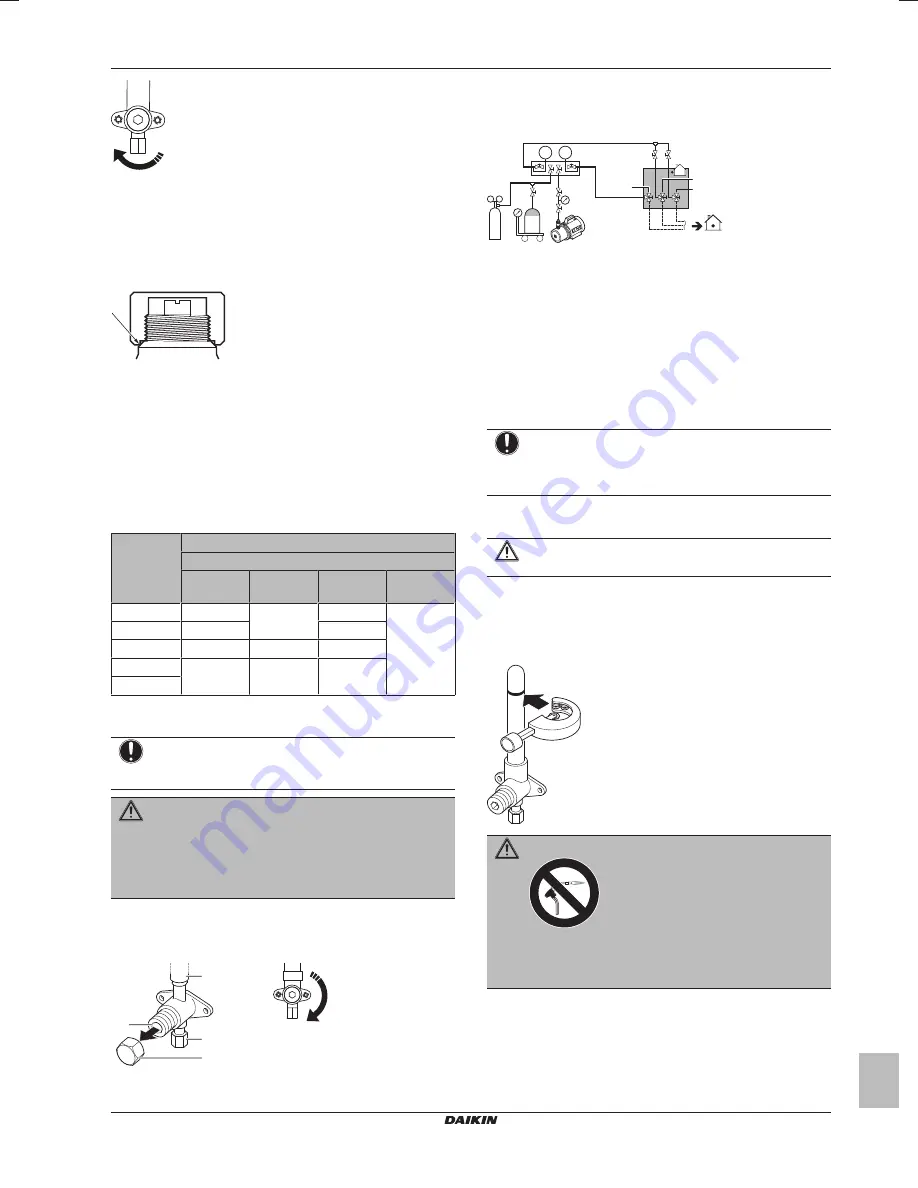
5 Installation
Installation and operation manual
15
RWEYQ8~RWEYQ8~14T9Y1B
VRV IV water-cooled system air conditioner
4P452190-1A – 2017.04
To handle the stop valve cover
▪ The stop valve cover is sealed where indicated by the arrow. Do
NOT damage it.
▪ After handling the stop valve, tighten the stop valve cover
securely, and check for refrigerant leaks. For the tightening
torque, refer to the table below.
To handle the service port
▪ Always use a charge hose equipped with a valve depressor pin,
since the service port is a Schrader type valve.
▪ After handling the service port, make sure to tighten the service
port cover securely. For the tightening torque, refer to the table
below.
▪ Check for refrigerant leaks after tightening the service port cover.
Tightening torques
Stop valve
size (mm)
Tightening torque N•m (turn clockwise to close)
Shaft
Valve body Hexagonal
wrench
Cap (valve
lid)
Service
port
Ø9.5
5.4~6.6
4 mm
13.5~16.5
11.5~13.9
Ø12.7
8.1~9.9
18.0~22.0
Ø15.9
13.5~16.5
6 mm
23.0~27.0
Ø19.1
27.0~33.0
8 mm
22.5~27.5
Ø25.4
5.3.7
To remove the pinched pipes
NOTICE
In case of heat pump mode, do NOT remove the pinched
pipe of the gas line stop valve.
WARNING
Any gas or oil remaining inside the stop valve may blow off
the pinched piping.
Failure to observe the instructions in procedure below
properly may result in property damage or personal injury,
which may be serious depending on the circumstances.
Use the following procedure to remove the pinched piping:
1
Remove the valve cover and make sure that the stop valves are
fully closed.
a
c
d
b
a
Service port and service port cover
b
Stop valve
c
Field piping connection
d
Stop valve cover
2
Connect the vacuuming/recovery unit through a manifold to the
service port of all stop valves.
p< p>
R410A
N2
b
c
e
a
f
g
h
d
A
C
(1)
D
B
a
Pressure reducing valve
b
Nitrogen
c
Weighing scales
d
Refrigerant R410A tank (siphon system)
e
Vacuum pump
f
Liquid line stop valve
g
Gas line stop valve
h
High pressure/low pressure gas line stop valve
A
Valve A
B
Valve B
C
Valve C
(1)
D
Valve D
(1)
Only for heat recovery mode.
NOTICE
Do not connect the vacuum pump to the suction gas stop
valve if the unit is intended to run in heat pump mode. This
will increase the risk of unit failure.
3
Recover gas and oil from the pinched piping by using a
recovery unit.
CAUTION
Do not vent gases into the atmosphere.
4
When all gas and oil is recovered from the pinched piping,
disconnect the charge hose and close the service ports.
5
Cut off the upper part of the liquid, gas, and high pressure/low
pressure gas stop valve pipes along the black line. Use an
appropriate tool (e.g. a pipe cutter, a pair of nippers).
WARNING
Never remove the pinched piping by brazing.
Any gas or oil remaining inside the stop valve may blow off
the pinched piping.
6
Make sure that no particles remain in the pipe. Blow out any
particles with compressed air.
7
Wait until all oil is dripped out before continuing with the
connection of the field piping in case the recovery was not
complete.