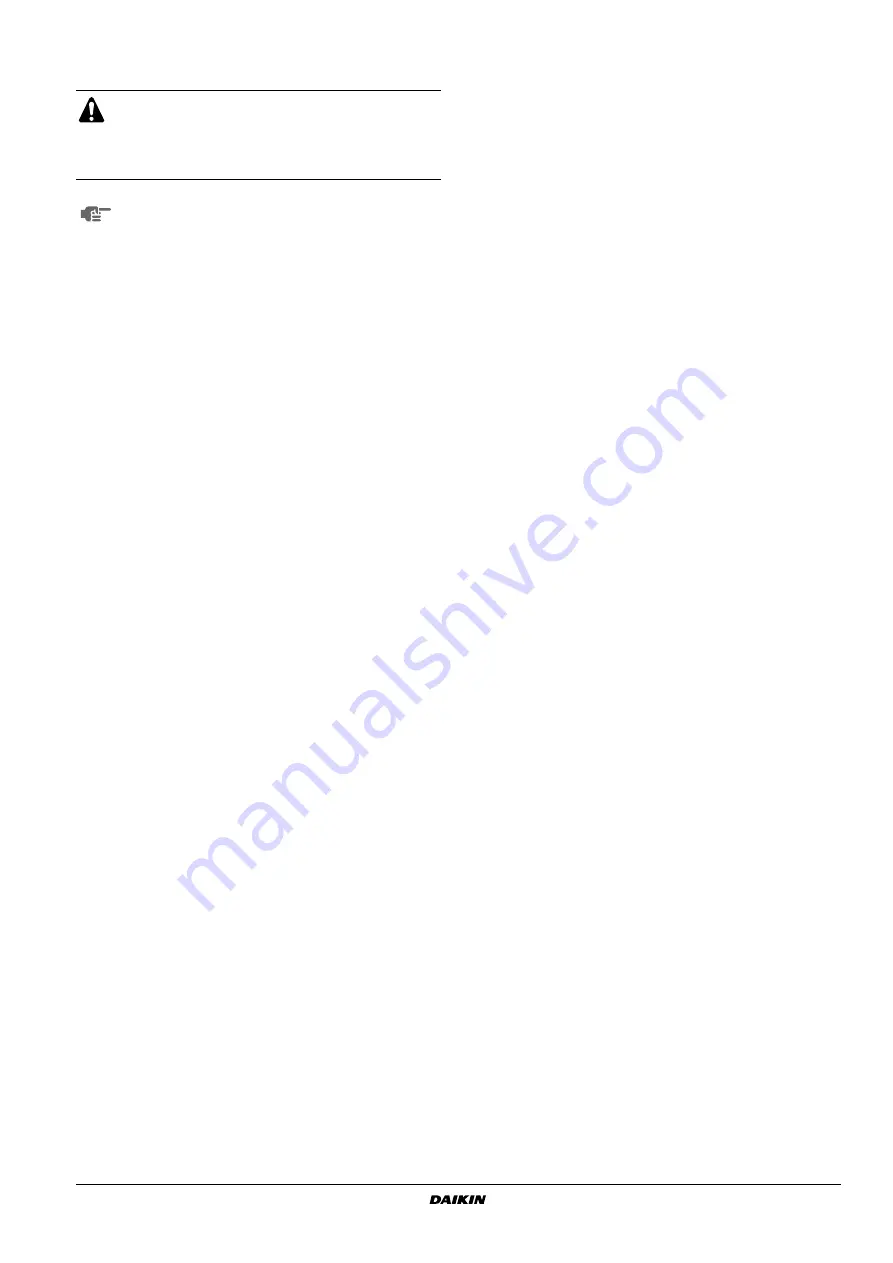
RXYSQ4~6M7V3B
VRVII-S system air conditioner
4PW17806-1C
Installation manual
11
10. E
LECTRICAL
WIRING
WORK
10.1. Internal wiring – Parts table
A1P........................ Printed circuit board (main)
A2P........................ Printed circuit board (inverter)
A3P........................ Printed circuit board (noise filter)
BS1~BS5 ............... Push button switch (mode, set, return, test,
reset)
C1~C3 ................... Capacitor
DS1, DS2............... Dip switch
E1HC ..................... Crankcase heater
F1U........................ Fuse (T6, 3 A/250 V)
F2U........................ Field fuse
H1P~H7P .............. Light emitting diode (service monitor orange)
HAP ....................... Light emitting diode (service monitor green)
K1M ....................... Magnetic contactor (M1C)
K2R........................ Magnetic relay (K1M)
K1R........................ Magnetic relay (Y1S)
K2R........................ Magnetic relay (Y2S)
K4R........................ Magnetic relay (Y3S)
K5R........................ Magnetic relay (E1HC)
L1R ........................ Reactor
M1C ....................... Motor (compressor)
M1F, M2F............... Motor (fan)
PS.......................... Switching power supply
Q1DI ...................... Field earth leak detector (300 mA)
R1 .......................... Resistor (current limiting)
R2 .......................... Resistor (current sensor)
R1T........................ Thermistor (air)
R2T........................ Thermistor (suction)
R3T........................ Thermistor (compressor discharge)
R4T........................ Thermistor (heat exchanger de-icer)
R5T........................ Thermistor (heat exchanger outlet)
S1NPH................... Pressure sensor (high)
S1NPL ................... Pressure sensor (low)
S1PH ..................... Pressure switch (high)
T1R........................ Transformer (230 V/20 V)
V1R, V2R............... Power module (A2P)
V1T ........................ IGBT (A2P)
X1M ....................... Terminal strip (power supply)
X1M ....................... Terminal strip (control)(A1P)
Y1E........................ Electronic expansion valve (main)
Y2E........................ Electronic expansion valve (subcool)
Y1S........................ Solenoid valve (hot gas)
Y2S ........................ Solenoid valve (receiver gas purge)
Y3S ........................ Solenoid valve (4 way valve)
Z1C~Z3C ............... Noise filter (ferrity core)
Z1F......................... Noise filter (with surge absorber)
Cool/heat selector
S1S ........................ Selector switch (fan/cool – heat)
