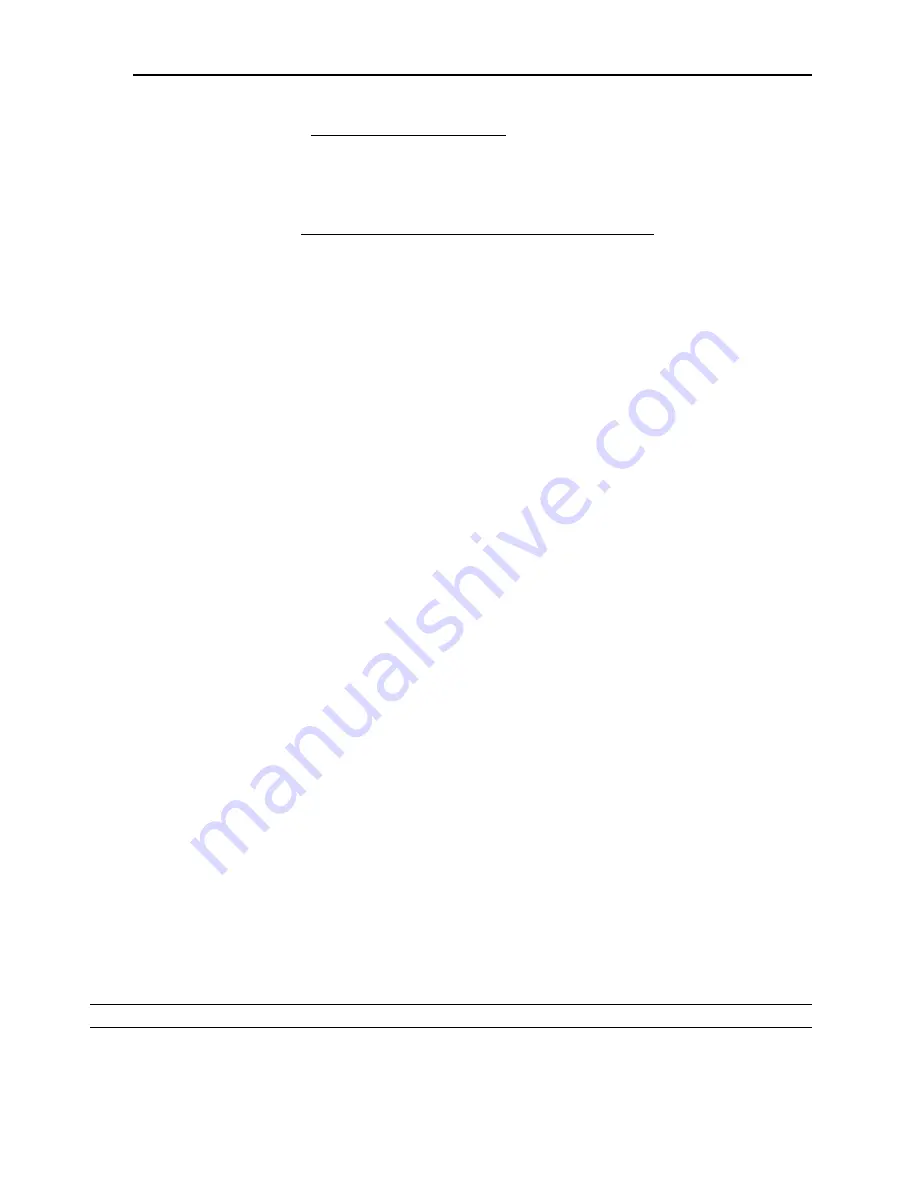
TMC 188/40 Motion Control Module
How It Works
Delta Computer Systems, Inc. 360/254-8688
45
Integral Drive = INTEGRAL GAIN x Accumulator
10,000
The differentiator looks at the difference between the target and actual speeds. The difference is
multiplied by the DIFFERENTIAL GAIN and divided by 100 to get the differentiator drive:
Differentiator Drive = (TARGET SPEED - ACTUAL SPEED) x DIFFERENTIAL GAIN
100
Feed Forward
When the axis is moving, the difference between the TARGET POSITION and the ACTUAL
POSITION may become large, even when the error gain is as high as it can be without causing
oscillation. There are three tuning parameters called EXTEND FEED FORWARD, RETRACT FEED
FORWARD, and FEED FORWARD ADVANCE that help reduce the difference between the ACTUAL
POSITION and TARGET POSITION.
The first two feed forward parameters compensate for the system's physical differences between
extending and retracting. Feed forward is an open loop drive output that is proportional to the
TARGET SPEED of the axis. The ACTUAL SPEED of the axis should be proportional to the drive
output. The difference between the TARGET SPEED and the ACTUAL SPEED should be small if the
feed forward is adjusted correctly.
Therefore, the difference between the TARGET POSITION and ACTUAL POSITION should be small
while the axis is moving. If the feed forward is too low, the ACTUAL POSITION will LAG the
TARGET POSITION. If it is too high, the ACTUAL POSITION will LEAD the TARGET POSITION and
the axis will overshoot the COMMAND POSITION.
If the axis response is very slow, the axis will overshoot even if the feed forwards are adjusted
correctly. This happens because the axis does not decelerate when the Motion Control Module
commands it. The TMC 188/40 can advance the feed forward component of the drive output so the
axis will decelerate at the proper time. The amount of advance is determined by the FEED
FORWARD ADVANCE parameter.
Control at Rest
When the TMC is controlling the position of an axis at rest, it uses three parameters:
PROPORTIONAL STATIC GAIN, NULL UPDATE and DIFFERENTIAL GAIN. The PROPORTIONAL
STATIC GAIN provides a drive output proportional to the error between the ACTUAL POSITION and
TARGET POSITION.
The NULL UPDATE compensates for the null offset inherent in many hydraulic valves. Every NULL
UPDATE period (see NULL UPDATE on page 28), one count of drive is added or subtracted to the
null drive value when there is a position error at set point. As long as there is an error, a count will be
added until it is corrected.
If the DIFFERENTIAL GAIN is set to a value greater than zero, the differentiator will influence the
drive when the axis is at rest. See page 29 for more information about the differentiator.
NOTE:
Axes will oscillate if the error gains are too high.