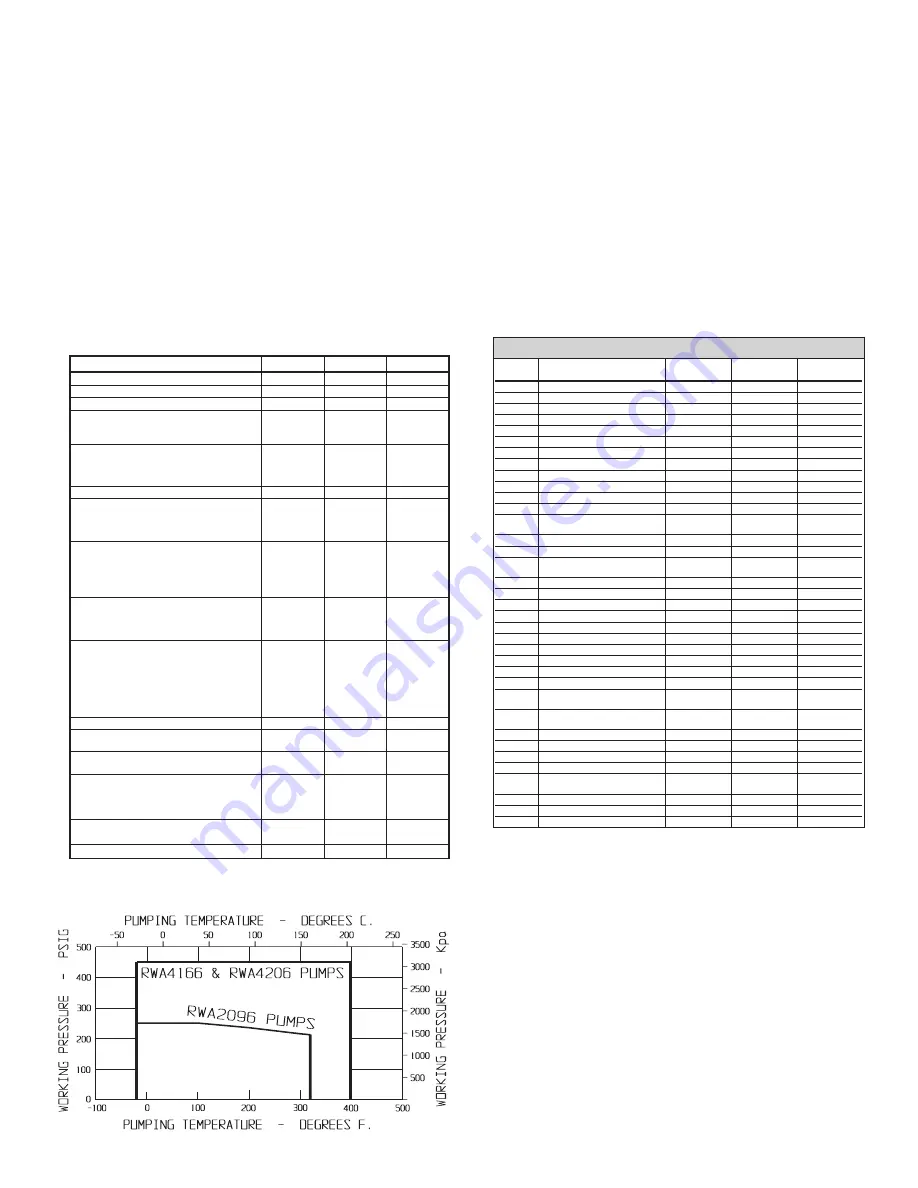
ALLOWABLE WORKING PRESSURE VS. PUMPING TEMPERATURE
WARNING:
Be sure that there is nothing remaining in the pump that could
react with the liquid that will be pumped or that would have an
excessive vapor pressure at the system operating temperature.
4) Replace the vapor eliminator. Place pipe sealant onto
the threads of the pipe nipple, and tighten the vapor
eliminator onto the top of the piping rising from the vent
tee. Install the vapor exhaust tube into the connector on
top of the vapor eliminator.
