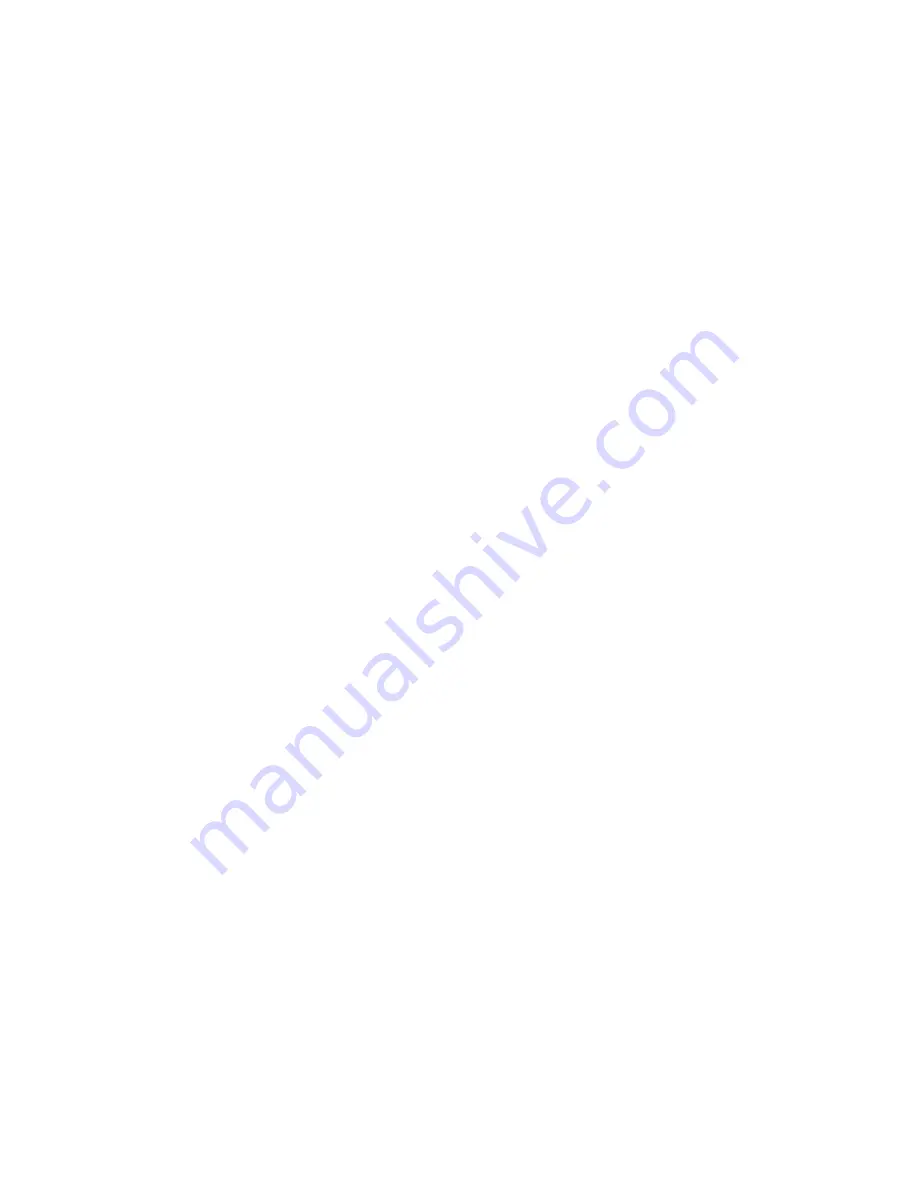
j) Remove the vapor eliminator assembly (see “Small Piping
Connections” on page 7). First, loosen the tubing nut at the top
of the vapor eliminator and remove the vapor exhaust tube.
Next, remove the vapor eliminator by breaking the pipe joint
at the top connection of the pipe tee. There is no need to break
any of the other piping connections.
k) Remove the casing capscrews (5D) of the RWA2096 or the
casing nuts (5C) of the RWA4166 or the RWA4206, and
using a mechanical lifting apparatus to support the weight, pull
the rotating unit form the casing (5). Unscrew the two
jackscrews until they are not protruding through the “casing
side” of the bearing housing (26) flange.
l) Flush the wetted parts – now exposed – with a compatible,
non-toxic, non-hazardous, stable liquid.
m) Remove the gasket from the face of the casing (5) or the
bearing housing (26) dependent on which one the gasket may
have adhered to. The type of gasket and material of construc-
tion will vary with service requirements. Attack by prying and
then, if necessary, layering off the old gasket with a sharp
scraper, attempting to remove it in the largest possible pieces.
