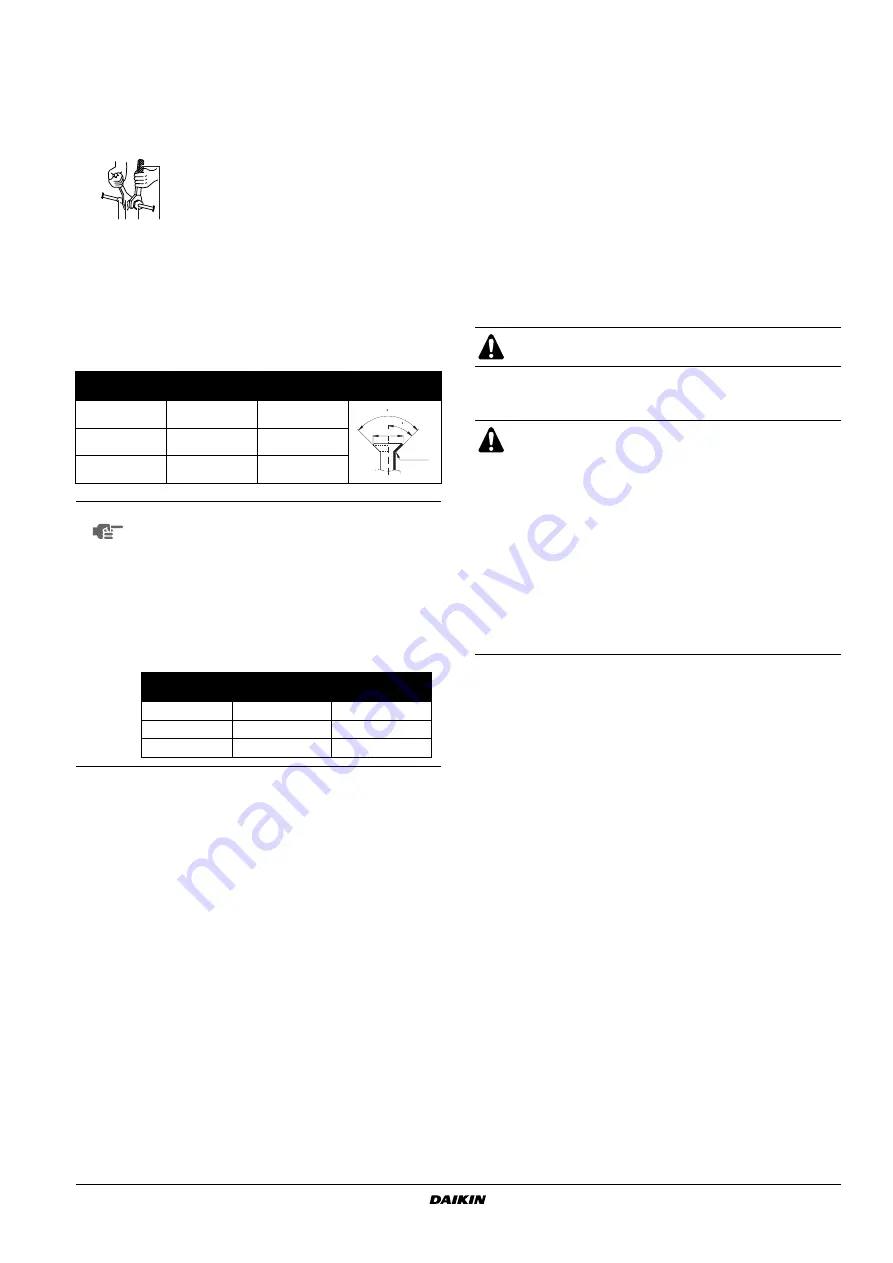
REYQ8~16M8W1B
VRVII System air conditioner
4PW23712-1
Installation manual
10
FLARE SHAPE and FLARENUT TIGHTENING TORQUE
Precautions when connecting pipes
■
See the following table for flare part machining dimensions.
