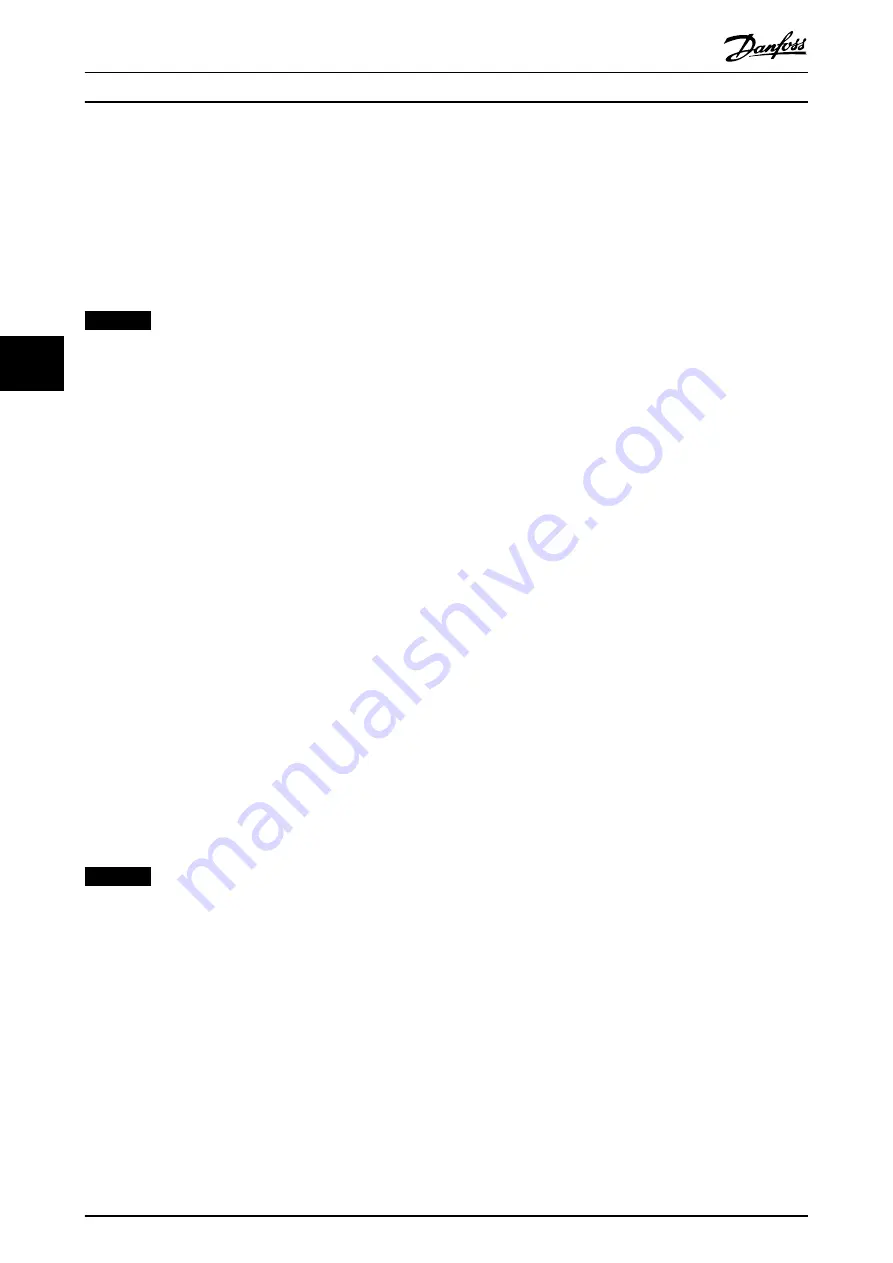
The brake IGBT gate signal originates on the control card and is delivered to the brake IGBT via the power card and
gatedrive card. Also, the power and control cards monitor the brake IGBT for a short circuit. The power card also monitors
the brake resistor for overloads.
5.4 Mechanical Holding Brake Overview
A mechanical holding brake is an external piece of equipment mounted directly on the motor shaft that performs static
braking. Static braking is when a brake is used to clamp down on the motor after the load has been stopped. A holding
brake is either controlled by a PLC or directly by a digital output from the drive.
NOTICE
A drive cannot provide a safe control of a mechanical brake. A redundancy circuitry for the brake control must be
included in the installation.
5.4.1 Mechanical Brake Using Open-loop Control
For hoisting applications, typically it is necessary to control an electromagnetic brake. A relay output (relay 1 or relay 2) or a
programmed digital output (terminal 27 or 29) is required. Normally, this output must be closed for as long as the drive is
unable to hold the motor. In
parameter 5-40 Function Relay
(array parameter),
parameter 5-30 Terminal 27 Digital Output
, or
parameter 5-31 Terminal 29 Digital Output
, select
[32] mechanical brake control
for applications with an electromagnetic brake.
When
[32] mechanical brake control
is selected, the mechanical brake relay remains closed during start until the output
current is above the level selected in
parameter 2-20 Release Brake Current
. During stop, the mechanical brake closes when
the speed is below the level selected in
parameter 2-21 Activate Brake Speed [RPM]
. If the drive is brought into an alarm
condition, such as an overvoltage situation, the mechanical brake immediately cuts in. The mechanical brake also cuts in
during safe torque off.
Consider the following when using the electromagnetic brake:
•
Use any relay output or digital output (terminal 27 or 29). If necessary, use a contactor.
•
Ensure that the output is switched off as long as the drive is unable to rotate the motor. Examples include the load
being too heavy or the motor not being mounted.
•
Before connecting the mechanical brake, select
[32] Mechanical brake control
in
parameter group
5-4* Relays
(or in
parameter group
5-3* Digital Outputs
).
•
The brake is released when the motor current exceeds the preset value in
parameter 2-20 Release Brake Current
.
•
The brake is engaged when the output frequency is less than the frequency set in
parameter 2-21 Activate Brake
Speed [RPM]
or
parameter 2-22 Activate Brake Speed [Hz]
and only if the drive carries out a stop command.
NOTICE
For vertical lifting or hoisting applications, ensure that the load can be stopped if there is an emergency or a
malfunction. If the drive is in alarm mode or in an overvoltage situation, the mechanical brake cuts in.
For hoisting applications, make sure that the torque limits in
parameter 4-16 Torque Limit Motor Mode
and
parameter 4-17 Torque Limit Generator Mode
are set lower than the current limit in
parameter 4-18 Current Limit
. It is also
recommended to set
parameter 14-25 Trip Delay at Torque Limit
to 0,
parameter 14-26 Trip Delay at Inverter Fault
to 0, and
parameter 14-10 Mains Failure
to
[3] Coasting
.
Product Features
VLT® AutomationDrive FC 302
24
Danfoss A/S © 01/2018 All rights reserved.
MG38C202
5
5