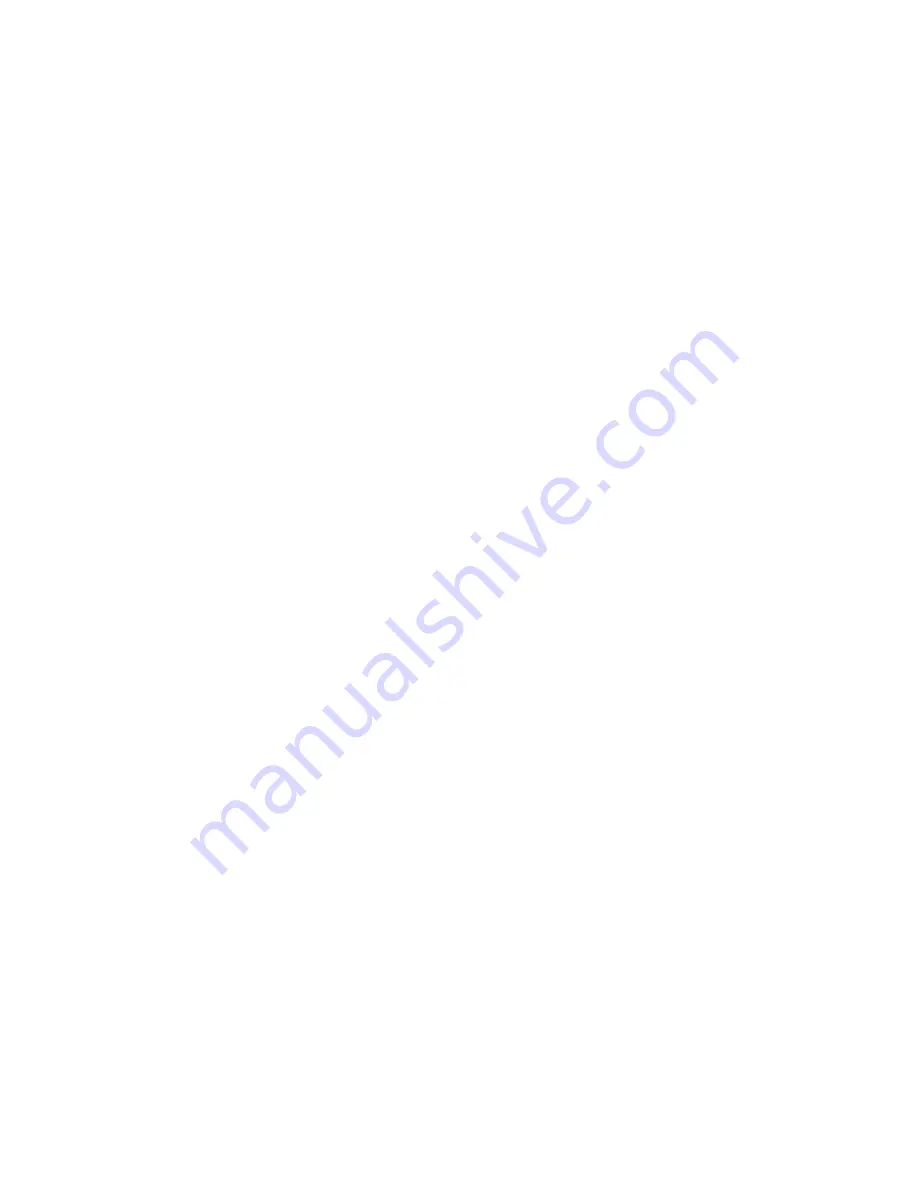
12
1
WARNING:
Work must be performed only by thoroughly trained and quali-
fied personnel to assure quality repair and to reduce the possi-
bilities of injury to personnel and/or damage to equipment. If
you do not have personnel who are capable of safe quality
repair of this equipment, we advise you to return the equipment
to DEAN PUMP to be repaired.
When it is necessary to open the pump and/or the pumping
system the fluid will be exposed to the atmosphere and
personnel in the area. For the safety of all involved, the risk of
exposure of personnel to the hazards of the pumpage can be
reduced by flushing the entire system with a compatible, non-
toxic, non-hazardous, stable fluid before opening the pump or
the system. In all cases, where the system is flushed or not, use
the utmost care around the pumpage and the pumping system.
Always wear the appropriate protective apparel when working
on or around the pumping equipment. Safety glasses with side
shields, heavy work gloves (use insulated work gloves when
handling hot items), steel-toed shoes, hard hat, and any other
protective gear as needed for protection. One example of
other gear would be breathing apparatus when working near
toxic materials.
