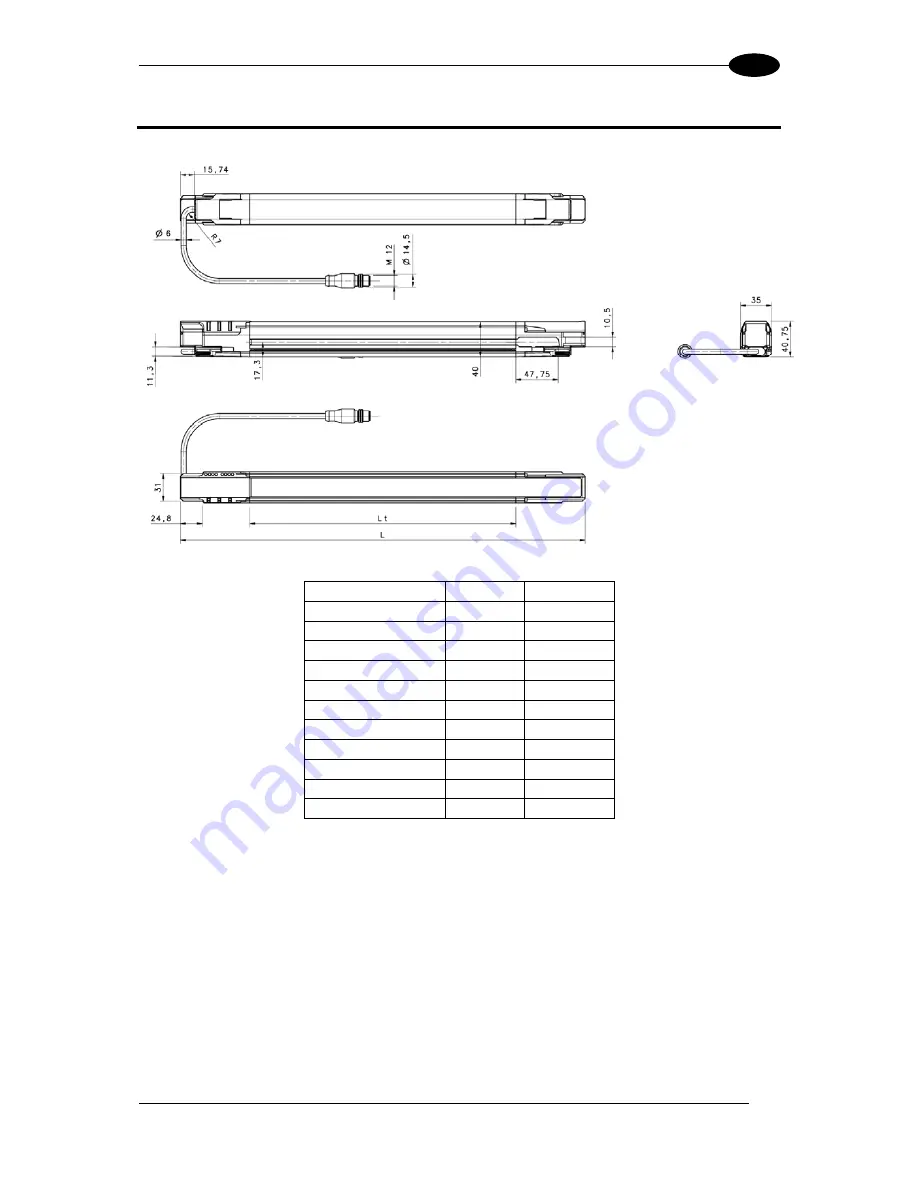
OVERALL DIMENSIONS
77
13
13 OVERALL DIMENSIONS
MODEL L
t
(mm)
L (mm)
SG4-xx-030-OO-P
150
306,3
SG4-xx-045-OO-P
300 456,3
SG4-xx-060-OO-P
450 606,3
SG4-xx-075-OO-P
600 756,3
SG4-xx-090-OO-P
750 906,3
SG4-xx-105-OO-P
900 1056,3
SG4-xx-120-OO-P
1050 1206,3
SG4-xx-135-OO-P
1200 1356,3
SG4-xx-150-OO-P
1350 1506,3
SG4-xx-165-OO-P
1500 1656,3
SG4-xx-180-OO-P
1650 1806,3
xx = Resolution (14mm - 30mm)
Summary of Contents for SG4-14-030-OO-P
Page 1: ...SG4 EXTENDED Instruction Manual ...
Page 3: ......
Page 93: ...ACCESSORIES 85 15 Fixing kit MODEL DESCRIPTION CODE ST DM Kit STAND ALONE 95ASE1940 ...
Page 105: ...ACCESSORIES 97 15 SG4 EXTENDED BRACCI ATTIVO PASSIVO L SG4 EXTENDED BRACCI ATTIVO PASSIVO T ...
Page 108: ...www datalogic com ...