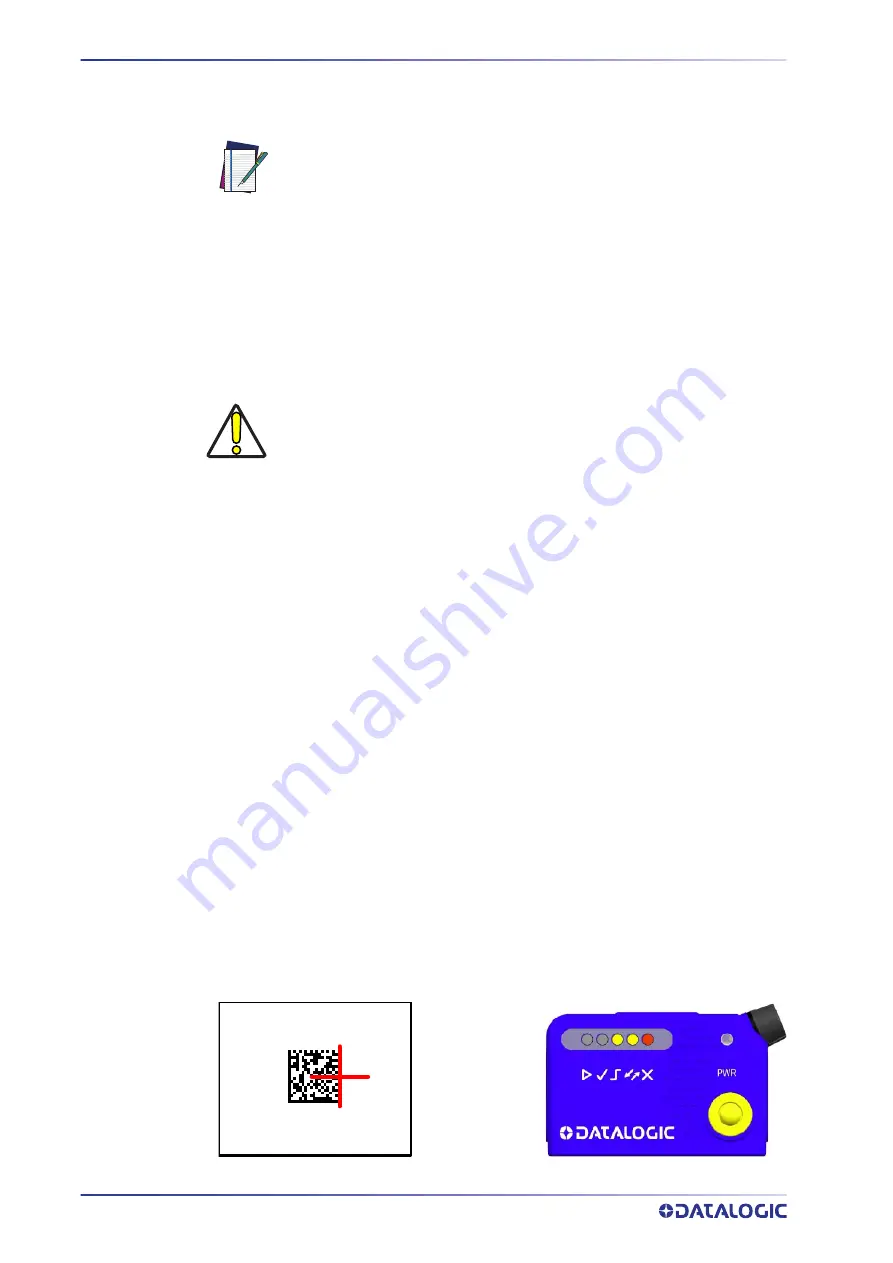
RAPID CONFIGURATION
6 MATRIX 120™
3. Refer to the reading diagrams in
to determine the distance your reader
should be positioned at.
NOTE
STEP 3 - X-PRESS CONFIGURATION
The Matrix 120 models are factory calibrated at three focus positions (
45,
70 and 125
mm for WVGA models; 45,
80 and 125 mm for MP models
). Using a 2.5 mm Hex key
(Allen wrench), rotate the Focus Adjustment Screw at the back of the reader to one of
these three positions for your application.
Refer to the Reading Diagrams in
, which show the reading
ranges at the different focus positions for Code 128 (1D) and Data Matrix (2D) codes.
Focus/Aiming
Matrix 120™ devices provide a built-in aiming system to aid reader positioning. The aim-
ing system is accessed through the X-PRESS Interface.
1. Power the reader on. During the reader startup (reset or restart phase), all the
LEDs blink for one second. On the connector side of the reader near the cable, the
“POWER ON” LED (blue) indicates the reader is correctly powered.
2. Enter the Focus/Aim function by pressing and holding the X-PRESS push button
until the Aim LED is on.
3. Release the button to enter the Aim function. The aiming system turns on see .
4. Place an
application specific code
in front of the reader at the reading distance
indicated for your model as described above, centering it a few mm to the left of
the aiming system indicator as shown below.
FOV
Rapid Configuration of the Matrix 120™ reader can be made either
through the X-PRESS™ interface (steps 3) which requires no PC con-
nection, or by using the DL.CODE Configuration Program (steps 5-6).
Select the procedure according to your needs.
CAUTION
Do not rotate the Focus Adjustment Screw beyond the focus scale limits
otherwise damage can occur to the focus mechanism.
Figure 6 - Aiming function using
the red crosshairs
Figure 7 - X-PRESS interface:
Aim Function
Summary of Contents for Matrix 120
Page 1: ...Matrix 120 PRODUCT REFERENCE GUIDE Image Based Reader...
Page 14: ...GENERAL VIEW XIV MATRIX 120...
Page 75: ...INPUTS PRODUCT REFERENCE GUIDE 61 Figure 41 NPN External Trigger Using Matrix 120 Power...
Page 97: ...GLOBAL FOV DIAGRAMS PRODUCT REFERENCE GUIDE 83 Matrix 120 310 xxA Models Digimarc Barcode...
Page 153: ...Reader 2 Reader 3 PASS THROUGH CONFIGURATIONS PRODUCT REFERENCE GUIDE 139...
Page 185: ......
Page 186: ......
Page 187: ......