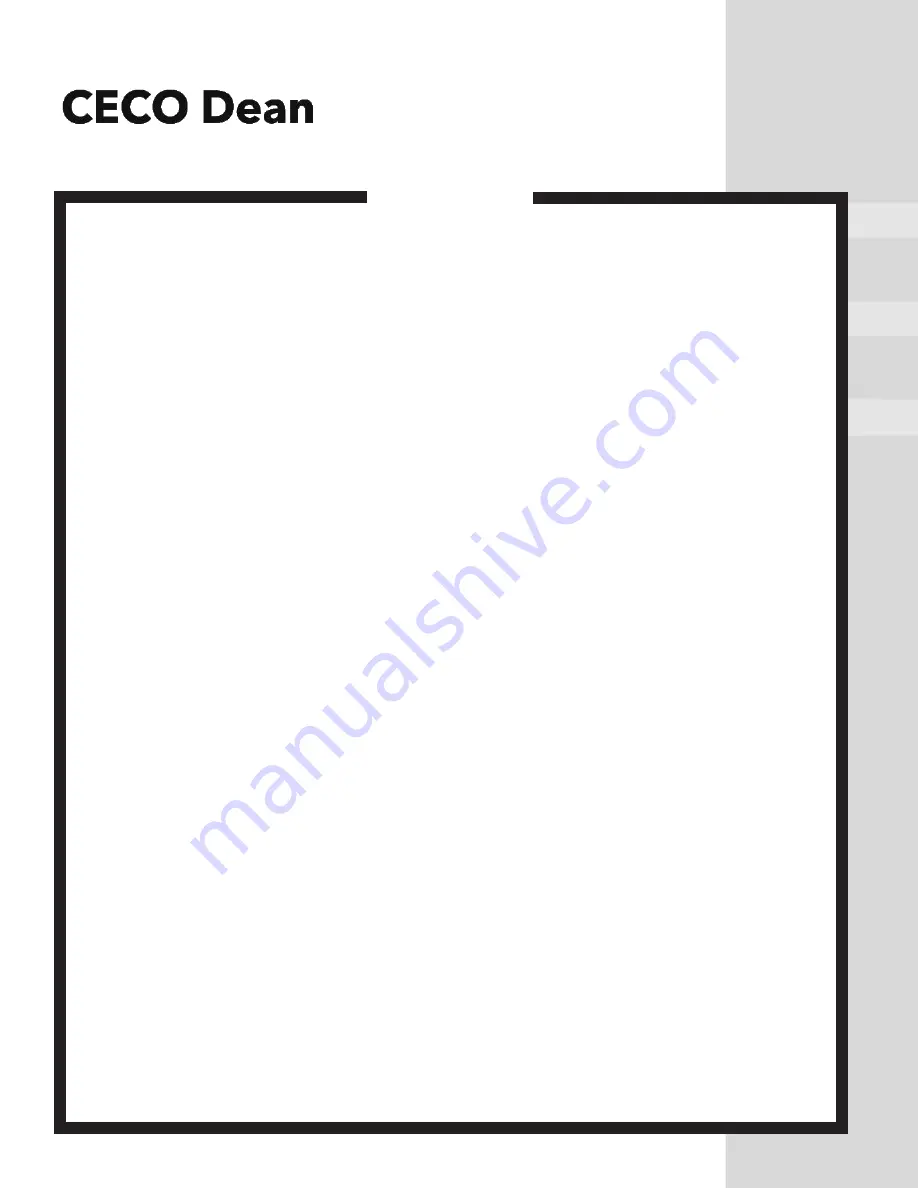
©COPYRIGHT 2007
CECO ENVIRONMENTAL
, DEAN PUMP DIVISION
Dean Pump Division
®
IS A REGISTERED TRADEMARK OF
CECO ENVIRONMENTAL
09-5952 307
6040 Guion Road Indianapolis, IN 46254
Phone: (317) 293-2930 FAX: (317) 297-7028
E-Mail:
.com Web Site: www.
cecoenviro
.com
Read the instruction manual completely, before installing, filling, operating, or maintaining this equipment.
Obtain, read, and heed the MSDS ( Material Safety Data Sheet) for the fluids being handled before attempting to
fill, operate or maintain this equipment.
