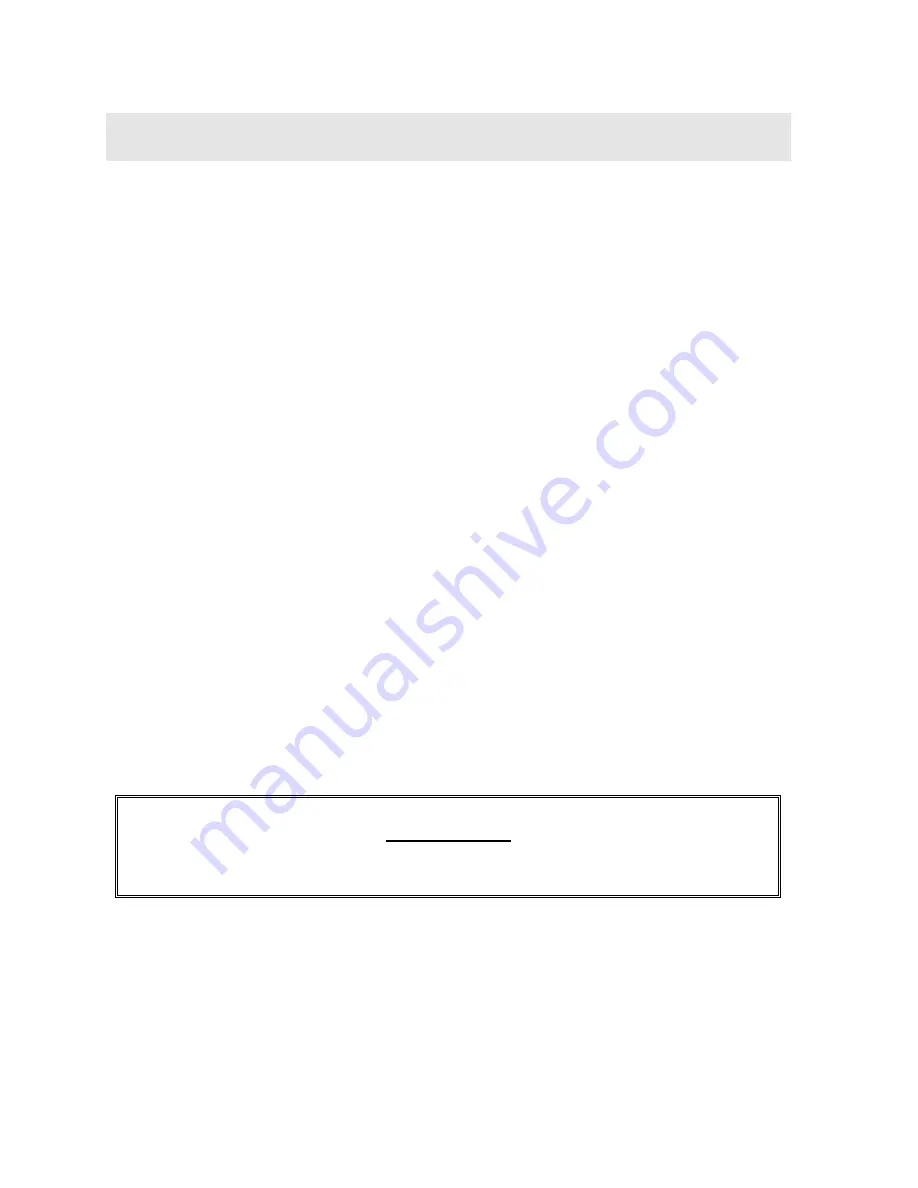
36
CHAPTER FIVE
CALIBRATION
In this section we’ll focus on calibrating the
DFX-7
. There are a number of ways to
go about performing a calibration, but we’ll be focusing on the simplest and most
accurate method, which is performing a two point calibration. This method is very
convenient, as it will automatically calculate the material velocity and zero using a
minimum and maximum calibration standard of know thickness and material type.
The
DFX-7
can certainly be manually calibrated by adjusting the velocity and zero
features, but this is a tedious and redundant process overall.
The two point calibration method can be used for both straight and angle beam
transducers. A number of certified calibration standards are available to address
inspection code requirements, specifications, and applications. It should be noted
again that the
DFX-7
has virtually 2 gauges built into a single gauge; a flaw detector,
and a thickness gauge. Therefore, while the flaw detector option can be calibrated
for straight beam contact and angle beam style transducers, the thickness gauge
option contains a number of tools for using single and dual element style transducers
with linearity tables and v-path correction curves. In addition, it should also be noted
that the thickness gauge option has a fully functional scope with the same precision
linearity as the flaw detector option. Therefore, the user should consider the current
application to determine which gauge option will produce the best results. The
following sections outline how to setup and calibrate your
DFX-7
for field use, given a
specific range and material type.
5.1 Setting Up For Calibration
This section covers performing a two point automatic calibration using a single
element straight beam contact transducer with a range from 1 to 4 inches. In order to
accomplish this, a set of calibration standards covering range is required. The steps
are outlined as follows:
DFX-7 Setup