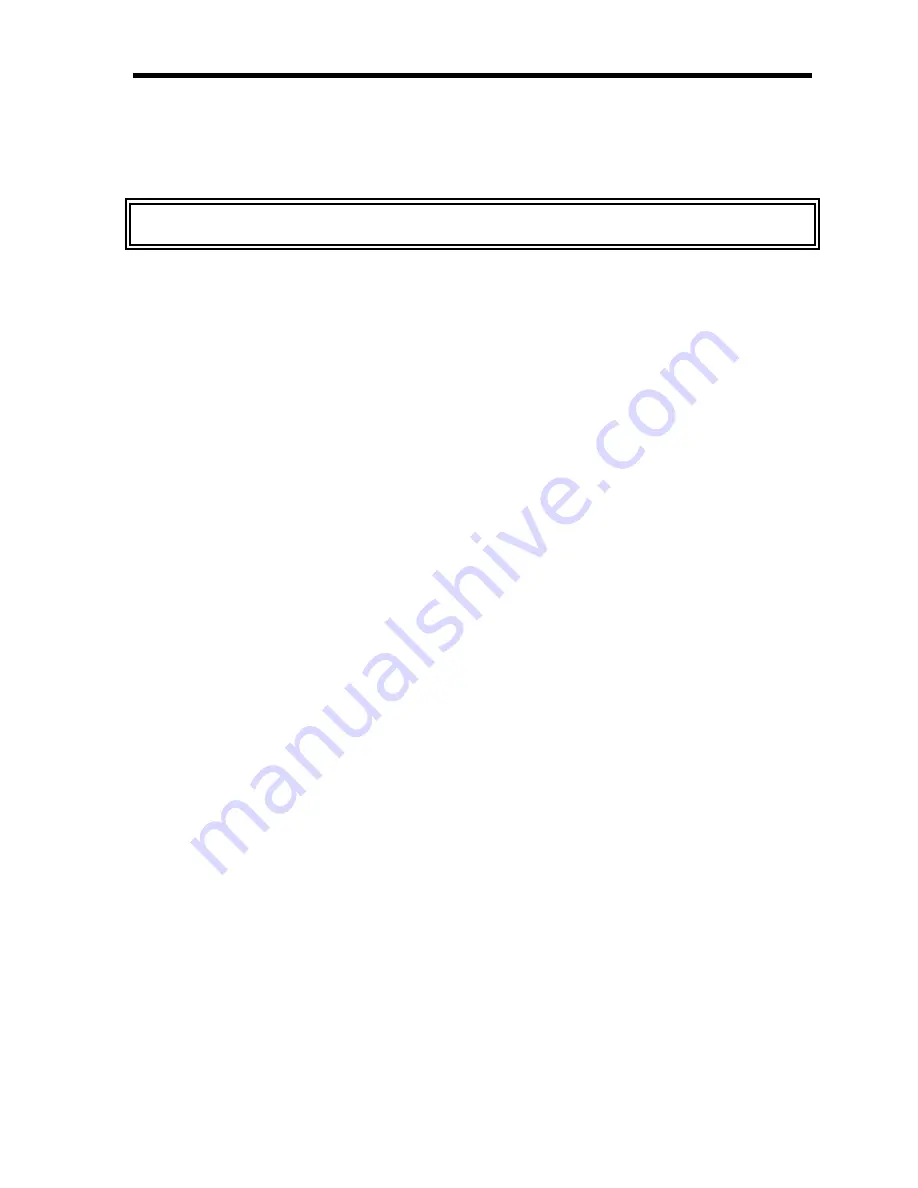
VMC 186/40 Motion Control Module Getting Started
30
VME Controller Programming Precautions
The VME Controller is responsible for:
•
Storing the parameters used by the VMC 186/40.
•
Making sure the motion controller is properly initialized.
CAUTION: The VME Controller is also responsible for issuing an 'H' or Halt command when drive power is
off. Also, to set the
New Null
when power is turned back on.
The motion controller provides a
Status Word
for each axis. Should an error bit be set in the
Status Word
, the
VME Controller is responsible for shutting down the axis drive power. The VME Controller should have a
watch dog timer that will shut down the drives if a time-out should occur.
VME Controller Error Handling
The VMC 186/40 reports errors within a millisecond. This is done by setting a bit in the axis
Status Word
and
flashing the appropriate Front Panel LED. The VME Controller is responsible for checking errors using the
Status Word
. It is up to the VME Controller to determine what should be done if an error is detected.
The system must have the capability to shut down the axis drive power using a normally open output which is
activated to close when the system is running. This contact should be in series with an operator emergency off
button. If power to the rack is lost, the contact will be deactivated and the axes will stop. If an error occurs on
the VMC 186/40, the contact can be deactivated, thus stopping the axes. Usually the VME Controller will not
take so drastic a step until it has determined that all control is lost. An 'H' or Halt command for the axis with an
error can take care of most error situations.
When two or more axes are moving in a coordinated manner and one axis starts moving slower than it should,
it is probably best to issue a Halt command to all the axes and stop operation until the problem with the faulty
axis has been solved.
It is also possible to use Estop and Halt on error detection by clearing the appropriate bits in the
Halt Mask
and
the
Estop Mask
corresponding to the error bits in the
Status Word
.
Key Items to Remember
•
Retracting is always toward the transmitter end of the magnetostrictive transducer.
(
Transducer Counts
decrease while retracting.)
•
The last 6 inches of the transducer are usually not usable.
•
Always know the position of the transducer transmitter because all positions between the transmitter
and the retract position will cause the axis to retract. Other positions outside the extend and retract
limits will cause the axis to extend.
•
When the direction is 0, all positions from the transmitter to the zero position should be thought of as
negative numbers. When the direction is 1, all positions from the transmitter to the end of the rod
should be considered negative numbers.
•
Linear transducer non-linearity may be a concern in applications where opposing axis are used.