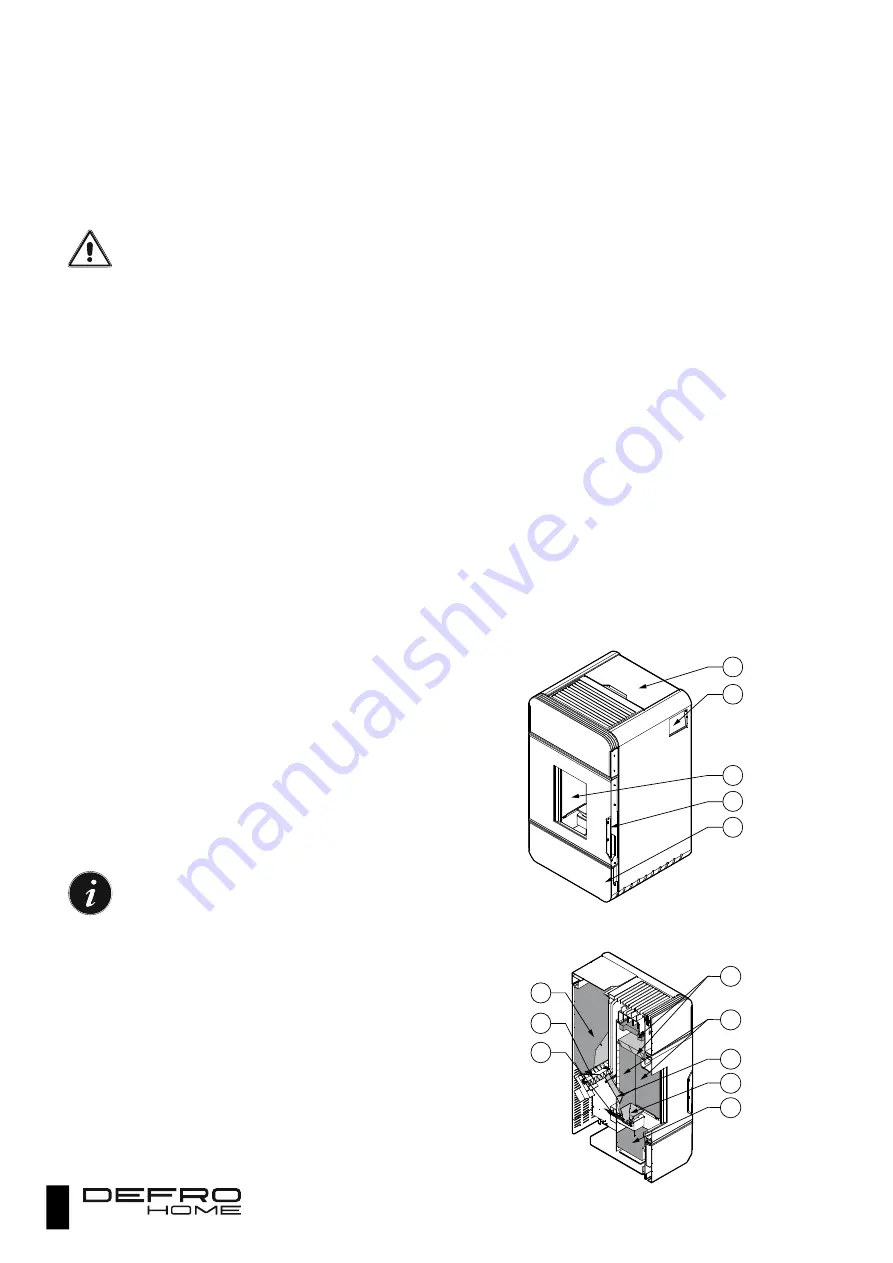
6
It is absolutely forbidden to use flammable liquid for
equipment firing up.
If the substrate, on which the equipment is located, is
made of inflammable materials, such as parquet or
floor lining then you should place protective plate un-
der it (the plate should protrude 250-300 mm from front
of the equipment).
