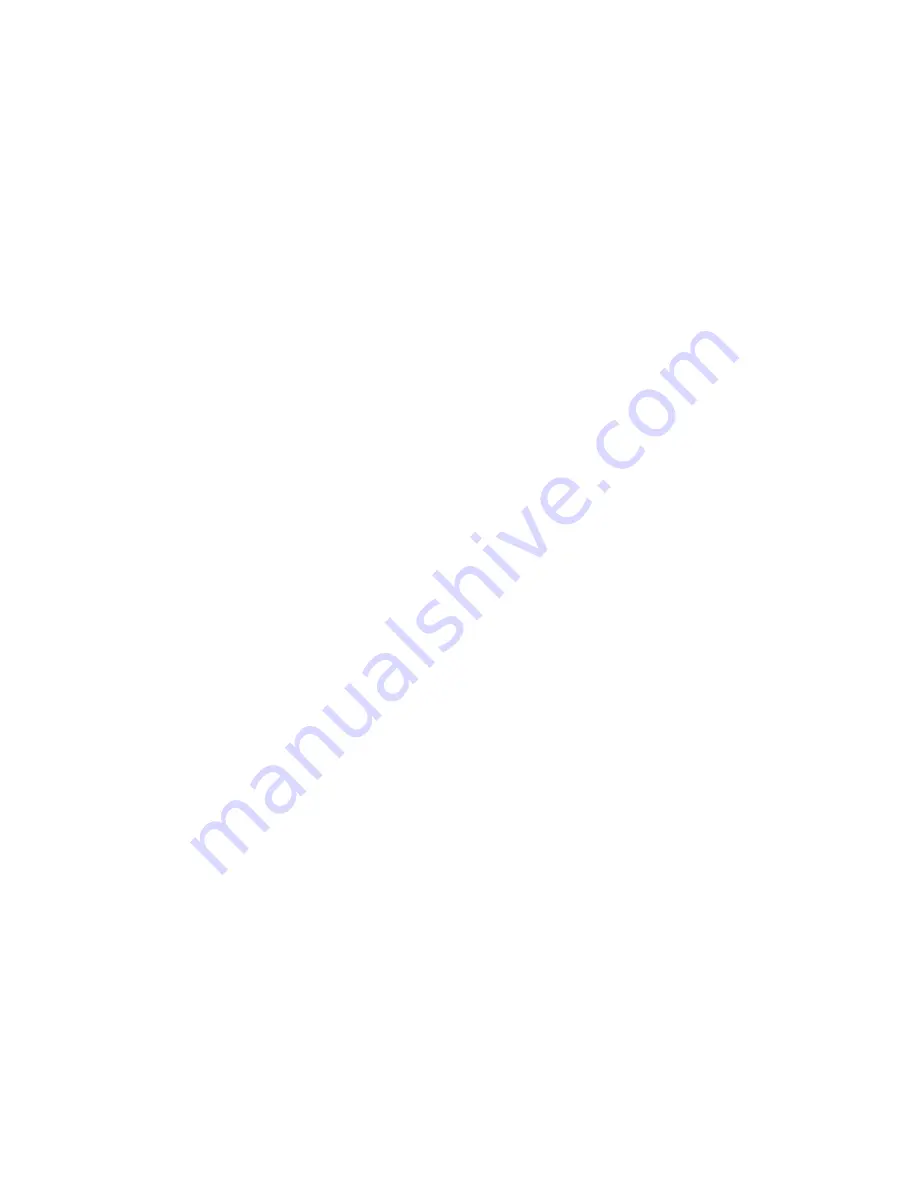
2
The Products of Dean Pump Division are subject to thorough and
rigorous quality control and inspection procedures throughout the
whole of the manufacturing process to assure proper operation in
full conformity with established performance standards. On
completion of inspection, each unit is sprayed internally with rust
inhibitor (if material is subject to atmospheric corrosion),
sealed against the entrance of dirt, and tagged with a signed
certificate of inspection prior to shipment. Each pump when shipped
is ready to perform the service for which it was designed
with minimum maintenance and expense if properly installed and
operated in accordance with the instructions furnished.
PRODUCT INSPECTION AND TEST
Read the instruction manual completely before installing, filling,
operating, or maintaining this equipment.
