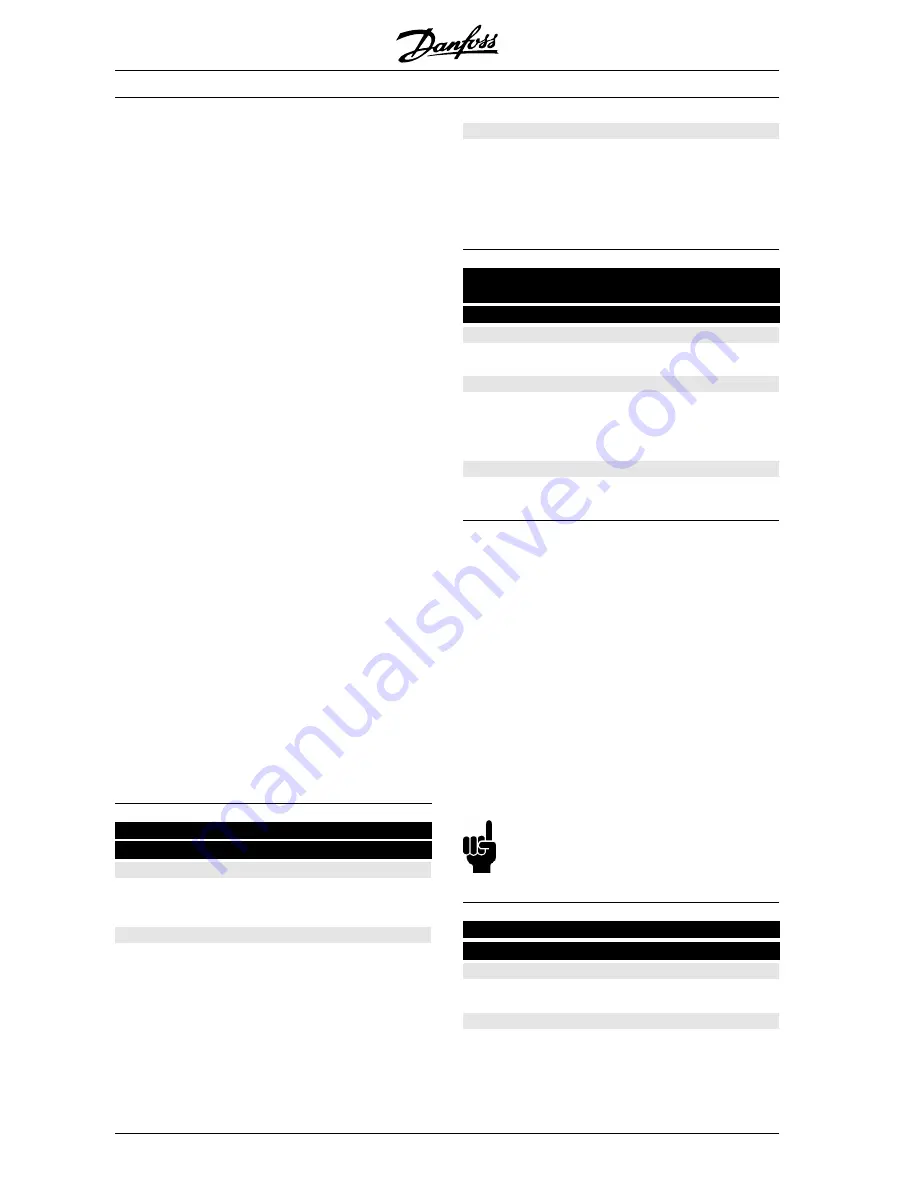
VLT
®
FCD Series
Choose
Coasting during start delay time
[2] and the
motor will not be controlled by the frequency con-
verter during the start delay time (inverter turned off).
Choose
Start frequency/voltage clockwise
[3] to ob-
tained the function described in parameter 130
Start
frequency
and 131
Voltage at start
during start delay
time. Regardless of the value assumed by the refer-
ence signal, the output frequency equals the setting
in parameter 130
Start frequency
and the output
voltage will correspond to the setting in parameter
131
Voltage at start
.
This functionality is typically used in hoist applica-
tions. It is used in particular in applications in which
a cone anchor motor is applied, where the direction
of rotation is to start clockwise followed by the refer-
ence direction.
Select
Start frequency/voltage in reference direction
[4] to obtain the function described in parameter 130
Start frequency
and 131
Voltage at start
during the
start delay time.
The direction of rotation of the motor will always fol-
low in the reference direction. If the reference signal
equals zero, the output frequency will equal 0 Hz,
while the output voltage will correspond to the set-
ting in parameter 131
Voltage at start
. If the
reference signal is different from zero, the output fre-
quency will equal parameter 130
Start frequency
and the output voltage will equal parameter 131
Volt-
age at start
. This functionality is used typically for
hoist applications with counterweight. It is used in
particular for applications in which a cone anchor
motor is applied. The cone anchor motor can break
away using parameter 130
Start frequency
and pa-
rameter 131
Voltage at start
.
122
122 Function at stop
(FUNCTION AT STOP)
Value:
✭
Coasting (COAST)
[0]
DC hold (DC HOLD)
[1]
Function:
This is where to choose the function of the fre-
quency converter after the output frequency has
become lower than the value in parameter 123
The
min. frequency for activation of function at stop
or
after a stop command and when the output fre-
quency has been ramped down to 0 Hz.
Description of choice:
Select
Coasting
[0] if the frequency converter is to
’let go’ of the motor (inverter turned off).
Select DC hold [1] if parameter 137
DC hold voltage
is to be activated.
123
123 Min. frequency for activation of function at
stop
(MIN.F.FUNC.STOP)
Value:
0,1 - 10 Hz
✭
0,1 Hz
Function:
In this parameter, the output frequency is set at
which the function selected in parameter 122
Func-
tion at stop
is to be activated.
Description of choice:
Set the required output frequency.
■
DC Braking
During DC braking DC voltage is supplied to the mo-
tor, and this will cause the shaft to be brought to a
standstill. In parameter 132
DC brake voltage
DC
brake voltage can be preset from 0-100%. Max. DC
brake voltage depends on the motor data selected.
In parameter 126
DC braking time
DC braking time
is determined and in parameter 127
DC brake cut-in
frequency
the frequency at which DC braking
becomes active is selected. If a digital input is pro-
grammed to
DC braking inverse
[5] and shifts from
logic ’1’ to logic ’0’, DC braking will be activated.
When a stop command becomes active, DC braking
is activated when the output frequency is less than
the brake cut-in frequency.
NB!:
DC braking may not be used if the inertia in
the motor shaft is more than 20 times greater
than the motor’s internal inertia.
126
126 DC brake time
(DC BRAKING TIME)
Value:
0 - 60 sec.
✭
10 sec
Function:
In this parameter, the DC brake time is set at which
parameter 132
DC brake voltage
is to be active.
✭
= factory setting. () = display text [] = value for use in communication via serial communication port
MG.04.A1.02 - VLT is a registered Danfoss trade mark
60