Obtain instructions from the Safety Engineer responsible for your facility before performing any work on the pump-
ing equipment and systems.
APPLICATION AND REAPPLICATION - At the time of installation, the equipment received should have already been
selected for the service required. You must read the paperwork for the installation and check serial number of the
pump to assure that you are installing the correct pump into the service for which it was selected.
Many pumps look identical from the outside but can be made of different materials and/or be constructed differently
inside. Personal injury, death, equipment damage, product (pumpage) damage, and/or product loss could occur if the
incorrect pump is installed.
Do not transfer an existing pump to any other service conditions until you have thoroughly reviewed the pump
construction, materials, sizing, sealing, pressure containing capability, head/capacity capability, and
temperature capability with respect to the required service. Consult your DEAN PUMP sales engineer with all the
service requirements and a full description of the existing pump (including the serial number), seal, and sub-systems
so that we can assist you in a successful reapplication.
INSTALLATION - Always wear the appropriate protective apparel when working on or around the pumping equipment.
Safety glasses with side shields, heavy work gloves (use insulated work gloves when handling hot items), steel toed
shoes, hard hat, and any other protective gear as needed for protection. One example of other gear would be
breathing apparatus when working near toxic materials.
Use lifting devices, manufactured expressly for the purpose of lifting, to move the pumping machinery. Do not attempt
to lift the assembly or its components manually. Use only devices with lifting capabilities in excess of the weight of
the unit being lifted. Inspect straps,chains, hooks, etc. for damage and lifting capability before use. Lift only at the
center of gravity.
Personal injury, death, and/or equipment damage could occur if good lifting practices are not used.
Install the equipment on a properly designed and built foundation. Assure that the driver (motor, turbine,or engine)
shaft is properly aligned to the pump shaft.
Connect the suction and discharge piping without forcing the piping into position. The pipe flanges must line up
with the pump flanges “freely”. Strain caused by “forcing” and/or misalignment may cause failure of the pumping
unit, flanges, and/or the piping resulting in fluid (pumpage) release. This could cause personal injury, death and/or
damage to this and/or other equipment.
Install a “new” bolt, of the correct size per ASME/ANSI B16.5 and the correct material per ASME/ANSI B16.5,
in every bolt hole. Tighten all bolts evenly. Use only new uncorroded fasteners.
Improper flange bolting may cause failure of the pumping unit, flanges, piping, and/or fluid (pumpage) release
which could cause personal injury, death, and/or damage to this and/or other equipment.
Connect all other (auxiliary) piping necessary for safe and successful operation of the equipment in the specific ser-
vice conditions of the application. Make sure that all piping is installed into it’s correct connection. Installation of a
pipe into an incorrect location could result in an explosion and personal injury or death as well as damage to this
and/or other equipment.
Install pressure relief valves in any cavities that could be subjected to pressures in excess of the allowable working
pressure of that cavity. Explosion, personal injury, death, and/or damage to this and/or other equipment may occur
if pressure exceeds allowable.
Recheck the alignment between the driver (motor, turbine, or engine) and pump shafts. Installation of piping may have
forced the pump out of alignment. If so, correct the piping to remove the distorting load.
Check to be certain that the shaft coupling spacer is not installed, and then gently bump the motor starter to check
the rotational direction of the motor. If this is not in the direction of rotation required for the pump, make the neces-
sary corrections.
Lock-out the power to the driver (motor, turbine, engine, etc.)
Install the shaft coupling spacer. Be sure that you install all the retaining devices and bolts and that they are tight.
Read and comply with the coupling manufacturer’s instructions. Personal injury, death, and/or equipment damage
could occur if the coupling spacer is not properly installed. Remove all debris and tools from the area near the shafts
and the shaft coupling. Do this to assure that nothing is caught and thrown by the rotating parts when the pump is
started. Bolt the coupling guard securely to the baseplate, checking to assure that it is not contacting any parts that
will rotate when the pump is started.
FILLING - Before filling the pump with liquid, check to see that all possible leak locations are sealed. See that all of
the connections into the pressure containing cavity are sealed or connected to a related piping system that also has
all possible leak paths sealed. Do not plug unused jacket cavities, as this could develop dangerous pressure build-
up. Use a wrench on all bolted joints to apply torque to assure that all gaskets are sealed in a tight joint. Check to
see that all threaded pipe connections are also tight enough to seal the liquid pressure that will be applied when
the system is started.
