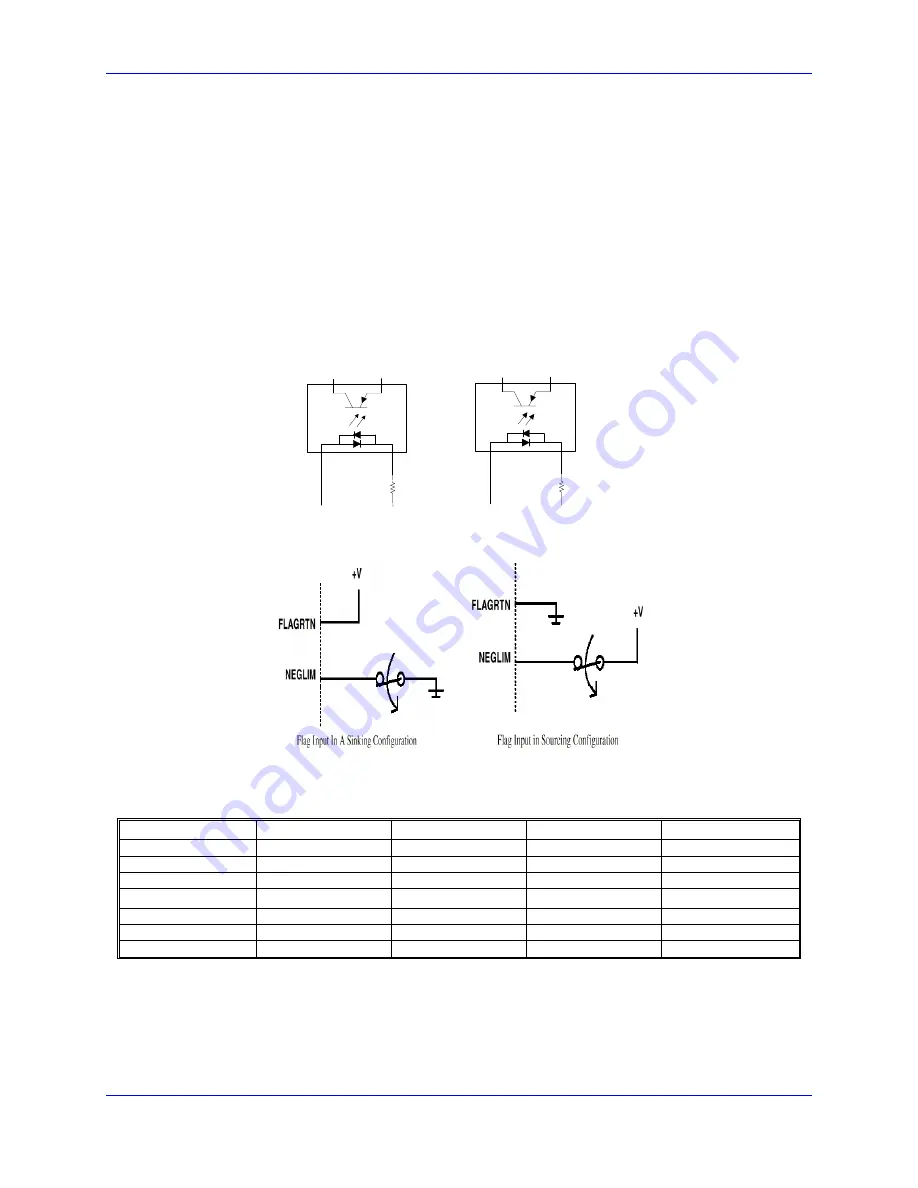
PMAC Quick Reference Guide
Installing and Configuring PMAC
25
Home Switches
While normally closed-to-ground switches are required for the overtravel limits inputs, the home switches
could be either normally closed or normally open types. The polarity is determined by the home sequence
setup, through the I-Variables
I902, I907, ... I977. However, for the following reasons, the same type of switches used for overtravel
limits are recommended:
•
Normally closed switches are proven to have greater electrical noise rejection than normally open
types.
•
Using the same type of switches for every input flag simplifies maintenance stock and replacements.
PMACPack and PMAC2 Flag Inputs
The PMAC Pack and PMAC2 interface accessories include a bipolar opto-isolating circuitry (chip PS-
2705-4NEC) for flag and amplifier fault connections:
+V
Flag
Return
Signal
Sinking Signal
(Gnd)
Gnd
Flag
Return
Signal
Sourcing Signal
(+V)
Examples:
Checking the Flag Inputs
In the PEWIN terminal window, define the following M-Variables for the flags of the motors under
consideration:
Flag Type
Motor #1
Motor #2
Motor #3
Motor #4
HMFL input status
M120->X:$C000,20,1 M220->X:$C004,20,1 M320->X:$C008,20,1 M420->X:$C00C,20,1
-LIM input status
M121->X:$C000,21,1 M221->X:$C004,21,1 M321->X:$C008,21,1 M421->X:$C00C,21,1
+LIM input status
M122->X:$C000,22,1 M222->X:$C004,22,1 M322->X:$C008,22,1 M422->X:$C00C,22,1
Flag Type
Motor #5
Motor #6
Motor #7
Motor #8
HMFL input status
M520->X:$C010,20,1 M620->X:$C014,20,1 M720->X:$C018,20,1 M820->X:$C01C,20,1
-LIM input status
M521->X:$C010,21,1 M621->X:$C014,21,1 M721->X:$C018,21,1 M821->X:$C01C,21,1
+LIM input status
M522->X:$C010,22,1 M622->X:$C014,22,1 M722->X:$C018,22,1 M822->X:$C01C,22,1
Open a Watch Window and press Insert to enter the M-Variable number to watch. Interacting with the
switch or sensor, monitor the change in the corresponding M-Variable. A value of zero indicates that the
flag is closed to ground and therefore the limit is not in fault, the motor will be able to run in that
direction (See
Ix25). If the value is 1, the flag is open instead.
Summary of Contents for PMAC Mini
Page 4: ......
Page 8: ...PMAC Quick Reference Guide iv Table of Contents ...
Page 28: ...PMAC Quick Reference Guide 20 PMAC Executive Program PEWIN ...
Page 80: ...PMAC Quick Reference Guide 72 Troubleshooting ...
Page 82: ...PMAC Quick Reference Guide 74 Appendix A PMAC Error Code Summary ...
Page 88: ...PMAC Quick Reference Guide 80 Appendix B PMAC I Variables Summary ...
Page 106: ...PMAC Quick Reference Guide 98 Appendix F I O Suggested M Variable Definitions ...