Wear heavy Leather, long sleeve work gloves when using the
scraper. Wet the gasket before and during the scraping
operation to reduce the possibility of fibers becoming
airborne. Wear a respirator during this operation and until all
debris has been disposed of in a plastic bag. Remove all of
the gasket material down to clean metal surfaces on both parts
that contacted the gasket. Use care to not damage the metal
faces. Place all of the gasket residue in a plastic bag, seal the
bag and dispose.
n) Inspect the inside of the casing (5) for any signs of wear,
corrosion or any other damage. If the casing needs to be
removed, remove the bolts from the suction and discharge
flanges. Remove the bolts that hold the casing feet to the base-
plate. The casing can now be removed. Remove the suction
and discharge flange gaskets using the procedure as in
paragraph “m” above.
o) The rotating assembly of the pump can now be moved to a
more convenient location for further disassembly. Use mechan-
ical lifting equipment to move assemblies and components.
DISASSEMBLY PROCEDURE
To further dismantle the pump, perform the following steps in the
sequence shown:
WARNING:
Use only high quality tools.
Obtain MSDS data sheets for all liquids (from the manufacturers of
those liquids) being used with the pump, and heed all cautions.
Flush parts as disassembled to remove hazardous residue from
the pumpage and/or sub-system fluids.
Wear protective equipment as advised at the beginning of this
section.
Use mechanical lifting equipment to lift assemblies and components.
Do not apply heat to parts to assist in disassembly. Explosion
could occur causing personal injury, death, and/or damage to
equipment.
Do not attempt to drill, saw or otherwise cut parts to remove
them. Explosion and/or fuming could occur causing personal
injury, death, and/or equipment damage.
Do not hammer on any parts. Personal injury and/or damage to
equipment may occur.
a) Remove the impeller nuts (12) of the RWA2096 or the impeller
bolt (12) of the RWA4166 or the RWA4206 (all have right
hand threads) while holding the pump shaft (29) against
rotation with a wrench on the flats of the coupling hub. When
loosening the impeller nuts (12) of the RWA2096, be sure to
loosen the outer nut and remove it, before loosening the nut that
is closest to the impeller (3). Remove the impeller retaining
washer (12A). Slide the impeller (3) off of the shaft (29).
Remove the impeller key (4) from the shaft (29).
b) Remove the coupling hub from the pump shaft (29) by
loosening the set screws and using a gear puller to pull the hub
from the shaft. Do not hammer on the coupling hub or the shaft.
Remove the coupling key. Be careful to not bend the blades
of the fan (120).
c) Remove the fan (120) from the pump shaft (29). If the pump is
a RWA2096, slide the fan (120) and the fan clamp ring (122)
off the end of the pump shaft (29). If the pump is a RWA4166
or a RWA4206, loosen the radially positioned securing screw
in the side of the fan collar (121) and slide the fan (120), fan
collar (121), fan clamp ring (122) assembly off the end of the
pump shaft (29). If this assembly resists removal, loosen the two
axially positioned screws that hold these parts together.
WARNING:
Wear gloves when removing the fan (120) to protect your
hands as the fan is made of thin metal and could cut you.
d) Remove the bearing end cover (28) from the bearing housing.
Remove the bearing end cover gasket (77B), if the pump is a
RWA4166 or RWA4206.
e) Press the grease seal (76A) from the bearing end cover (28), if
the pump is a RWA4166 or a RWA4206.
f) Pull the pump shaft (29) from the bearing housing (26), using
care to keep the shaft in line with the bearing housing so as
not to damage any parts. Wear heavy work gloves.
Compression of the mechanical seal springs will be detected
during this operation.
g) Remove the mechanical seal rotary (95B) from the pump
shaft (29).
1) If the pump is a RWA2096, loosen the set screws that hold
the mechanical seal rotary (95B) to the shaft, at least two
full turns each. Use gloves to protect your hands and slide
the mechanical seal rotary (95B) from the shaft (29). It may
take a considerable amount of force to remove the rotary
(95B) as the “O” ring, between the rotary and the shaft
(29) may be tight.
2) If the pump is a RWA4166 or a RWA4206, loosen the set
screws (370), in the shaft sleeve (10), at least two full
revolutions each. Use gloves to protect your hands and slide
the shaft sleeve (10) and the mechanical seal rotary (95B),
as an assembly, from the pump shaft (29). It may take a
considerable amount of force to remove these parts as the
sleeve gasket (77A) is a “O” ring and may be tight on the
shaft (29). Loosen the set screws, that hold the mechanical
seal rotary (95B) to the sleeve (10), at least two full
revolutions each. Slide the seal rotary (95B) from the sleeve
(10). It may take a considerable amount of force to remove
the rotary (95B) as the “O” ring between the rotary and the
sleeve (10) may be tight.
h) Remove the mechanical seal gland (13) from the shaft. Remove
the seal gland gaskets (325) from the seal gland (13). Remove
the mechanical seal stationary (95A) from the mechanical seal
gland (13).
13