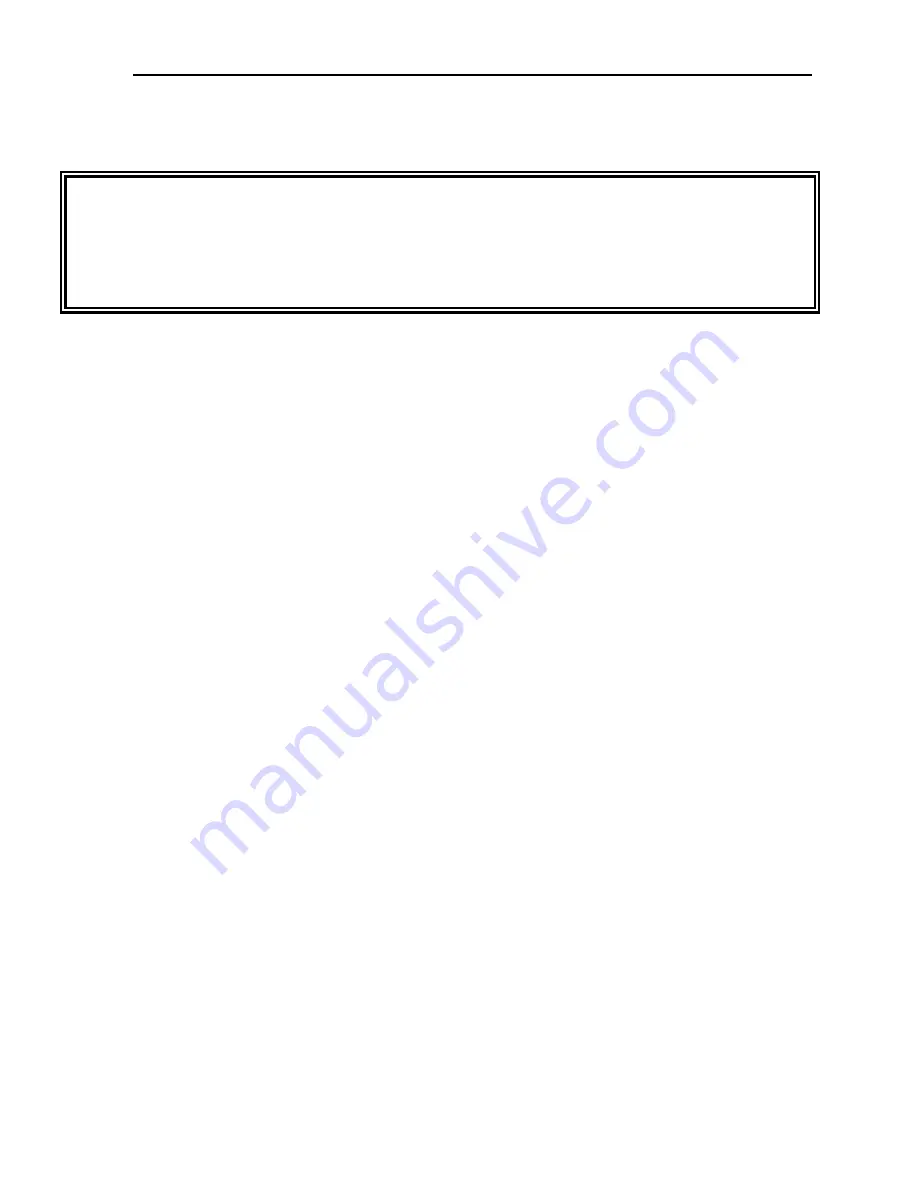
TMC 188/40 Motion Control Module
Getting Started
Delta Computer Systems, Inc. 360/254-8688
9
Getting Started and Tuning the Axis
CAUTION
: When starting the Motion Control Module for the first time, great care must be taken to avoid
accidents. The most common accident is a runaway. This is where the MCM tries to move the
axis to a position beyond it's physical limits.
MAKE SURE THE POWER TO THE DRIVE IS TURNED OFF
BEFORE STARTING THIS PROCEDURE!
Step 1 - Configuring The TMC Module
To configure the TMC module so it will work with your system, the following five steps must be taken.
See
Module Jumpers and External Wiring
(on page 47) and
TMC Wiring Diagrams
(on page 107)
for details about these steps.
1. Select voltage or current mode for the drive output of each axis (Default: current mode).
2. Select the drive level for each axis (Default: 50mA; range: 25, 50, 100mA or 2.5, 5, 10 volts)
3. Individually select each transducer interrogation pulse polarity (Default: Positive; Negative is
for short Temposonics® I rods only).
4. Individually select the number of recirculations used on each axis (Default: 4; Range: 1, 2, 4).
5. Wire the transducer and drive cables to your system.
Step 2 - Configuring the P/C Base
To configure the P/C so it will communicate with the TMC 188/40, the appropriate slot in the Base
must be initialized. To configure the P/C Base:
1. Run
TISOFT
software.
2. Put it in the
ONLINE
mode.
3. Enter the
CONFIO
menu.
4. Verify the appropriate slot is configured for eight
WY
registers with
SPECIAL FUNCTION
capability. This can be done manually or by doing a
READBS
.
5. Set the I/O address so it will not conflict with other I/O in the system. (The programs supplied
with DCSMON use WY201 through WY208. DCSMON is a monitor program included with
each Motion Control Module. See the DCSMON manual for more information.)
6. Update the information in the P/C by doing a
WRITPC
.
7. Initialize the
WY
registers as described in the next section.
Step 3 - Initializing the WY Registers
The eight WY registers must be initialized before the TMC 188/40 will begin normal operation. The
WY registers define the P/C's V Memory locations where the TMC 188/40 reads and writes
information. The initialization can be done either with the CHART utility of TISOFT or with a ladder
logic routine (see
filelist.txt
on the DCSMON disk for example ladder programs).