Obtain, read and heed the MSDS (Material Safety Data Sheet) for
the fluids being handled before attempting to fill, operate or main-
tain this equipment. Obtain instructions from the Safety Engineer
responsible for your facility before performing any work on the
pumping equipment and systems.
Proper storage while not in use and proper installation and startup
are essential for successful pump operation. Misuse or improper
storage, installation or operation of pumps may result in serious loss
or damage. Dean Pump Division is not responsible for any loss or
damage resulting from causes beyond its control, and is not liable
for charges for work performed or materials furnished to repair such
loss or damage.
All installation, operation, and maintenance must be done by thor-
oughly qualified personnel in strict accordance with this manual and
must comply with all local, state and Federal codes. Only Dean
authorized service parts must be used in the repair of these pumps.
RECEIVING PUMP
When the pump is received from the transportation company it
should be promptly inspected for damage and such damage noted
on the bill of lading before it is signed. Claims for shipping damage
must be filed against the carrier.
Care must be exercised in unloading and handling the pump.
STORAGE
Pumps must be properly covered and protected against moisture,
dirt, and physical damage during storage prior to installation.
If prolonged storage is anticipated, do the following:
1) Remove the vapor eliminator from the pipe tee into which it
is mounted. Wrap and box the vapor eliminator and store it
in a clean dry place.
2) Seal the suction opening of the pump with a blind flange,
gasket, and bolts.
3) Fill through the discharge opening of the pump with a
corrosion inhibiting liquid that is also compatible with the
liquid that will later be pumped. Evaluation of compatibility
must include consideration of the temperature at which the
system will later operate. Fill the pump until the liquid flows
from the pipe tee from which the vapor eliminator was
removed. Plug the top of the pipe tee with a NPT pipe plug.
4) Continue filling through the discharge opening until the
pump is completely filled.
5) Seal the discharge opening with a blind flange, gasket,
and bolts.
6) Remove the pumpage leak detection pipe from the bottom of
the bearing housing. Apply pipe sealant to a
3/8
” NPT pipe
plug, and tighten it into this opening. Save the pipe that was
removed, so that it may be re-installed when the pump is
placed into service.
7) Remove the gland vent plug from the top of the bearing
housing and fill the gland cavity, through this opening, with
a standard SAE 10 weight oil. When full, replace the
3/8
”
NPT pipe plug.
8) Remove the bearing end cover (28) and fill the center
pocket of the end cover with the grease described under
“PUMP LUBRICATION”. Replace and secure the end cover.
9) Apply a heavy protective coating to all exposed machined
surfaces. A rust preventive must be used to protect all steel
and iron parts.
10) Rotate the pump shaft “by hand” each month. Wear heavy
gloves when rotating the shaft to protect your hands.
When you are ready to place the pump in service;
1) Remove the bearing end cover (28). Remove and discard
about one half of the grease that is in the end cover. Replace
and secure the end cover (see assembly instructions). Be sure
to comply with all government regulations in the disposal of
the grease.
2) Remove the plug that was installed into the pumpage leak
detection connection. Drain and discard the storage liquid.
Re-install the leak detection pipe. Be sure to comply with all
governmental regulations in disposal of the storage liquid.
3) Remove and discard the discharge bolts, nuts, blind flange,
and gasket. Remove the casing drain plug. Remove and
discard, the NPT plug from the top connection of the pipe tee
(into which the vapor eliminator mounts). Drain and discard
the storage liquid. Remove and discard the suction bolts,
blind flange, and gasket. Stand the pump up on its
suction flange to allow residual liquid to drain. Flush all
remains of the storage liquid from the pump. Use a flush
liquid that is compatible with the pumpage, as any flush
liquid remaining in the pump when it is placed in operation,
will be exposed to the operating temperatures and pressures.
Vapor pressure is “one” of the critical properties to be
considered. Be sure to comply with all governmental
regulations in disposal of the storage liquid, flush liquid,
and gaskets.
WARNING
HAZARDOUS SITUATIONS MAY OCCUR UNLESS THIS EQUIPMENT IS APPLIED, INSTALLED, OPERATED,
AND MAINTAINED BY THOROUGHLY QUALIFIED PERSONNEL IN STRICT ACCORDANCE WITH THE
INSTRUCTION MANUAL AND ALL APPLICABLE DRAWINGS AND CODES.