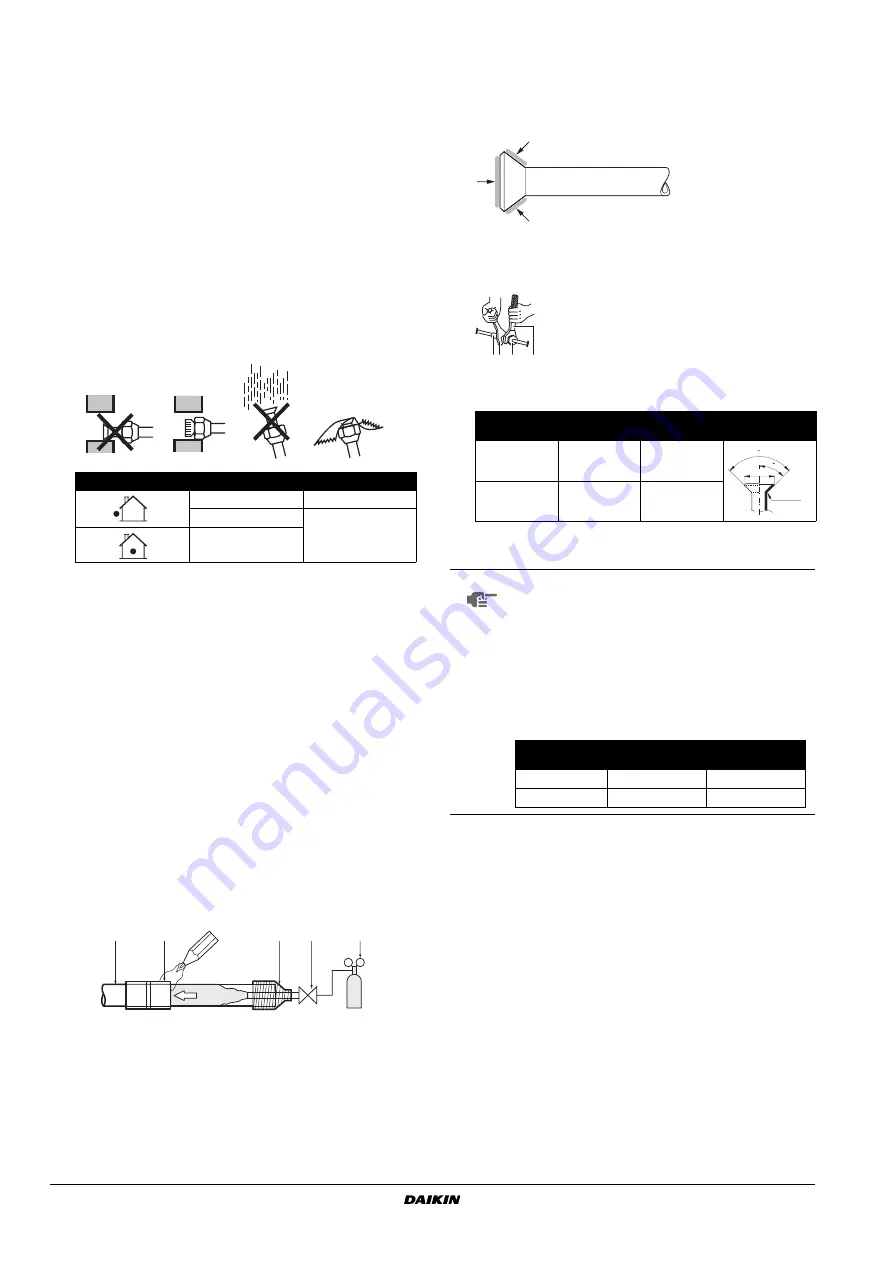
Installation manual
6
RXYSQ4~6M7V3B
VRVII-S system air conditioner
4PW17806-1C
8.
P
RECAUTIONS
ON
REFRIGERANT
PIPING
■
Do not allow anything other than the designated refrigerant to
get mixed into the freezing cycle, such as air, etc. If any
refrigerant gas leaks while working on the unit, ventilate the
room thoroughly right away.
■
Use R-410A only when adding refrigerant
Installation tools:
Make sure to use installation tools (gauge manifold charge hose,
etc.) that are exclusively used for R-410A installations to
withstand the pressure and to prevent foreign materials (e.g.
mineral oils and moisture) from mixing into the system.
Vacuum pump:
Use a 2-stage vacuum pump with a non-return valve
Make sure the pump oil does not flow oppositely into the system
while the pump is not working.
Use a vacuum pump which can evacuate to –100.7 kPa (5 Torr,
–755 mm Hg).
■
In order to prevent dirt, liquid or dust from entering the piping,
cure the piping with a pinch or taping.
Great caution is needed when passing copper tubes through
walls.
■
For handling of stop valves, refer to
■
Only use the flare nuts included with the unit. Using different
flare nuts may cause the refrigerant to leak.
■
Always use the supplied copper gasket when connecting the
gas pipe supplied with the unit. See
8.1.
Cautions for brazing
■
Be sure to carry out a nitrogen blow when brazing.
Brazing without carrying out nitrogen replacement or releasing
nitrogen into the piping will create large quantities of oxidized
film on the inside of the pipes, adversely affecting valves and
compressors in the refrigerating system and preventing normal
operation.
■
When brazing while inserting nitrogen into the piping, nitrogen
must be set to 0.02 MPa with a pressure-reducing valve (=just
enough so that it can be felt on the skin).
8.2.
Cautions for flare connection
■
See the following table for flare part machining dimensions.
■
When connecting the flare nuts, apply refrigerant ether or ester
oil to the inside and outside of the flares and turn them three or
four times at first.
■
When loosening a flare nut, always use two wrenches in
combination. When connecting the piping, always use a spanner
and torque wrench in combination to tighten the flare nut.
■
See the following table for tightening torque.
(Applying too much torque may cause the flares to crack.)
■
After all the piping has been connected, use nitrogen to perform
a gas leak check.
Installation period
Protection method
More than a month
Pinch the pipe
Less than a month
Pinch or tape the
pipe
Regardless of the
period
1
Refrigerant piping
2
Part to be brazed
3
Taping
4
Hands valve
5
Pressure-reducing valve
6
Nitrogen
1
2
3
4
5
6
6
Pipe size
Tightening
Torque (N•m)
A (mm)
Flare shape
Ø9.5
32.7~39.9
12.8~13.2
Ø15.9
61.8~75.4
19.3~19.7
NOTE
You must use a torque wrench but if you are obliged to
install the unit without a torque wrench, you may follow
the installation method mentioned below.
After the work is finished, make sure to check that
there is no gas leak.
When you keep on tightening the flare nut with a
spanner, there is a point where the tightening torque
suddenly increases. From that position, further tighten
the flare nut within the angle shown below:
12 3
4
1
Piping union
2
Spanner
3
Flare nut
4
Torque wrench
R=0.4~0.8
45
±
2
90
±
2
A
Pipe size
Further tightening
angle
Recommended
arm length of tool
Ø9.5 (3/8")
60~90°
±200 mm
Ø15.9 (5/8")
30~60°
±300 mm