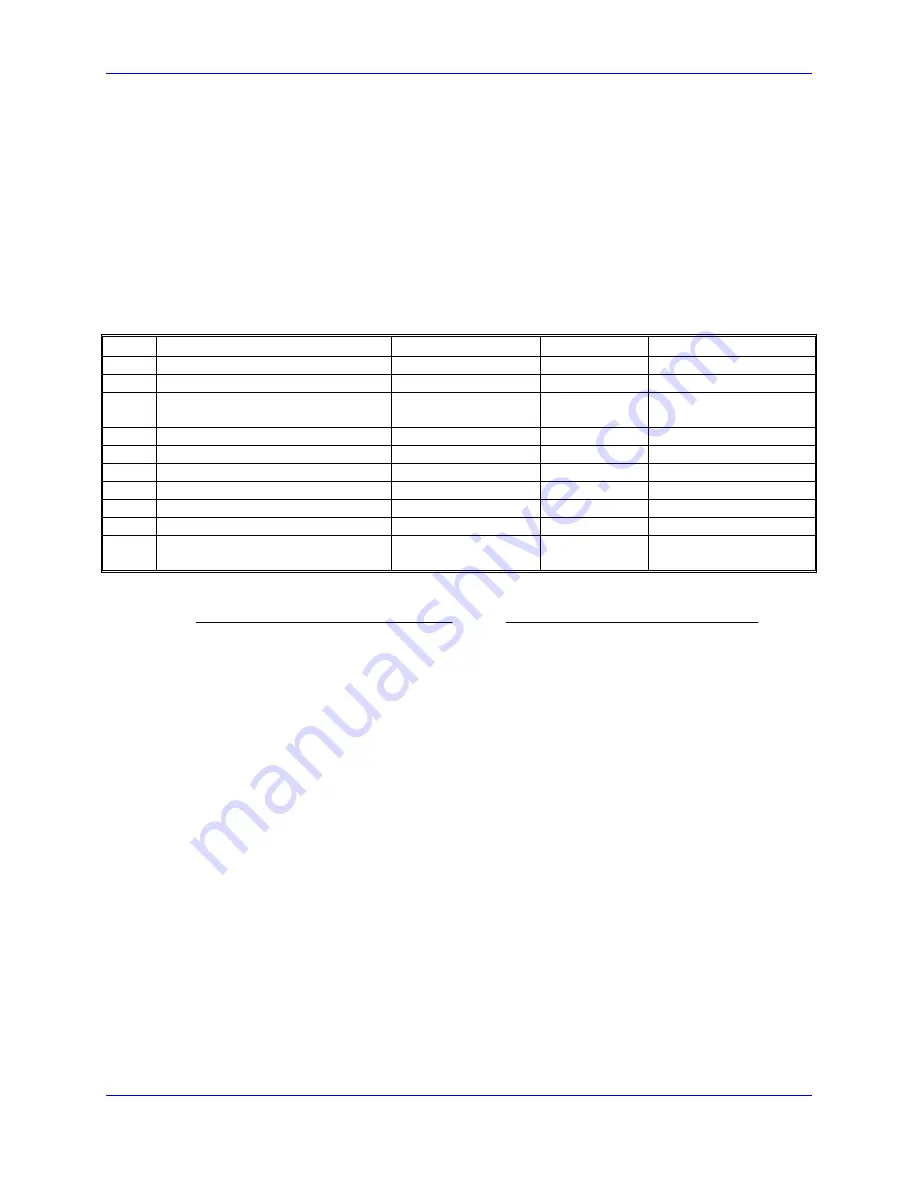
PMAC Quick Reference Guide
30
Installing and Configuring PMAC
Software Setup
PMAC has a large set of initialization parameters (I-Variables) that determine the personality of the card
for a specific application. Many of these are used to configure a motor properly. Using PEWIN, follow
these steps for Software Setup:
1. Fully reset PMAC to ensure a clean memory configuration before start:
$$$*** ;Global
Reset
P0..1023=0 Q0..1023=0
;Reset P-variables and Q-variables values
M0..1023->* M0..1023=0
;Reset M-variables definitions and values
UNDEFINE ALL
;Undefine Coordinate Systems
SAVE
;Save this initial, clean configuration
2. Define the safety I-Variables appropriately (x stands for the motor number, 1 through 8):
Motor Safety I-Variables Range
Default Units
Ix00 Motor x Activate
0 .. 1
0 (1 for Motor 1) none
Ix11 Motor x Fatal Following Error Limit 0 .. 8,388,607
32000
1/16 Count
Ix12 Motor x Warning Following Error
Limit
0 .. 8,388,607
16000
1/16 Count
Ix13 Motor x + Software Position Limit
+/- 2
47
0
(Disabled)
Encoder
Counts
Ix14 Motor x - Software Position Limit
+/- 2
47
0
(Disabled)
Encoder
Counts
Ix15 Motor x Abort/Lim Decel Rate
Positive floating point 0.25
Counts/msec
2
Ix16 Motor x Maximum Velocity
Positive floating point 32
Counts/msec
Ix17 Motor x Maximum Acceleration
Positive floating point 0.015625
Counts/msec
2
Ix19 Motor x Maximum Jog Acceleration Positive floating point 0.015625
Counts/msec
2
Ix25 Motor x Flag Address
PMAC X addresses
see Ix25 table
Extended legal PMAC X
addresses
For dual feedback systems:
encoder
velocity
the
of
Distance
of
Units
encoder
velocity
the
of
counts
of
Number
09
Ix
encoder
position
the
of
Distance
of
Units
encoder
position
the
of
counts
of
Number
08
Ix
⋅
=
⋅
3. Leave any loads disconnected from the motor at this point.
Test the polarity and functioning of the motor by means of open loop commands. For the open loop
command to work the overtravel limits must be either disabled (See Ix25) or properly connected.
Type the following in the terminal:
#1O10
; “Pound one, ‘O’ ten” will output 10% of the DAC on motor #1. It
; is about 0.6V on default settings
; <Observe the motor turning in the positive direction; the position
; window should indicate motor #1 counting up>
#1O-10 ; “Pound one, ‘O’ negative ten” will output a negative 10% of the
; DAC on motor #1, about -0.6V
<Observe the motor turning in the negative direction; the position
; window should indicate motor #1 decreasing>
If no motion is observed, slowly increase the percentage of the output command issued. If after 50% no
reaction of the motor occurred, check the DAC outputs following the guidelines in the previous sections.
4. Perform a tuning procedure as described in the PEWIN chapter.
5. After the tuning process has been completed satisfactory, check it by means of the following online
commands:
SAVE
;Save this setup
#1J+
;Jog Motor #1 continuously in the positive direction
#1J-
;Jog Motor #1 continuously in the negative direction
#1J=2000
;Jog Motor #1 to a known location
6. Create a PMAC memory backup file as described in the PEWIN chapter.
Summary of Contents for PMAC Mini
Page 4: ......
Page 8: ...PMAC Quick Reference Guide iv Table of Contents ...
Page 28: ...PMAC Quick Reference Guide 20 PMAC Executive Program PEWIN ...
Page 80: ...PMAC Quick Reference Guide 72 Troubleshooting ...
Page 82: ...PMAC Quick Reference Guide 74 Appendix A PMAC Error Code Summary ...
Page 88: ...PMAC Quick Reference Guide 80 Appendix B PMAC I Variables Summary ...
Page 106: ...PMAC Quick Reference Guide 98 Appendix F I O Suggested M Variable Definitions ...