OPERATING - Before starting the unit, see that all personnel are a safe distance away from all possible hazards,
that all sub-systems are connected and operating, that all debris has been removed, that the shaft coupling guard
is securely in place, and that the pump is full of liquid.
Do not operate this pump at shut-off (no flow) as an explosion may result. This can occur with any liquid, even “cold
water”. Personal injury, death, equipment damage, and/or loss of product (pumpage) is likely to occur. If your sys-
tem is operated where it is possible for all outlets for the discharge from the pump to be closed while the pump is
still operating, a modification of the system needs to be made to assure a continual flow of pumpage through the
pump. Note that some people have a belief that a bypass line from the discharge side of the pump to the suction
side of the pump will relieve this problem, this is “NOT TRUE”; DO NOT ATTEMPT THIS.
MAINTENANCE, DISASSEMBLY AND REPAIR - Work must be performed only by thoroughly trained and qualified
personnel to assure quality repair and to reduce the possibilities of injury to personnel and/or damage to equip-
ment. If you do not have personnel who are capable of safe quality repair of this equipment, we advise you to return
the equipment to DEAN PUMP to be repaired.
When it is necessary to open the pump and/or the pumping system, the fluid will be exposed to the atmosphere
and personnel in the area. For the safety of all involved, the risk of exposure of personnel to the hazards of the
pumpage can be reduced by flushing the entire system with a compatible non-toxic, non-hazardous,stable liquid
before opening the pump or the system. In all cases, where the system is flushed or not, use the utmost care around
the pumpage and the pumping system.
Always wear the appropriate protective apparel when working on or around the pumping equipment. Safety glass-
es with side shields, heavy work gloves (use insulated work gloves when handling hot items), steel-toed shoes, hard
hat, and any other protective gear as needed for protection. One example of other gear would be breathing
apparatus when working near toxic materials.
Use only top quality tools.
Stop the pump. Turn off the power supply (electricity, steam, etc.) to the pump driver (motor, turbine, engine, etc.)
and lock the switching device so that it cannot be restarted. Tag the switching device so that no one will attempt to
restart the unit.
Close the suction and discharge valves completely to isolate the pump from the system. Lock the valves in the closed
position and tag them so that no one will attempt to open them.
Turn off, lock out, and tag all sub-systems and auxiliary equipment and auxiliary supply lines to isolate the pump-
ing unit from any and all power, energy, and/or fluids.
Do not attempt to perform any work on the unit until you are confident that the pump and its contents have been
stabilized at ambient temperature, and atmospheric pressure.
Put on protective wear to protect human tissue from attack by the fluids contained in the pump and any sub-systems,
and from any vapors or fumes that could possibly be released from these fluids. This could mean breathing apparatus,
face shields, heavy long sleeve rubber gloves, rubber apron, hood, and possibly more, dependent of course on the
properties of the fluids involved and the installed drain and vent piping arrangement. Personal injury and/or death
can occur if adequate precautions are not taken with regard to the fluid, the installation, and the possibilities of the
release of fluid, vapors, and/or fumes.
Remove the coupling guard. Remove the coupling spacer.
Drain all the fluids from the auxiliary sub-systems (lubrication, cooling, heating, seal barrier, etc.) that are connect-
ed to the pump. Drain each fluid into a separate container. Use caution required for each fluid after reading the
MSDS (Material Safety Data Sheet) for each.
Carefully bleed off any pressure remaining in the pump. Pressure remaining in the pump will be dependent upon
the pressure in the system when the pump was stopped; the quality, type, and condition of the isolation valves; the
thermal expansion values of the fluid and the pump material; and the change in the vapor pressure of the fluid
between the temperature at the time the isolation valves were closed and the ambient temperature. Bleeding must
be through a valved drain line piped to a closed container mounted lower than the pump. The container must be
arranged with a relief passage to some point where pressure and fumes will not be harmful to personnel. The con-
tainer must also have a level device so that determination can be made that sufficient fluid has been drained to
empty the pump cavity and the volume of fluid that was contained in the run of suction and discharge pipe between
the isolation valves and the pump. After the initial rush of fluid from the pump relieves the pressure, the drain valve
can be opened further to speed the draining operation. When fluid quits running into the drain tank, gauge the
volume to see if it is sufficient to have fully drained the contents of the pump and the suction and discharge pipes
between the isolation valves.
