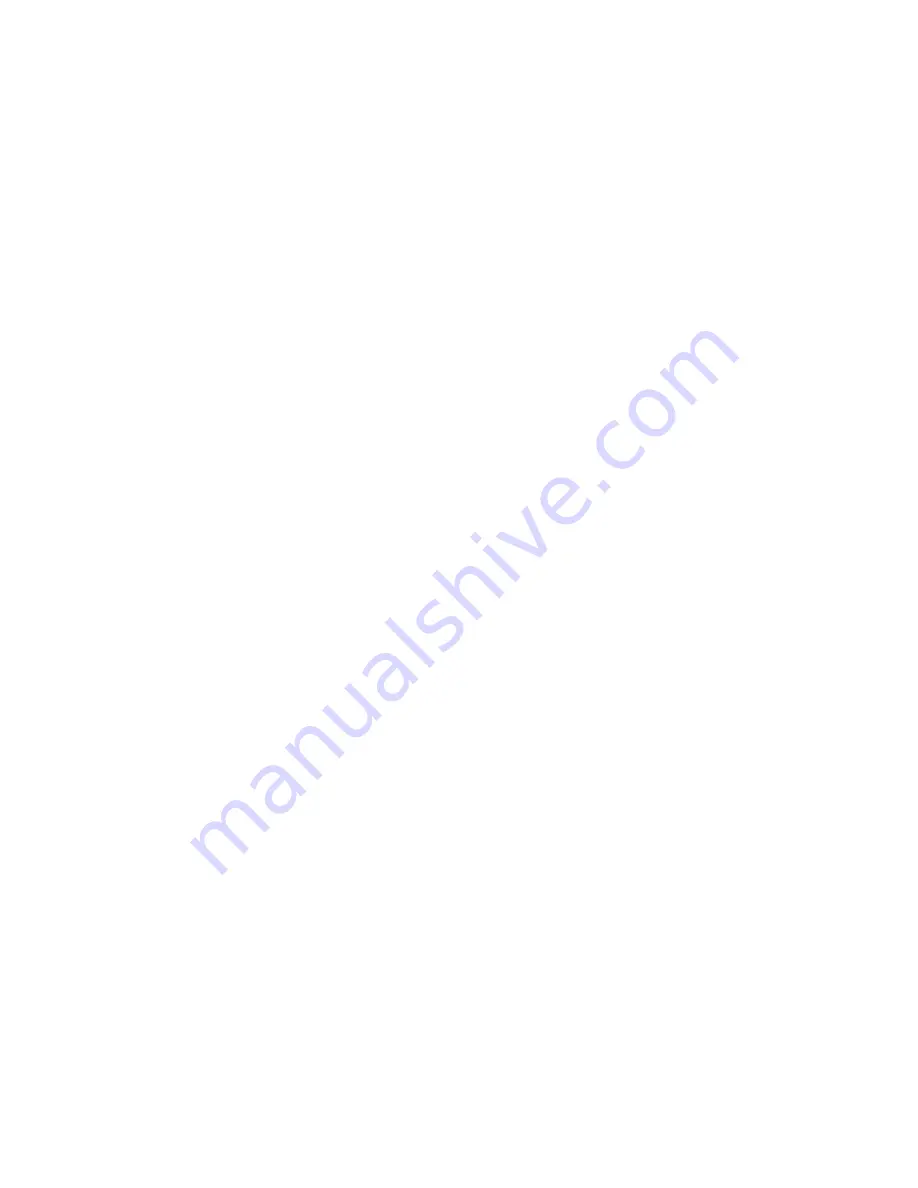
8
BEARINGS
The radial bearing (180) is lubricated by the liquid being pumped
and therefore needs no external lubrication.
The thrust bearing(s) (25A) are grease packed “for life” and require
no further lubrication until the pump is rebuilt.
The RWA2096 uses a “sealed for life” bearing that is packed with
grease by the ball bearing manufacturer.
The RWA4166 and RWA4206 have ball bearings that are hand
packed as an assembly procedure when the pump is assembled.
The grease is a lithium12-hydroxysterate soap-thickened grease
that has rust inhibitors and extreme pressure additives. This is a
NLGI, Grade 2, similar to:
Shell Oil Company’s “Alvania” Grease #EP2
or
Union Oil of California’s “Unoba EP” Grease Grade 2
Grease is also available from Dean Pump in individual containers.
one container is required for a RWA4166 pump. Two containers
are required for a RWA4206 pump. Order “RA3000” Grease #2
for bearing lubrication.
