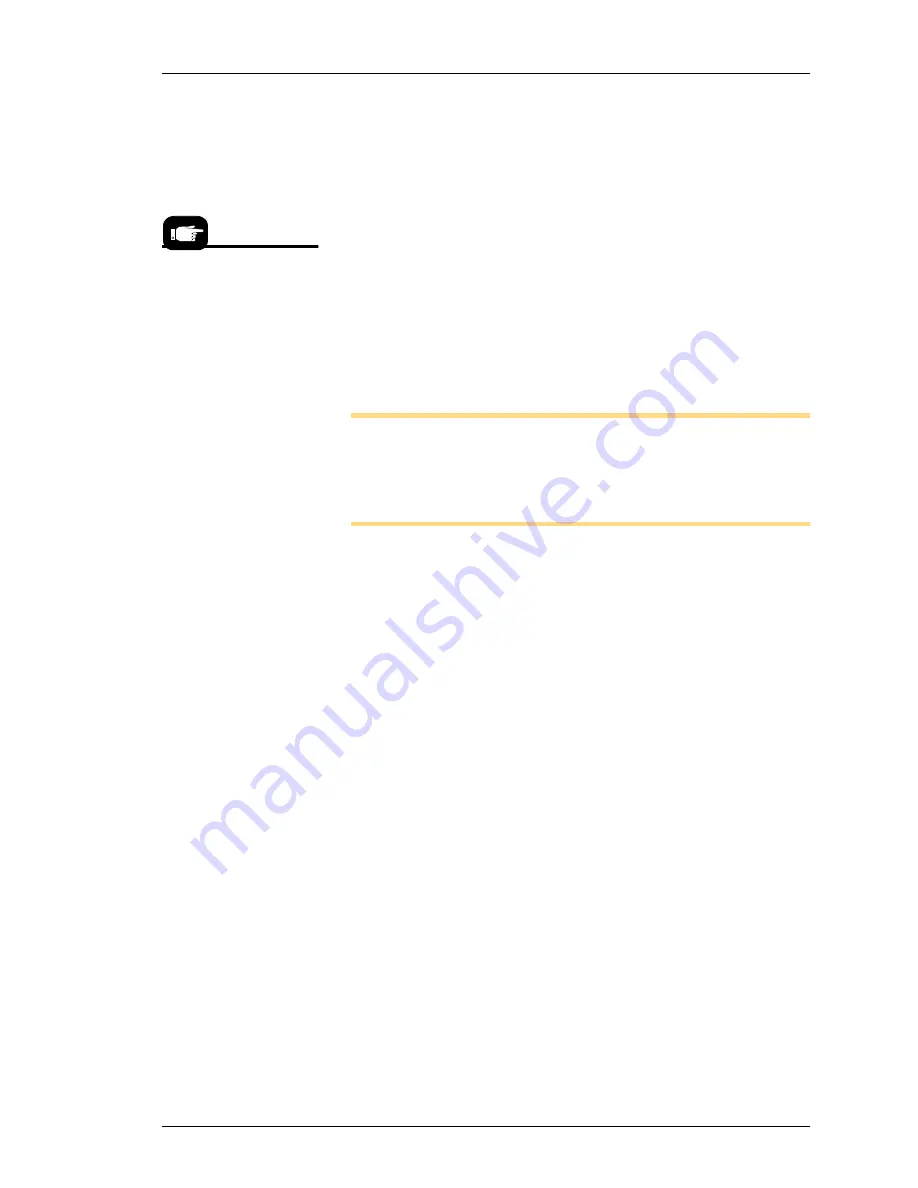
■ Running a Job on PSV7000 ◘ List of Steps to Start a Job
PSV7000 Operator’s Manual
—55—
back
5a. (Optional) In the
Continuity Retries
field, enter the number
of times the system should retry continuity failures before
rejecting the device.
5b. (Optional) In the
Fail Retries
field, enter the number of
times the system should retry programming failures
(excluding over-current and continuity) before rejecting the
device.
6.
[Automotive Performance Pak Option only]
(Optional) Start
any of the five utilities available with the AP Pak. NOTE that
you may not have security rights to change these options. Check
with your administrator.
7.
Make sure
Ignore Programmers
is Off (red).
If it is
On
(green), the PNP head will not stop at the program-
mers and will effectively transfer devices from input media to
output media with no programming, and with or without laser
marking. The default is Off.
Note:
If your desired input media (tube, tape, or tray) does not dis-
play on the
Options
tab, the winAH400.ini file may need to be
edited. See the online Help for instructions editing the
WinAH400.int file or contact Data I/O Customer Support or a
local Data I/O approved service representative.
Verifying Media Setup
1.
At the
Setup
window, click the
Job Info
tab.
2.
Verify that all the information displayed for this job is accurate.
Refer to the figure below of the
Job Info
tab.
For more information on
the AP Pak, see the AH700
on-screen Help.