2.2.
WARNINGS RELATED TO OPERATION
Equipment should be shutdown in case of failure or in-
correct operation.
Fuel used in the equipment should meet the conditions
described in this manual.
Internal parts of the equipment should not be washed
with water.
Avoid contact with water; above all do not wash any
painted surfaces until they are fully cured. Coating on
new devices is not an anti-corrosion coating; heat-re-
sistant paint achieves its protective properties only af-
ter curing under the influence of heat (after several ig-
nitions).
Do not expose the body to action of hot air for a long
period of time. Do not heat excessively the room where
you are staying and where the equipment is installed.
It may have adverse impact on physical condition and
be a reason for health problems.
Equipment should be installed in rooms with fire pro-
tection and equipped with all required components
such as supply (with air) and flue gas discharge.
Equipment and cladding made of ceramics should be
stored in rooms free from moisture and they cannot be
exposed to adverse effects of the weather.
It is not recommended to place body of the equipment
directly on the floor and if such floor is made of inflam-
mable materials it should be properly insulated.
To facilitate possible interventions by the technical
personnel you should not place the equipment inside
the closed rooms and just by the walls what can also
disturb air intake.
Always make sure and check whether doors of the
combustion chamber are tightly closed when the
equipment is operating.
Equipment consumes exact amount of air which is re-
quired for combustion process; it is recommended to
connect the equipment for air intake from outside us-
ing suitable pipe and through special outlet located at
the back of the equipment.
ADDITIONAL INFORMATION
In case of any problems you should contact sales out-
let or qualified personnel authorized by DEFRO. Re-
quest original spare parts if the repair is necessary.
Use only fuel with properties compatible with the rec-
ommendations of this operating manual.
Check and clean flue gas discharge ducts (connecting
piece to flue) periodically.
Store this manual carefully because it should be avail-
able for a whole period of equipment operation. In
case of sale of giving the equipment to the other user
you should always make sure whether the product has
the manual enclosed.
Request new copy from authorized sales outlet in DE-
FRO company if it has been lost.
3.
INTENDED USE
OMNIPELL dry stoves are intended for combustion of pellet. They
are intended for heating of houses and spaces where they are installed.
They can be also used as an additional source of thermal power.
Dry stove can be connected multiple times.
4.
TECHNICAL SPECIFICATION
4.1.
DESIGN
Dry stove fired with pellet operates as a heater for a room in which
it is installed. Hot air is emitted directly from the furnace through the
window panel and on by radiation through convection holes in the up-
per wall of the device.
Stove body (
3, picture 2
) - wall in contact with fire - is made of
heat-resistant steel sheet and sides of combustion chamber are lined
with cladding made of vermiculite (11). Body is lined with panels made
of steel sheet covered with high-temperature powder paint. Stove is
equipped with so-called combustion chamber.
Furnace chamber is equipped with discharge pellet (13) burner
adapted for combustion of biomass. Fuel required for combustion pro-
cess is transported using automatic feeder (17), which takes the pellet
from the container (1) located behind the combustion chamber. Igniter
(18) located in the furnace, in form of electric heater, initiates an ignition
of fuel supplied during start-up of the stove. Fuel required for combus-
tion is taken from air intake (8) and then supplied to the burner. Hot flue
gas flows around two deflectors (
10
), transfers heat in top, ribbed part
of the body, and then are discharged by vertical smoke pipes (
21
) to
bottom part of the stove. Air heated by the body is ejected through the
openings in top plate of stove housing. Flue gases from smoke pipes
are discharged to the chimney through a flue (9). Discharge process is
supported by a flue gas fan unit (20).
Combustion process in stove fired with pellet is adjusted by an
electronic controller (2) controlling operation of the igniter, feeder and
fan based on setpoints and measured temperature.
Picture 1 View of OMNIPELL dry stove.
2
1
5
6
7
10
11
12
13
14
16
17
18