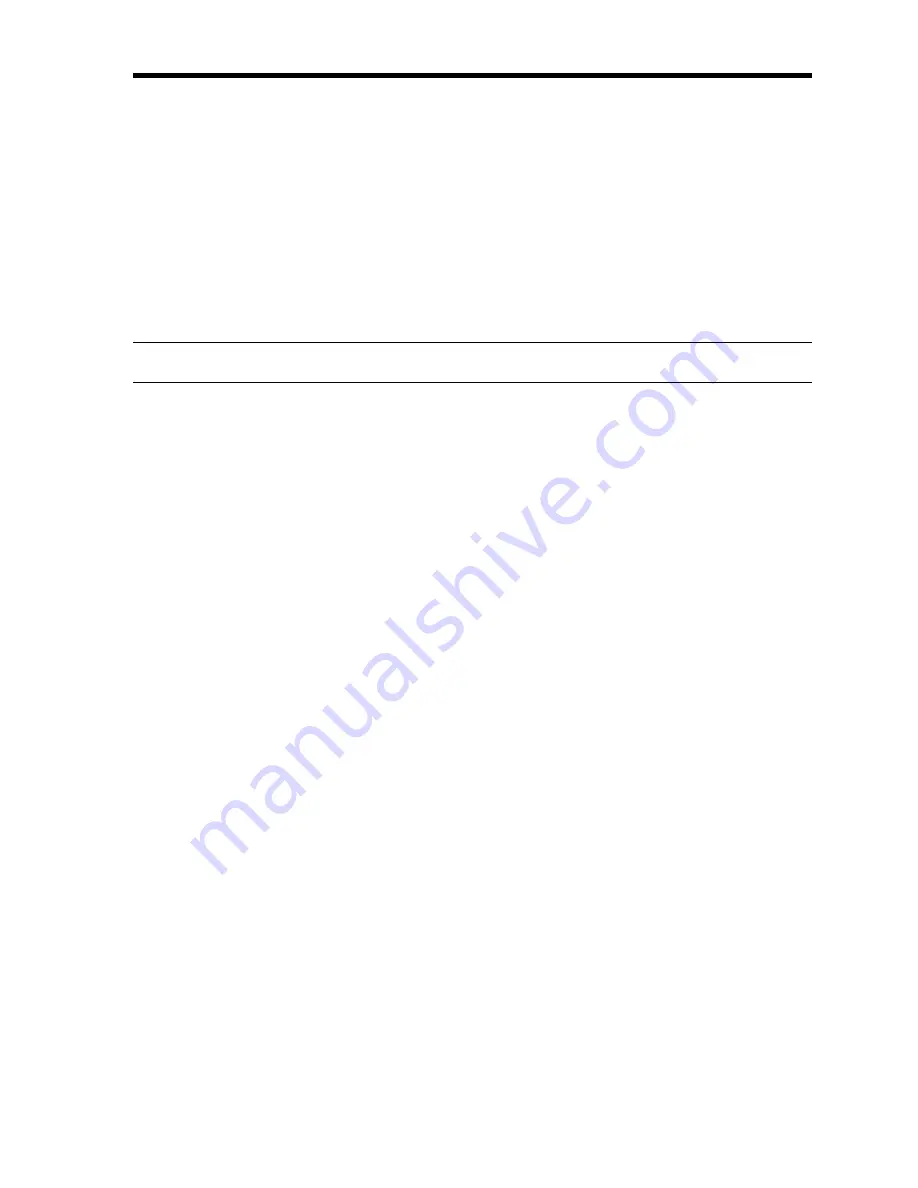
VMC 186/40 Motion Control Module Getting Started
29
Step 3 - Jogging the Axis
Jogging the axis can be accomplished by setting the
Requested Position
to the
Extend
or
Retract Limit
and
using the 'G' and 'H' commands repeatedly. This causes the motion controller to Go and Halt.
Step 4 - Tuning the Axis
It is best to use Delta's DCSMON program so moves can be plotted during the tuning process.
It will probably be necessary to mask off several bits in the
Halt Mask
while tuning the system to avoid
stopping every time an error occurs (see page 13 for
Halt Mask
information).
Note: Do not use the
Integral
or
Differential Gains
or
Feed Forward Advance
until you have finished with tips
1 to 10. Leave them at zero.
1
If the axis oscillates when it shouldn't be moving, reduce the
Static Gain
.
2
If the axis oscillates when it is extending, reduce the
Extend Gain
.
3
If the axis oscillates when it is retracting, reduce the
Retract Gain
.
4
Gains should be increased until the axis starts to oscillate, then follow tips 1 through 3.
5
If the axis gets a lead error and no lag error while extending, reduce the
Extend Feed Forward
.
6
If the axis gets a lag error and no lead error while extending, increase the
Extend Feed Forward
.
7
If the axis gets a lead error and no lag error while retracting, reduce the
Retract Feed Forward
.
8
If the axis gets a lag error and no lead error while retracting, increase the
Retract Feed Forward
.
9
If the axis gets both a lag error and a lead error, check for oscillations (tips 2 & 3). If it is not oscillating,
increase the
Maximum Position Error
until you get only one error (tips 5 - 8). Also check the
Feed
Forward Advance
(tip 14).
10
Once the axis moves smoothly, use the 'F' command (automatic tuning).
11
If the axis hunts around the set point, increase the
Hysteresis
slowly until the hunting stops or the axis
starts to oscillate. If oscillations occur, reduce the
Hysteresis
.
12 The
Null Update
should not be used until the
Hysteresis
is adjusted. Try to keep the
Null Update
interval
value higher than 1000. Systems with fast response times require larger
Null Update
intervals.
13
If the axis gets no lag or lead errors, reduce the
Maximum Position Error
until errors start to occur then
either tune the axis some more (tips 5 - 8), or increase the
Maximum Position Error
a little.
14 The
Feed Forward Advance
must be the same for all synchronized axes. Increasing the
Feed Forward
Advance
will decrease the chance of getting a lag error when ramping up or getting a lead error while
ramping down. If the
Feed Forward Advance
is too high, the axis will lead when ramping up and lag
when ramping down.
15 The
Integral Gain
is useful only when the feed forward terms can't be adjusted correctly. This may occur
if the upper limit of the feed forward is reached or the axis has a nonlinear response to drive output. If
the axis requires a different feed forward to move 10 inches a second than when moving 20 inches a
second, the axis is nonlinear and the integrator can help compensate. In these cases a little integral gain
will do the job. The better the feed forwards are adjusted, the lower the integral gain needs to be.
16
Another problem occurs on moves of a long duration and when the feed forward can't be adjusted high
enough. This usually happens only on systems that move less than 2 inches or 50 mm per second. If the
integrator must be used, increase by units of 50. Sometimes the integrator gain will get to 500 or more.
17 The
Differential Gain
is of little use on systems that respond quickly. It is most useful on systems with
slow response times that oscillate at 5 Hz or less. It adds a small boost while accelerating and helps stop
while decelerating. Increase this number by ones. The
Differential Gain
should not get over 10; high
values will cause oscillations.