PUMP LUBRICATION
MECHANICAL SEAL
The “RWA” pumps are arranged with a mechanical face seal
(95A and 95B) that was specifically selected for sealing hot
water, hot solutions of ethylene glycol in water, hot solutions of
propylene glycol in water, and hot solutions of triethylene glycol
in water. The mechanical seal faces are lubricated by the liquid
being pumped – it is therefore necessary to have liquid at the
mechanical seal faces at all times. To accomplish this, the
mechanical seal cavity of the pump must be vented when
filling the pump with liquid (see FILLING below) to allow the seal
cavity to also fill with liquid.
When operating, these liquids may vaporize at the seal faces,
this vapor will be removed by the vapor eliminator mounted on
the top of the pump.
WARNING:
Vapor emitting from the vapor exhaust may be hot.
It is important that a pump should never be subjected to thermal or
pressure shock. The liquid should therefore be allowed to flow into
the casing slowly. A centrifugal pump should never be started until
all the parts are up to the temperature of the liquid to be pumped.
FILLING
The pump was shipped with the vapor eliminator and vapor
exhaust tube not installed. Do not install these until so directed.
WARNING:
Before filling the pump with liquid, check to see that all possible
leak locations are sealed. See that all of the connections into the
pressure containing cavity are sealed or connected to a related
piping system that also has all possible leak paths sealed. Do not
plug the pumpage leak detection connection, this must be left open.
Use a wrench on all bolted joints to apply torque to assure that all
gaskets are sealed in a tight joint. Check to see that all threaded
pipe connections are also tight enough to seal the liquid pressure
that will be applied when the system is started.
WARNING:
Filling directions below refer to venting of “air” to the atmosphere,
but dependent upon the physical properties of the liquid intended
to be pumped, temperature, pressure, and other variables related
to the system and its operational requirements, this may not be
allowed by federal or local regulations, or may not be acceptable
for whatever other reasons. Consult your plant or corporate safety
engineer for instruction on possible required procedures for the
specific liquid, operating conditions and legal requirements.
When the source of the liquid to be pumped is below atmospheric
pressure or located below the pump, the filling may be ac-
complished in any of several ways, three of which are listed below:
1) An exhauster may be connected to the discharge piping
between the pump and the discharge isolation valve. With the
discharge isolation valve closed and the suction valve open,
the air can be exhausted from the pump and the suction pip-
ing. When all the air has been removed, close the suction
valve, remove the exhauster, plug the access port where the
exhauster was connected, and then open the discharge valve.
Remove the pipe cap from the top of the pipe rising from the
pipe tee which also contains the seal vent plug, refer to the
“Small Piping Connections” drawing on page 7. Discard the
pipe cap. Allow the air to flow from this port until the pumpage
starts to flow. This could take considerable time as the radial
bearing clearance, through which the liquid must flow, is quite
small. Several minutes is not unusual although sometimes it
may vent in less than a minute. If the pump is a “RWA2096”,
use a funnel and fill the seal cavity through this connection with
clean pumpage. Install the vapor eliminator assembly into the
top of the pipe through which you were venting. Install the
vapor exhaust tubing into the top of the vapor eliminator. Refer
to the “Small Piping Connections” drawing on page 7.
At any time in the future, when the system is drained and the
pump needs filling, follow the above procedure except remove
the seal vent plug to vent the seal cavity and leave the vapor
eliminator intact.
2) With a foot valve installed in the suction piping, the pump may
be filled with pumpage introduced somewhere above the
pump in the discharge piping. A foot valve may create exten-
sive losses and therefore must be allowed for in calculation of
the available NPSH. When the pump is filled, plug the port
through which you were filling. Remove the pipe cap from the
top of the pipe rising from the pipe tee which also contains the
seal vent plug (refer to the “Small Piping Connections” draw-
ing on page 7). Discard the pipe cap. Allow the air to flow
from this port until the pumpage starts to flow. This could take
considerable time as the radial bearing clearance, through
which the liquid must flow, is quite small. Several minutes is not
unusual although sometimes it may vent in less than a minute.
If the pump is a “RWA2096”, use a funnel and fill the seal cav-
ity through this connection with clean pumpage. Install the
vapor eliminator assembly into the top of the pipe through
which you were venting. Install the vapor exhaust tubing into
the top of the vapor eliminator. Refer to the “Small Piping
Connections” drawing on page 7.
At any time in the future, when the system is drained and the
pump needs filling, follow the above procedure except remove
the seal vent plug to vent the seal cavity and leave the vapor
eliminator intact.
STARTING THE PUMP