
Introduction
The new yellow LED located beside the red and green LEDs, when lit, indicates that the phase-locked
loop that multiplies the CPU clock frequency from the crystal frequency on the Option CPU is
operational and stable. This indicator is for diagnostic purposes only; it may not be present on all boards.
Working with PMAC
When used for the first time, the card must be configured for a specific application, using both hardware
and software features, in order to run that application properly. PMAC is shipped from the factory with
defaults set in hardware and software set up to be satisfactory for the most common application types.
Working with PMAC is very simple and its ease of use and power is based in the following features:
•
A clever interrupt-driven scheme allows every task, each motion program and PLC, to run
independently of each other.
•
Pointer M-Variables allow monitoring virtually any register in PMAC’s memory from different
sources: motion programs, PLCs or the host computer.
•
Communications are activated continuously. At any moment, any variable or status command could
be interrogated.
•
Up to eight axes could be either synchronized together, controlled individually or in any combination
in between.
•
Data gathering and reporting functions allows saving data such as motion trajectories, velocity
profiles or any set of variables for later analysis and plot.
Hardware Setup
On the PMAC, there are many jumpers (pairs of metal prongs), called E-points (on the bottom board of the
PMAC STD they are called W-points). Some have been shorted together; others have been left open.
These jumpers customize the hardware features of the board for a given application. Check each jumper
configuration using the appropriate hardware reference for the particular PMAC being set. Further
instructions for the jumper setup can be found in the PMAC User manual. After all the jumpers have been
properly set, PMAC can be installed either inside the host computer or linked with a serial cable to it.
Software Setup
PMAC has a large set of Initialization parameters (I-Variables) that determine the personality of the card
for a specific application. Many of these are used to configure a motor properly. Once setup, these
variables may be stored in non-volatile EAROM memory (using the
SAVE
command) so the card is
always configured properly (PMAC loads the EAROM I-Variable values into RAM on power-up).
The easiest way to program, setup and troubleshoot PMAC is by using the PMAC Executive Program
PEWIN and its related add-on packages P1Setup and PMACPlot. PEWIN has the following main tools
and features:
•
The terminal window is the main channel of communication between the user and PMAC
•
Watch window for real-time system information and debugging
•
Position window for displaying the position, velocity and following error of all motors on the system
•
Several ways to tune PMAC systems
•
Interface for data gathering and plotting
In PEWIN, the value of an I-Variable may be queried simply by typing in the name of the I-Variable. For
instance, typing
I900<CR>
causes the value of the I900 to be returned. Change the value by typing in
the name, an equals sign, and the new value (e.g.
I900=3<CR>
). Remember that if any I-Variables are
changed during this setup, use the
SAVE
command before powering down or reset the card, or the
changes that have been made will be lost.
Summary of Contents for PMAC Mini
Page 4: ......
Page 8: ...PMAC Quick Reference Guide iv Table of Contents ...
Page 28: ...PMAC Quick Reference Guide 20 PMAC Executive Program PEWIN ...
Page 80: ...PMAC Quick Reference Guide 72 Troubleshooting ...
Page 82: ...PMAC Quick Reference Guide 74 Appendix A PMAC Error Code Summary ...
Page 88: ...PMAC Quick Reference Guide 80 Appendix B PMAC I Variables Summary ...
Page 106: ...PMAC Quick Reference Guide 98 Appendix F I O Suggested M Variable Definitions ...