5) Replace the casing drain plug.
6) Remove the “storage” protective coating from the external
surfaces of the pump.
Pumps must also be protected from moisture, dirt, and physical
damage, during and after installation while the system is
being completed. Pumps “stored” on their foundations must be
completely checked for proper installation prior to start-up.
Care in storage and installation will preserve the built-in
quality of each Dean Product.
RWA SERIES
FAN COOLED, HORIZONTAL, SINGLE STAGE, END SUCTION, ENCLOSED IMPELLER, CENTRIFUGAL, HOT WATER PUMPS. THESE PUMPS
ARE DESIGNED SPECIFICALLY FOR USE WITH HOT WATER, ETHYLENE GLYCOL, PROPYLENE GLYCOL AND TRIETHYLENE GLYCOL.
THESE PUMPS WILL NOT WORK ON OTHER LIQUIDS.
3
MECHANICAL DESIGN SPECIFICATIONS
PUMP TYPE
Seal chamber pressure equals pump suction pressure plus .06 x developed head.
Casing Thickness, Minimum
Corrosion Allowance
Impeller Balance –
Standard
Optional Extra
Flanges
ANSI Class
Facing
Finish
Suction Pressure, Maximum
Horsepower Rating, Maximum
@3500 RPM
@1750 RPM
@1150 RPM
Bearings:
Thrust Bearing, Ball Type, Grease Lubricated
Rarial Bearing, Sleeve Type, Pumpage Lubricated
Seal Chamber Dimensions
Length (Depth)
Inside Diameter (Bore Dia.)
Shaft Diameter
Pump Shaft Dimensions
Span Between Bearings
Span Between Radial Bearing Centerline
and Impeller Centerline
Diameter at Coupling
Diameter Between Bearings
Diameter at Impeller
L
3
/D
4
Material Class
Maximum Working Pressure
Direction of Rotation (Viewed from Coupling End)
RWA 2096
RWA 4166
RWA 4206
CW
CCW
CCW
5
/
16
"
1
/
8
"
Single Plane
Dynamic
150
Flat Face
125 Ra
100 PSIG
Pumping Temperature
Minimum
35
15
10
5306 2RS
Double Row
Maximum Ambient Temperature
(temp. within 12” of the pump)
Hydrostatic Test Pressure
1
5
/
8
"
2
1
/
16
"
1
1
/
8
"
8
11
/
16
"
1
5
/
8
"
7
/
8
"
15
/
16
"
3
/
4
"
4.3
22
(Ductile Iron)
250 PSIG
@100°F
-20°F @
250 PSIG
320°F @
210 PSIG
Maximum
118°F
430 PSIG
700 PSIG
700 PSIG
118°F
118°F
5
/
16
"
5
/
16
"
1
/
8
"
1
/
8
"
Single Plane
Dynamic
Single Plane
Dynamic
300
Raised Face
125 Ra
300
Raised Face
125 Ra
260 PSIG
260 PSIG
100
40
25
250
125
75
7308 BG
Angular
Contact Pair
7311 BG
Angular
Contact Pair
2
13
/
16
"
3
1
/
8
"
2"
3
7
/
8
"
4
5
/
16
"
2
1
/
2
"
11
7
/
16
"
2
5
/
16
"
1
1
/
8
"
1
9
/
16
"
1
1
/
8
"
14
5
/
8
"
3
1
/
4
"
1
5
/
8
"
1
7
/
8
"
1
1
/
2
"
2.1
2.8
-20°F
400°F
-20°F
400°F
450 PSIG
450 PSIG
22
(Ductile Iron)
22
(Ductile Iron)
Part No.
Part Name
RWA 2096
RWA 4166
RWA 4206
Class 22
Class 22
Class 22
3
Impeller
C.I. (1)
C.I. (1)
C.I. (1)
4
Impeller Key
Steel (2)
Steel (2)
Steel (2)
5
Casing
D.I. (10)
D.I. (10)
D.I. (10)
5A
Casing Drain Plug
Steel (2)
Steel (2)
Steel (2)
5C
Casing Stud Nut
N.A.
