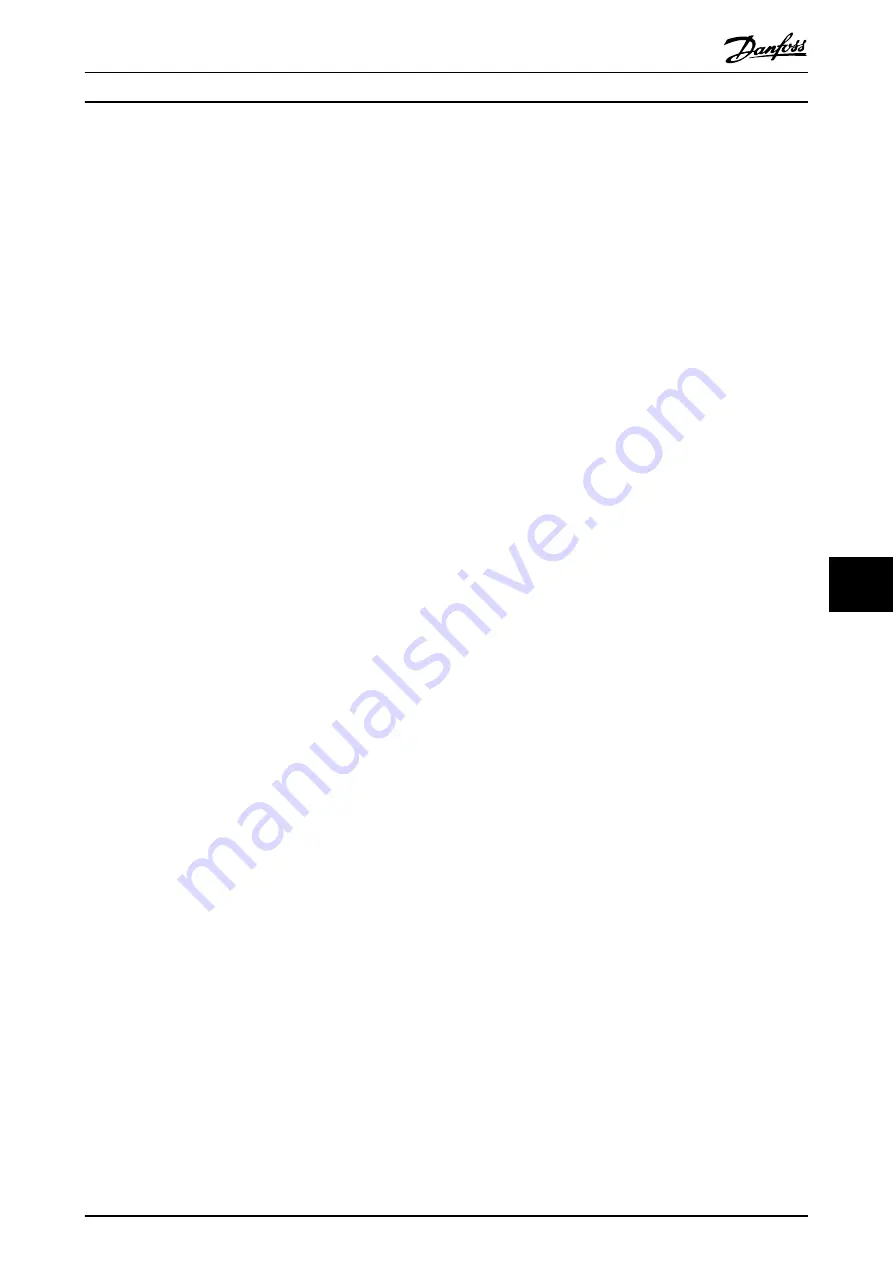
the terminal switch for 53 or 54 is set for voltage.
Check
1-93 Thermistor Source
selects terminal 53
or 54.
•
When using digital inputs 18 or 19, check that
the thermistor is connected correctly between
either terminal 18 or 19 (digital input PNP only)
and terminal 50.
•
If using a thermal switch or thermistor, check that
the programming if matches sensor wiring.
WARNING/ALARM 12, Torque limit
The torque has exceeded the value in
4-16 Torque Limit
Motor Mode
or the value in
4-17 Torque Limit Generator
Mode
.
14-25 Trip Delay at Torque Limit
can change this from
a warning only condition to a warning followed by an
alarm.
Troubleshooting
•
If the motor torque limit is exceeded during ramp
up, extend the ramp up time.
•
If the generator torque limit is exceeded during
ramp down, extend the ramp down time.
•
If torque limit occurs while running, possibly
increase the torque limit. Be sure the system can
operate safely at a higher torque.
•
Check the application for excessive current draw
on the motor.
WARNING/ALARM 13, Over current
The inverter peak current limit (approximately 200% of the
rated current) is exceeded. The warning lasts about 1.5 s,
then the frequency converter trips and issues an alarm.
This fault may be caused by shock loading or fast
acceleration with high inertia loads. If extended mechanical
brake control is selected, trip can be reset externally.
Troubleshooting
•
Remove power and check if the motor shaft can
be turned.
•
Check that the motor size matches the frequency
converter.
•
Check parameters
1-20
to
1-25
for correct motor
data.
ALARM 14, Earth (ground) fault
There is current from the output phases to ground, either
in the cable between the frequency converter and the
motor or in the motor itself.
Troubleshooting:
•
Remove power to the frequency converter and
repair the ground fault.
•
Check for ground faults in the motor by
measuring the resistance to ground of the motor
leads and the motor with a megohmmeter.
•
Perform current sensor test.
ALARM 15, Hardware mismatch
A fitted option is not operational with the present control
board hardware or software.
Record the value of the following parameters and contact
the Danfoss supplier:
•
15-40 FC Type
•
15-41 Power Section
•
15-42 Voltage
•
15-43 Software Version
•
15-45 Actual Typecode String
•
15-49 SW ID Control Card
•
15-50 SW ID Power Card
•
15-60 Option Mounted
•
15-61 Option SW Version
(for each option slot)
ALARM 16, Short circuit
There is short-circuiting in the motor or motor wiring.
•
Remove power to the frequency converter and
repair the short circuit.
WARNING/ALARM 17, Control word timeout
There is no communication to the frequency converter.
The warning is only active when
8-04 Control Timeout
Function
is NOT set to OFF.
If
8-04 Control Timeout Function
is set to
[5] Stop and trip
, a
warning appears and the frequency converter ramps down
until it trips then displays an alarm.
Troubleshooting
•
Check connections on the serial communication
cable.
•
Increase the value in
8-03 Control Timeout Time
.
•
Check the operation of the communication
equipment.
•
Verify a proper installation based on EMC
requirements.
ALARM 18, Start failed
The speed has not exceeded
1-77 Compressor Start Max
Speed [RPM]
during start within the allowed time. (set in
1-79 Pump Start Max Time to Trip
). This may be caused by a
blocked motor.
Warning/Alarm 19, Discharge Temperature High
Warning:
The discharge temperature exceeds the level programmed
in
28-25 Warning Action
.
Alarm:
The discharge temperature exceeds the level programmed
in
28-26 Emergency Level
.
WARNING 23, Internal fan fault
The fan warning function is an extra protective function
that checks if the fan is running/mounted. The fan warning
can be disabled in
14-53 Fan Monitor
(
[0] Disabled
).
Warnings and Alarms
Operating Instructions
MG16J202
Danfoss A/S © Rev. 05/2014 All rights reserved.
87
9
9
Summary of Contents for VLT FC 103
Page 2: ......