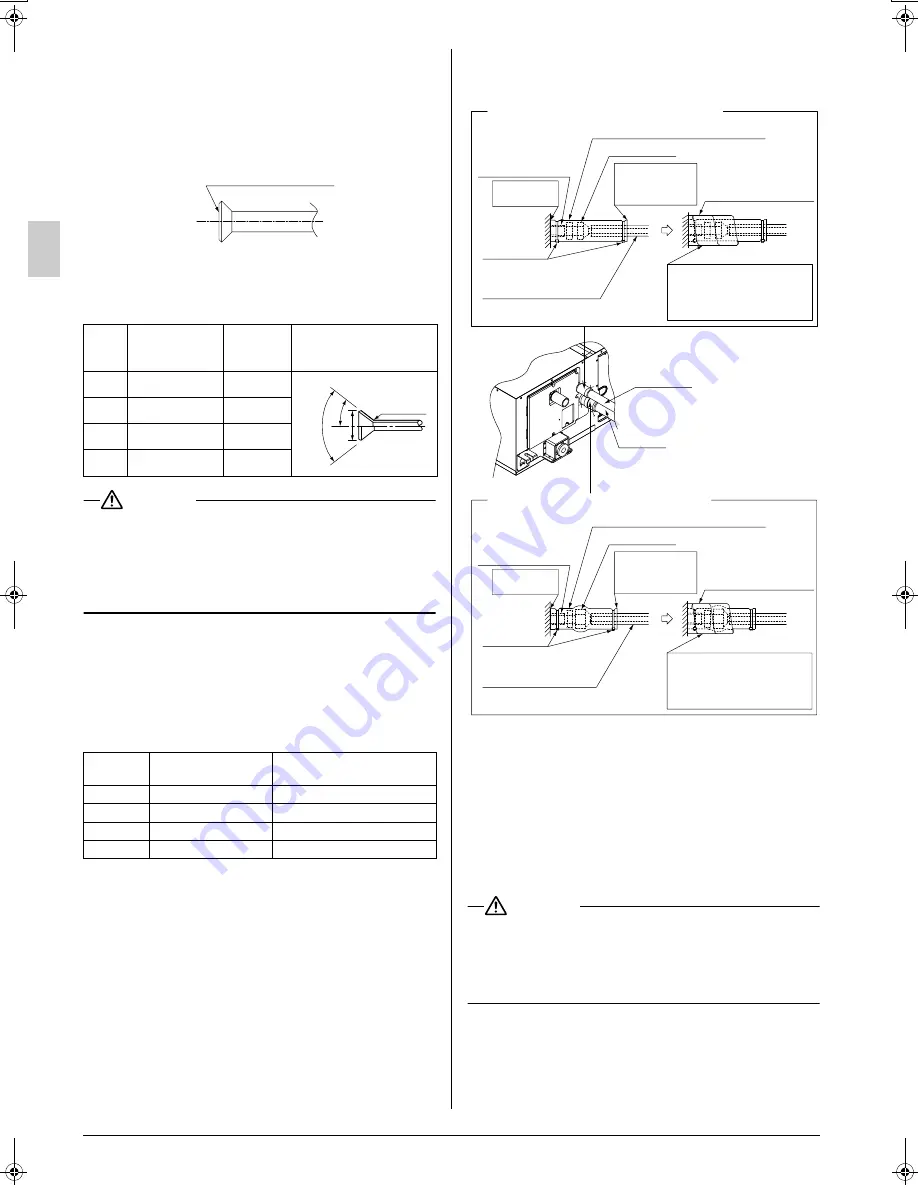
6
English
• Refer to Table 2 for the processing dimensions of the
flare.
• Use the flare nut provided with the unit.
•
Apply ether oil or ester oil only to inner side of the
flare
and screw in the flare nut three to four turns first by
hand at the time of connecting the flare nut.
(Refer to Fig. 5)
• Refer to Table 2 for the corresponding tightening torque.
Table 2
CAUTION
•
Do not excessively tighten the flare nut.
Doing so will break the flare nut and refrigerant leakage may
result.
•
Make sure that all parts around the flare are free of oil.
The drain pan and the resin part may be deteriorated if oil is
attached.
• If no torque wrenches are available, refer to Table 3 as a
standard.
When the flare nut is tightened with the spanner, the
tightening torque should increase suddenly. Tighten the
flare nut further for the corresponding angle shown in
Table 3.
Table 3
(2) On completion of installation work,
check that there is no
gas leakage
.
(3) Refer to the illustration on the right-hand side and be sure to
perform heat insulation work on the piping joints after gas
leakage checks.
(Refer to Fig. 6)
• Use the insulation for fitting (4) and (5) provided to the
liquid piping and gas piping, respectively, and conduct
heat insulation work.
(Tighten both edges of the insulation for fitting (4) and (5)
for each joint with the clamp (8).)
• Make sure that the joint of the insulation for fitting (4) and
(5) for the joint on the liquid piping and gas piping side
faces upward.
• Wrap the middle sealing material (7) around the insula-
tion for fitting (4) and (5) for the joint (flare nut part).
CAUTION
•
Be sure to perform the heat insulation of the local piping
up to the piping joint.
If the piping is exposed, dew condensation may result. Fur-
thermore, a burn may be caused if a human body comes in
contact with the piping.
Pipe
size
Tightening torque
Flare
dimensions
A (mm)
Flare shape
φ
6.4
14.2 – 17.2N·m
8.7 – 9.1
φ
9.5
32.7 – 39.9N·m
12.8 – 13.2
φ
12.7
49.5 – 60.3N·m
16.2 – 16.6
φ
15.9
61.8 – 75.4N·m
19.3 – 19.7
Pipe size
Further tightening angle
Recommended arm length of
tool
φ
6.4
60 to 90 degrees
Approx. 150mm
φ
9.5
60 to 90 degrees
Approx. 200mm
φ
12.7
30 to 60 degrees
Approx. 250mm
φ
15.9
30 to 60 degrees
Approx. 300mm
Fig. 5
Apply ester oil or ether oil
only to inner side of flare.
A
45
0
±2
0
R0.4-0.8
90
0
± 2
0
Heat insulation procedure for gas piping
Insulation material
for piping
(on unit side)
Insulation material
for piping (field supply)
Make sure that
the seam faces
upward.
Clamp (8)
(accessory)
Gas pipe
Liquid pipe
Flare nut joint
Attached to
the surface.
Insulation for fitting (5) (accessory)
Middle sealing pad (7)
(accessory)
Wrap the insulation material
around the portion from the
surface of the main unit to the
upper part of the flare nut joint.
Insulation material
for piping (field supply)
Wrap the insulation material
around the portion from the
surface of the main unit to the
upper part of the flare nut joint.
Fig. 6
Heat insulation procedure for liquid piping
Insulation material
for piping
(on unit side)
Make sure that
the seam faces
upward.
Clamp (8)
(accessory)
Main unit
Flare nut joint
Attached to
the surface.
Insulation for fitting (4) (accessory)
Middle sealing pad (7)
(accessory)
01_EN_3PN06583-7N.fm Page 6 Saturday, February 28, 2009 3:02 PM