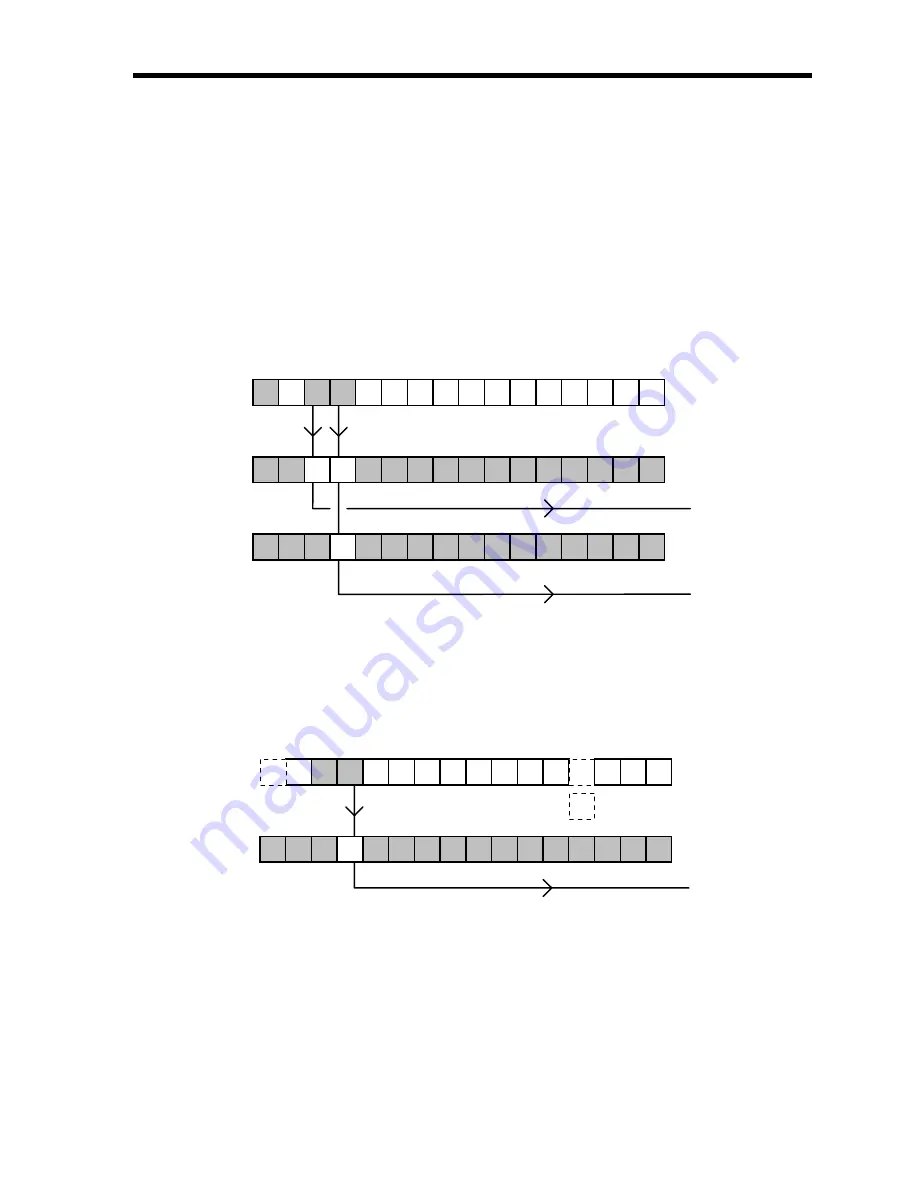
VMC 186/40 Motion Control Module Control Parameters
13
Estop Mask (Default: FFFFH Emergency stop disabled)
The bits in the
Estop Mask
field have a one-to-one correspondence with the bits in the
Status Word
. The bits in
this field are used to mask out the emergency stop that occurs when an error bit is set in the
Status Word
.
During an emergency stop, the drive output is immediately set to null and held there until a new command is
issued. To enable an emergency stop on an error condition, the appropriate bit must be
cleared
in both the
Halt
Mask
and the
Estop Mask
.
Halt Mask (Default: 0000H HALT enabled)
Like the
Estop Mask, t
he bits in the
Halt Mask
field have a one-to-one correspondence with the bits in the
Status Word
. The bits in this field are used to mask out the automatic halt that occurs when an error bit is set in
the
Status Word
. On start-up, this field is zero and any error will cause a halt. For applications where two or
more axes are moving together, the VME controller should mask out the automatic halts and take responsibility
for handling any errors. See the error handling section on page 30.
Status Word, Halt and Estop Masks
15
14
13
12
11
10
9
8
7
6
5
4
3
2
1
0
Halt Mask
15
14
13
12
11
10
9
8
7
6
5
4
3
2
1
0
Estop Mask
Axis
Emergency
Halt
Stop
= CFFF
= EFFF
Lead error causes a Halt and Overdrive causes an emergency stop
15
14
13
12
11
10
9
8
7
6
5
4
3
2
1
0
Status Word
= B000
Interrupt Mask (Default: FFFFH Interrupts disabled)
The bits in the
Interrupt Mask
are used to selectively enable interrupts. By clearing bit 12 of the mask, the
VMC 186/40 can generate a overdrive error interrupt when an overdrive condition is detected. This word only
needs to be used if the VME controller is configured to accept a bus interrupt. On start-up, this word is FFFFH.
Therefore, all of the interrupts are disabled.
15
14
13
12
11
10
9
8
7
6
5
4
3
2
1
0
Interrupt Mask
= EFFF
15
14
13
12
11
10
9
8
7
6
5
4
3
2
1
0
Status Word
= B000
Overdrive error causes a VME interrupt
VME
Interrupt
Will not
cause
an
interrupt