■
When connecting the flare nuts, apply refrigerant oil to the inside
and outside of the flares and turn them three or four times at
first. (Use ether or esther oil).
■
When loosening a flare nut, always use two wrenches in
combination. When connecting the piping, always use a spanner
and torque wrench in combination to tighten the flare nut.
■
See the following table for tightening torque.
(Applying too much torque may cause the flares to crack.)
■
After all the piping has been connected, use nitrogen to perform
a gas leak check.
6.5.
Pipe insulation
After finishing the leak test and vacuum drying, the piping must be
insulated. Take into account the following points:
■
Make sure to insulate the connection piping and refrigerant
branch kits entirely.
■
Be sure to insulate liquid, suction gas, and discharge gas piping
(for all units) and oil equalizing pipe (only for REYQ18~48).
■
Use heat resistant polyethylene foam which can withstand a
temperature of 70°C for liquid side piping and polyethylene foam
which can withstand a temperature of 120°C for gas side piping.
■
If you think the temperature and the relative humidity around the
cooling pipes might exceed 30°C and RH 80%, reinforce the
insulation of the cooling pipes (at least 20
mm thick).
Condensation might be formed on the surface of the insulation.
■
If there is a possibility that condensation on the stop valve might
drip down into the indoor unit through gaps in the insulation and
piping because the outdoor unit is located higher than the indoor
unit this must be prevented by sealing up the connections. See
figure 13
.
6.6.
Additional refrigerant charge
See
figure 12
.
Pipe size
Tightening
Torque (N•m)
A (mm)
Flare shape
Ø9.5
32.7~39.9
12.8~13.2
Ø12.7
49.5~60.3
16.2~16.6
Ø15.9
61.8~75.4
19.3~19.7
NOTE
You must use a torque wrench but if you are obliged to
install the unit without a torque wrench, you may follow
the installation method mentioned below.
After the work is finished, make sure to check that
there is no gas leak.
When you keep on tightening the flare nut with a
spanner, there is a point where the tightening torque
suddenly increases. From that position, further tighten
the flare nut within the angle shown below:
12 3
4
1
Piping union
2
Spanner
3
Flare nut
4
Torque wrench
R=0.4~0.8
45
±
2
90
±
2
A
Pipe size
Further tightening
angle
Recommended
arm length of tool
Ø9.5 (3/8")
60~90°
±200 mm
Ø12.7 (1/2")
30~60°
±250 mm
Ø15.9 (5/8")
30~60°
±300 mm
A
One outdoor unit installed
B
When multiple outdoor units installed
1
Liquid line stop valve
2
Suction gas line stop valve
3
Discharge gas line stop valve
4
Indoor to outdoor interconnecting piping
5
Sealing up treatment
6
Heat insulator
7
Oil-equalizing line stop valve
8
Oil-equalizing line
Be sure to insulate local pipes, as touching them can
cause burns.
Refrigerant cannot be charged until field wiring has been
completed.
Refrigerant may only be charged after performing the leak
test and the vacuum drying (see above).
When charging a system, care shall be taken that its
maximum permissible charge is never exceeded, in view of
the danger of liquid hammer.
Charging with an unsuitable substance may cause
explosions and accidents, so always ensure that the
appropriate refrigerant (R-410A) is charged.
Refrigerant containers shall be opened slowly.
Always use protective gloves and protect your eyes when
charging refrigerant.
1
Presssure reducing valve
2
Nitrogen
3
Tank
4
Siphon system
5
Measuring instrument
6
Vacuum pomp
7
Valve A
8
Valve B
9
Suction gas line stop valve
10
Liquid line stop valve
11
Discharge gas line stop valve
12
stop valve service port
13
Charge hose
14
Indoor unit
15
BS unit
16
Oil-equalizing line stop valve
17
Valve C
18
Outdoor unit
19
Dotted lines represent onsite piping
20
To indoor unit