S2S ........................ Selector switch (cool – heat)
10.2. Precautions on electrical wiring work
■
Before obtaining access to terminal devices, all supply circuits
must be interrupted.
■
Use only copper wires.
■
The wiring between the indoor unit and outdoor unit must be for
230 V.
■
Do not turn on the main switch until all the wiring is completed.
Make sure that the main switch has a contact separation of at
least 3 mm in all poles.
■
Never squeeze bundled cables into a unit.
■
Fix cables so that cables do not make contact with the pipes
(especially on high pressure side).
■
Secure the electrical wiring with clamping material as shown in
so that it does not come in contact with the piping,
particulary on the high-pressure side.
Make sure no external pressure is applied to the terminal
connectors.
■
When installing the earth leak detector make sure that it is
compatible with the inverter (resistant to high frequency
electrical noise) to avoid unnecessary opening of the earth leak
detector.
■
As this unit is equipped with an inverter, installing a phase
advancing capacitor not only will deteriorate power factor
improvement effect, but also may cause capacitor abnormal
heating accident due to high-frequency waves. Therefore, never
install a phase advancing capacitor.
■
Follow the "electrical wiring diagram" when carrying out any
electrical wiring.
■
Always ground wires. (In accordance with national regulations of
the pertinent country.)
■
Do not connect the ground wire to gas pipes, sewage pipes,
lightning rods, or telephone ground wires.
•
Combustion gas pipes: can explode or catch fire if there is a gas
leak.
•
Sewage pipes: no grounding effect is possible if hard plastic
piping is used.
•
Telephone ground wires and lightning rods: dangerous when
struck by lightning due to abnormal rise in electrical potential in
the grounding.
■
This unit uses an inverter, and therefore generates noise, which
will have to be reduced to avoid interfering with other devices.
The outer casing of the product may take on an electrical charge
due to leaked electrical current, which will have to be discharged
with the grounding.
10.3. Connection example of total system wiring
■
All wiring must be performed by an authorized
electrician.
■
All components procured on the site and all electric
construction should comply with the applicable local
and national codes.
To persons in charge of electrical wiring work:
Do not operate the unit until the refrigerant piping is
complete. (Running it before the piping is ready will break
the compressor.)
1
Power
2
Earth leak detector
3
Branch switch overcurrent breaker (fuse)
4
Ground
5
Remote controller