If the system was constructed without any drain connections, it will be necessary to consult the designers of the system
for safe draining procedures.
Now drain any small piping, that contains the fluid pumped, from all low points, into the same container used to drain
the pump. Do not drain any other fluids (different than the pumpage) into this container as they may not be
compatible. Personal injury, death, and/or equipment damage could occur.
Even though it might appear that, the cavity being drained has completely drained, be extremely careful about
opening the system and/or opening the pump. If something solid in the pumpage moves to the vicinity of the drain
connection, it could seal-off the drain and maintain pressure in the cavity thought to have been drained. It is also
possible that the isolation valves are not sealing and therefore allowing liquid to flow from the system into the pump.
Personal injury, death, and/or equipment damage may occur if intense caution is not exercised.
Because of the above possibility, when you loosen the gasketed joint at the back of the casing (5), loosen the nuts only
one full turn, and then use jack screws to break the gasket seal. If fluid and/or pressure remains in the pump, it will
spray out now. Use extreme caution, wearing protective gear, to avoid injury. Do not proceed with disassembly until
leakage ceases completely. If leakage does not cease, the isolation valves may not be sealing. Note that if the pump
was purchased with out a drain, the pump will contain fluid which will flow out at the time the bolts are loosened
and the gasket seal is broken.
When you open the pump, the fluid will be exposed to the atmosphere and personnel in the area. For the safety of
all involved, the risk of exposure can be reduced by flushing the cavity that was just drained, with a compatible non-
toxic, non-hazardous, stable liquid, before disassembling the pump.
Remove the casing nuts and using mechanical lifting apparatus to support the weight, pull the rotating unit from
the casing.
Flush the wetted parts now exposed with compatible, non-toxic, non-hazardous, stable liquid.
Remove the gasket from the face of the casing (5) or the bearing housing (26) dependent on which one the gasket may
have adhered to. The type of gasket and material of construction will vary with service requirements. Attack by prying
and then, if necessary, layering off the old gasket with a sharp scraper, attempting to remove it in the largest possible
pieces. Wear heavy leather, long sleeve work gloves when using the scraper. Wet the gasket before and during the
scraping operation to reduce the possibility of fibers becoming airborne. Wear a respirator during this operation and
until all debris has been disposed of in a plastic bag. Remove all of the gasket material down to clean metal surfaces
on both parts that contacted the gasket. Place all of the gasket residue in a plastic bag, seal the bag and dispose of it
in compliance with all government requirements.
The rotating assembly of the pump can now be moved to a more convenient location for further disassembly. Use
only high quality tools. Flush parts as disassembled to removed hazardous residue from the pumpage and/or
sub-system fluids.
Wear protective equipment as advised at the beginning of these warnings.
Use mechanical lifting equipment to lift assemblies and components.
Do not apply heat to parts to assist in disassembly. Explosion could occur causing personal injury, death, and/or
damage to equipment.
Do not attempt to drill, saw, or otherwise cut parts to remove them. Explosion and/or fuming could occur causing
personal injury, death, and/or equipment damage.
Do not hammer on any parts. Personal injury and/or damage to equipment may occur.
Do not attempt to manufacture parts or modify Dean Pump parts in any manner. Death, personal injury, and/or
damage to equipment may occur.
One example of the above would be overboring the seal chamber, which removes metal that is required to contain
fluids. Removal of this metal reduces the pressure containing capability of the part, and may create a leak path
through the part.
Replace all gaskets, seals, bearings, and lubricants. Replace all parts that have worn, corroded, eroded, or other-
wise deteriorated.
Use only Dean Pump Division of Met-Pro Corporation parts.
HAZARDOUS SITUATIONS MAY OCCUR UNLESS THIS EQUIPMENT IS APPLIED, INSTALLED, OPERATED, AND MAINTAINED BY THOROUGHLY QUALIFIED PERSONNEL
IN STRICT ACCORDANCE WITH THE INSTRUCTION MANUAL AND ALL APPLICABLE DRAWINGS AND CODES.
READ WARNINGS