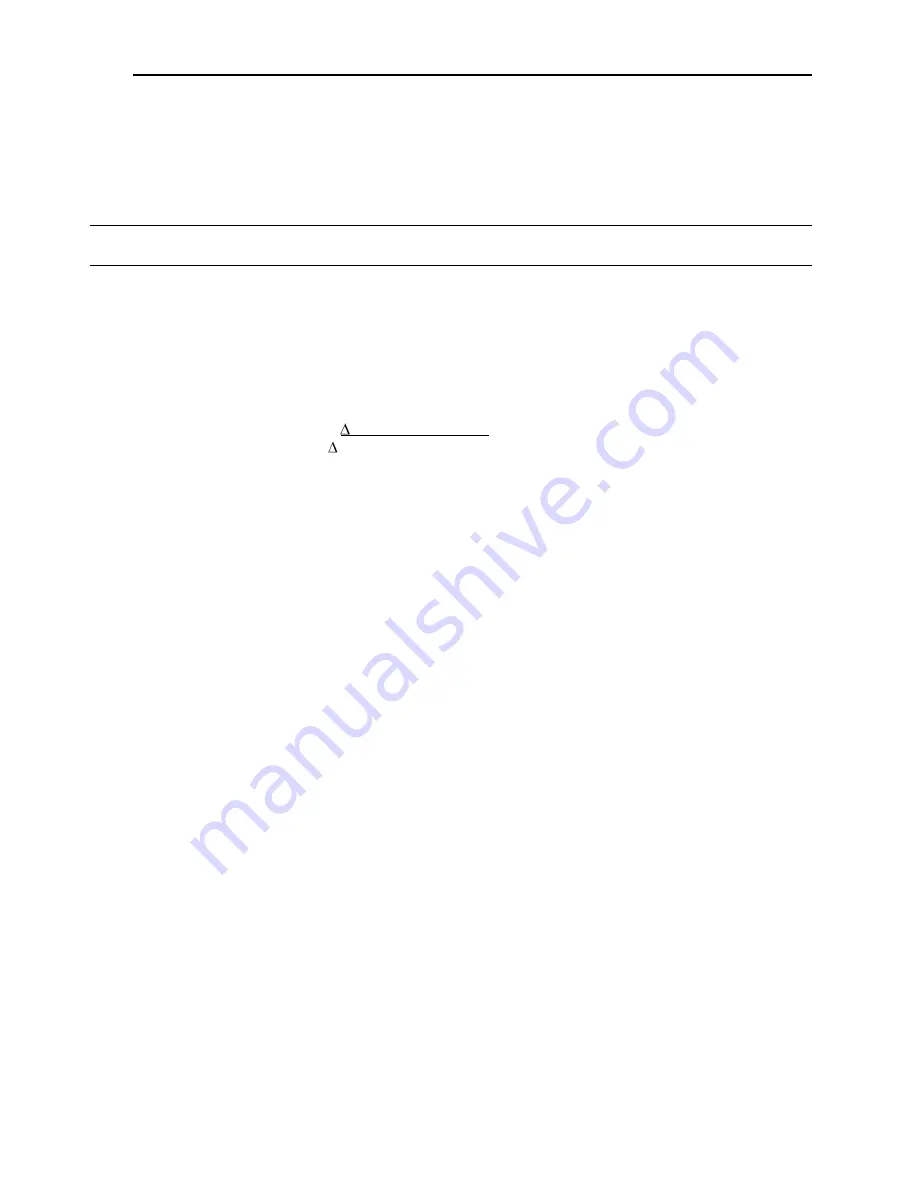
TMC 188/40 Motion Control Module
Appendix B: ASBX/40 Module
Delta Computer Systems, Inc. 360/254-8688
81
Setting the PRESSURE SCALE and PRESSURE OFFSET
When the ASBX/40 is shipped it is calibrated to produce 41 PRESSURE COUNTS at the low end of
the input range and 4055 PRESSURE COUNTS at the high end of the input range, for a span of 4014
PRESSURE COUNTS. This creates a 1% margin at each end of the scale to allow for drift in the
input signal or circuitry.
NOTE:
The span in PRESSURE COUNTS and the inherent offset must be considered when setting the
PRESSURE SCALE and PRESSURE OFFSET.
Using the TMC 188/40-TA
Each axis can be independently configured for position or pressure mode. When using an axis in
analog position mode (with the P4 jumper installed), the axis operates the same as with a
magnetostrictive transducer with two exceptions:
1) The SCALE parameter is defined as
SCALE = ACTUAL POSITION x 1000
TRANSDUCER COUNTS
2) The TRANSDUCER COUNTS is limited to 4095 because of the 12 bit resolution of the
analog to digital converter on the ASBX/40 module.
When using an axis in pressure mode (no jumper at P4), the axis can function as a standard axis by
clearing (entering a 0 at) bit 10 of the MODE Word, or an axis can control position and pressure by
setting bit 10 (to 1). With bit 10 set, the module will control position using a magnetostrictive
transducer until the pressure reaches PRESSURE LOW. At this point the axis starts controlling the
pressure. The motion of the axis is controlled so the pressure increases at the PRESSURE RAMP
rate until it reaches the PRESSURE COMMAND value. The pressure is then maintained until any of
the following conditions are met:
1) The PRESSURE COMMAND is changed; the axis then moves to ramp the pressure up or down
to the new PRESSURE COMMAND.
2) A new command is given instructing the axis to move back (bit 10 is cleared).
3) The pressure drops below the PRESSURE LOW value; the axis then switches from pressure
mode to magnetostrictive transducer position control, and it moves to the COMMAND POSITION.
4) The ACTUAL POSITION is the same as the COMMAND POSITION.
You can change three pressure parameters at any time without issuing a new command: PRESSURE
LOW, PRESSURE RAMP, and PRESSURE COMMAND. This allows you to follow pressure profiles
that can be dynamically updated.
A PID loop is implemented on the pressure control. The integral and differential terms allow the
controller to accurately maintain pressure while following a moving target. This is useful in
applications where an object is being simultaneously clamped and moved.