Use only top quality tools.
a) Stop the pump. Turn off the power supply (electricity) to the
pump driver (motor) and lock the switching device so that it
can not be restarted. Tag the switching device so that no
one will attempt to restart the unit.
b) Close the suction and discharge valves completely to isolate
the pump from the system. Lock the valves in the closed posi-
tion and tag them so that no one will attempt to open them.
c) Turn off, lock out, and tag all sub-systems and auxiliary
equipment and auxiliary supply lines to isolate the pumping
unit from any and all power, energy, and/or fluids.
WARNING:
Do not attempt to perform any work on the unit until you are
confident that the pump and its contents have been stabilized at
ambient temperature, and atmospheric pressure.
Put on protective wear to protect human tissue from attack by the
fluids contained in the pump and any sub-systems, and from any
vapors or fumes that could possibly be released from these flu-
ids. This could mean breathing apparatus, face shields, heavy
long sleeve rubber gloves, rubber apron, hood, and possibly
more, dependent, of course, on the properties of the fluids
involved and the installed drain and vent piping arrangement.
Personal injury and/or death can occur if adequate precautions
are not taken with regard to the fluid, the installation and the
possibilities of the release of fluid, vapors, and/or fumes.
d) Remove the coupling guard. Remove the coupling spacer.
Be careful to not bend the blades of the fan (120). If the
pump is a RWA2096, the removal of the spacer will also
loosen the fan (120) from the face of the coupling hub.
e) Drain all the fluids from all the auxiliary sub-systems
(lubrication, cooling, heating, etc.) that are connected to the
pump. Drain each fluid into a separate container. Use
caution required for each fluid after reading the MSDS
(Material Safety Data Sheet) for each.
f) Flush each sub-system with a compatible, non-toxic, non-
hazardous, stable liquid. Drain into individual containers
for each fluid.
g) Carefully bleed off any pressure remaining in the pump.
Pressure remaining in the pump will be dependent upon the
pressure in the system when the pump was stopped; the
quality, type, and condition of the isolation valves; the thermal
expansion values of the fluid and the pump material; and the
change in the vapor pressure of the fluid between the temper-
ature at the time the isolation valves were closed and the
ambient temperature. Bleeding must be through a valved drain
line piped to a closed container mounted lower than the pump.
The container must be arranged with a relief passage to some
point where pressure and fumes will not be harmful to person-
nel. The container must also have a Level device so that
determination can be made that sufficient fluid has been
drained to empty the pump cavity and the volume of fluid that
was contained in the run of suction and discharge pipe
between the isolation valves and the pump. After the initial rush
of fluid from the pump relieves the pressure, the drain valve can
be opened further to speed the draining operation. When fluid
quits running into the drain tank, gauge the volume to see if it
is sufficient to have fully drained the contents of the pump and
the suction and discharge pipes between the isolation valves.
If the system was constructed without any drain connections, it
will be necessary to consult the designers of the system for safe
draining procedures.
h) Now drain any small piping that contains the fluid pumped from
all low points into the same container used to drain the pump.
Do not drain any other fluids (different then the pumpage) into
this container as they may not be compatible. Personal injury,
death, and/or equipment damage could occur.
WARNING:
Even though it might appear that the cavity being drained has com-
pletely drained, be extremely careful about opening the system
and/or opening the pump. If something solid in the pumpage
moves to the vicinity of the drain connection, it could seal-off the
drain and maintain pressure in the cavity thought to have been
drained. It is also possible that the isolation valves are not sealing
and therefore allowing liquid to flow from the system into the pump.
Personal injury, death and/or equipment damage may occur if
great caution is not exercised.
i) Remove the bolt(s) that retain the bearing housing foot (9) to
the baseplate. because of the above possibility, when you
loosen the gasketed joint at the back of the casing (5), loosen
the casing capscrews (5D) of the RWA2096 or the casing nuts
of the RWA4166 or the RWA4206, only one full turn. Then use
jackscrews (two, 180
º
apart) through the flange of the bearing
housing (26) to “break” the gasket seal. The bearing housing
flange of the RWA2096 and RWA4166 pumps have tapped
holes for
1/2
” - 13 UNC screws, the RWA4206 has
5/8
” - 11
UNC. If fluid and/or pressure remains in the pump, it will
spray out now. Use extreme caution, wearing protective gear,
to avoid injury. Do not proceed with disassembly until leakage
ceases completely. If leakage does not cease, the isolation
valves may not be sealing. Note that if the pump was
purchased without a drain, the pump will contain fluid which
will flow out at the time the nuts or capscrews are loosened and
the gasket seal is “broken”.
WARNING:
When you open the pump, the fluid will be exposed to the atmos-
phere and personnel in the area. For the safety of all involved, the
risk of exposure can be reduced by flushing the cavity that was just
drained with a compatible, non-toxic, non-hazardous, stable liquid,
before disassembling the pump.
DISASSEMBLY AND REASSEMBLY PROCEDURES