Steel (5)
Steel (5)
5D
Casing Stud/Cap Screw
Steel (3) Screw Steel (4) Stud
Steel (4) Stud
6A
Casing Ring (only some sizes)
N.A.
Iron (7)
Iron (7)
9
Bearing Housing Foot
Steel (2)
Steel (2)
Steel (2)
*10
Shaft Sleeve
N.A.
316 S/S
316 S/S
*12
Impeller Bolt/Nut
Steel (2) Nut
Steel (2) Bolt
Steel (2) Bolt
*12A
Impeller Washer
Steel (2)
Steel (2)
Steel (2)
*13
Mechanical Seal Gland
Steel (2)
Steel (2)
Steel (2)
*25A
Shaft Bearing – Thrust – Ball
Double Row
Angular
Angular
Contact Pair
Contact Pair
26
Bearing Housing
D.I. (10)
D.I. (10)
D.I. (10)
*28
Bearing End Cover
C.I. (1)
Steel (2)
D.I. (9)
*29
Pump Shaft
11-13 S/S
11-13 S/S
11-13/316 S/S
(12)
(12)
S/S (8)
*31
Thrust Bearing Lock Nut
N.A.
Steel (2)
Steel (2)
*31A
Thrust Bearing Lock Washer
N.A.
Steel (2)
Steel (2)
56
Casing Foot
N.A.
C.I. (1)
C.I. (1)
*75
Snap Ring
N.A.
Steel (2)
N.A.
*75A
Snap Ring
Steel (2)
N.A.
N.A.
*76
Grease Seal – Front
Viton (13)
Viton (13)
Viton (13)
*76A
Grease Seal – Rear
N.A.
Buna (14)
Buna (14)
77
Casing Gasket
Teflon (11)
Teflon (11)
Teflon (11)
*77A
Sleeve Gasket
N.A.
Aflas)
Aflas
*77B
Bearing End Cover Gasket
N.A.
Buna (14)
Buna (14)
*95A
Mechanical Seal Stationary
Silicon Carbide Silicon Carbide Silicon Carbide
& Aflas
& Aflas
& Aflas
*95B
Mechanical Seal Rotary
S/S, Carbon,
S/S, Carbon,
S/S, Carbon,
& Aflas
& Aflas
& Aflas
98
Coupling Guard
Steel (2)
Steel (2)
Steel (2)
*120
Fan
Aluminum
Aluminum
Aluminum
*121
Fan Collar
N.A.
Steel (2)
Steel (2)
*122
Fan Clamp Ring
Steel (2)
Steel (2)
Steel (2)
*180
Radial Bearing Cartridge
Carbon &
Carbon &
Carbon &
Steel
& Steel
416 S/S
*325
Seal Gland Gasket
Aflas (13)
Aflas (13)
Aflas (13)
*370
Sleeve Set Screw
N.A.
18-8 S/S
18-8 S/S
*375
Anti-Rotation Pin
N.A.
N.A.
316 S/S
MATERIAL SPECIFICATIONS (REFER TO NUMBERS IN PARENTHESES)
* Denotes parts interchangeability in all pump sizes of a given series.
S
TANDARD
M
ATERIALS OF
C
ONSTRUCTION
(1) Cast Iron
(9) Ductile Iron – ASTM A536
(2) AISI 1020
(10) Ductile Iron – ASTM A395
(3) SAE Grade 5 or ASTM A449 Type 1 Steel (11) Teflon® Elastomer
(4) AISI 4140, ASTM A193-B7 Steel
(12) ANSI 420 S/S
(5) ASTM A194 Grade 2 Steel
(13) Viton® Elastomer
(7) Hardened Iron
(14) Buna N Rubber
(8) ANSI 316 S/S with ANSI 416 S/S
at the sleeve bearing
Viton® is a registered Trademark of E. I. DuPont Co.
Teflon® is a registered Trademark of E. I. DuPont Co.