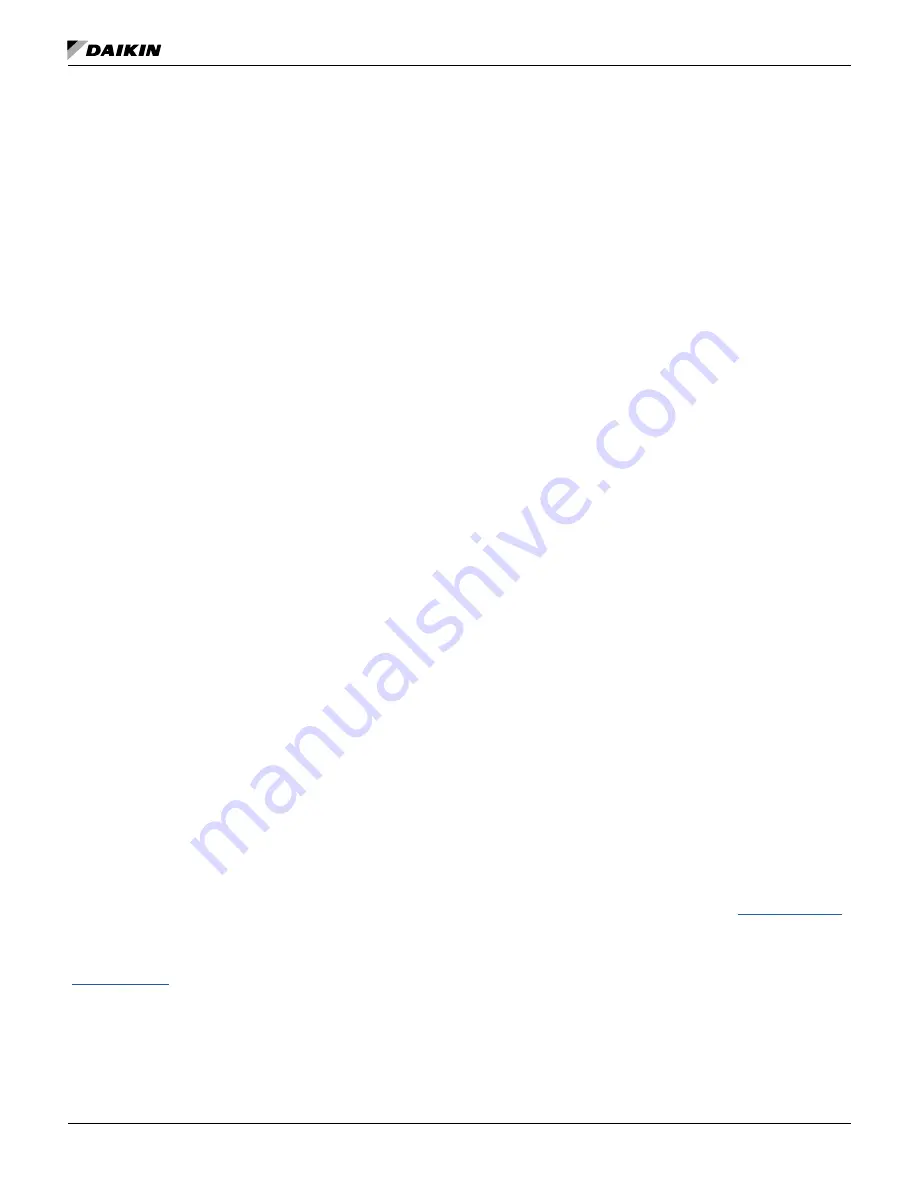
ED 15103-6 • MICROTECH III WSHP UNIT CONTROLLER 4
www.DaikinApplied.com
I
nTroduCTIon
Overview
This purpose of this document is to serve as an integration
guide for the MicroTech
®
III Water Source Heat Pump (WSHP)
Unit Controller from Daikin Applied. It provides the necessary
information to incorporate the WSHP unit controller into
a building automation system (BAS). It lists all BACnet
®
properties,
L
on
W
orks
®
variables, corresponding WSHP unit
controller data points and configuration instructions.
How to use this Guide
Refer to the first section for a glossary for common terms and
protocol definitions.
Use the primary portion of this protocol document, the
BACnet and
L
on
W
orks
summary tables, for point mapping
and addressing details. Some parameters require further
explanation or information beyond what is shown in the tables.
Those affected parameters are noted within each table, along
with the reference to where the additional details can be found.
See
BACnet Configuration and Commissioning
and
for instructions on how to use
configuration and system commissioning and verification tools
for BACnet and
L
on
W
orks
variables.
BACnet and
L
on
W
orks
Effective Occupancy modes. This is
helpful for determining the interaction among the various inputs
that ultimately determine the effective occupancy mode of the
unit.
The
Space Temperature Setpoint Methods
section provides the
temperature setpoint operation details and diagram.
Terminology
Unit Controller Data Points
The WSHP unit controller contains data points or unit variables
that are accessible from a BACnet MS/TP (Master Slave/Token
Passing) network or a
L
on
W
orks
network. Not all points are
accessible from each interface. This document contains the
network details necessary to incorporate the unit controller into
the network.
BACnet Networks
BACnet Protocol
BACnet is a standard communication protocol for Building
Automation and Control Networks developed by the American
National Standards Institute (ANSI) and American Society
of Heating, Refrigeration and Air-conditioning Engineers
(ASHRAE) specified in ANSI/ASHRAE standard 135-2004
(
). It addresses all aspects of the various
systems that are applied to building control systems. BACnet
provides the communication infrastructure needed to integrate
products manufactured by different vendors and to integrate
building services that are now independent.
BACnet Network Compatibility
The WSHP unit controller is tested according to the BACnet
Testing Laboratory (BTL) Test Plan. It is designed to meet
the requirements of the BACnet Standard as stated in the
Protocol Implementation and Conformance Statement (PICS).
However, it is not BTL listed. The PICS are found in
A: Protocol Implementation Conformance Statements (PICS)
with separate documents for Enfinity Single Stage Compressor,
SmartSource Single and Two Stage Compressor, and Enfinity
Large Two Compressor WSHPs.
BACnet Objects
The WSHP unit controller incorporates standard BACnet object
types (i.e., object types defined in the BACnet Standard) that
conform to the BACnet Standard. Each object has properties
that control unit variables or data points. Some object types
occur more than once in the unit controller; each occurrence
or instance has different properties and controls different
unit variables or data points. Each instance is designated
with a unique type and instance index. Some properties
can be adjusted (read/write properties, e.g., setpoints) from
the network and others can only be interrogated (read-only
properties, e.g., status information).
Each data point accessible from a BACnet network is
described with a detailed table that gives the Object Identifier,
Property Identifier, and other information.
l
on
W
orks
Networks
A control network specification for information exchange built
upon the use of LonTalk
®
for transmitting data developed by
the Echelon Corporation.
LonTalk Protocol
A protocol developed and owned by the Echelon Corporation.
It describes how information is transmitted between devices on
a control network.
LonMark Certification
LonMark certification is an official acknowledgement by
the LonMark Interoperability Association that a product
communicates using the LonTalk protocol and transmits and
receives data per a standard LonMark functional profile. The
L
on
W
orks
communication module is in accordance with
the LonMark Heat Pump with Temperature Control functional
profile and is LonMark 3.4 certified. Refer to
for certification conformance information.