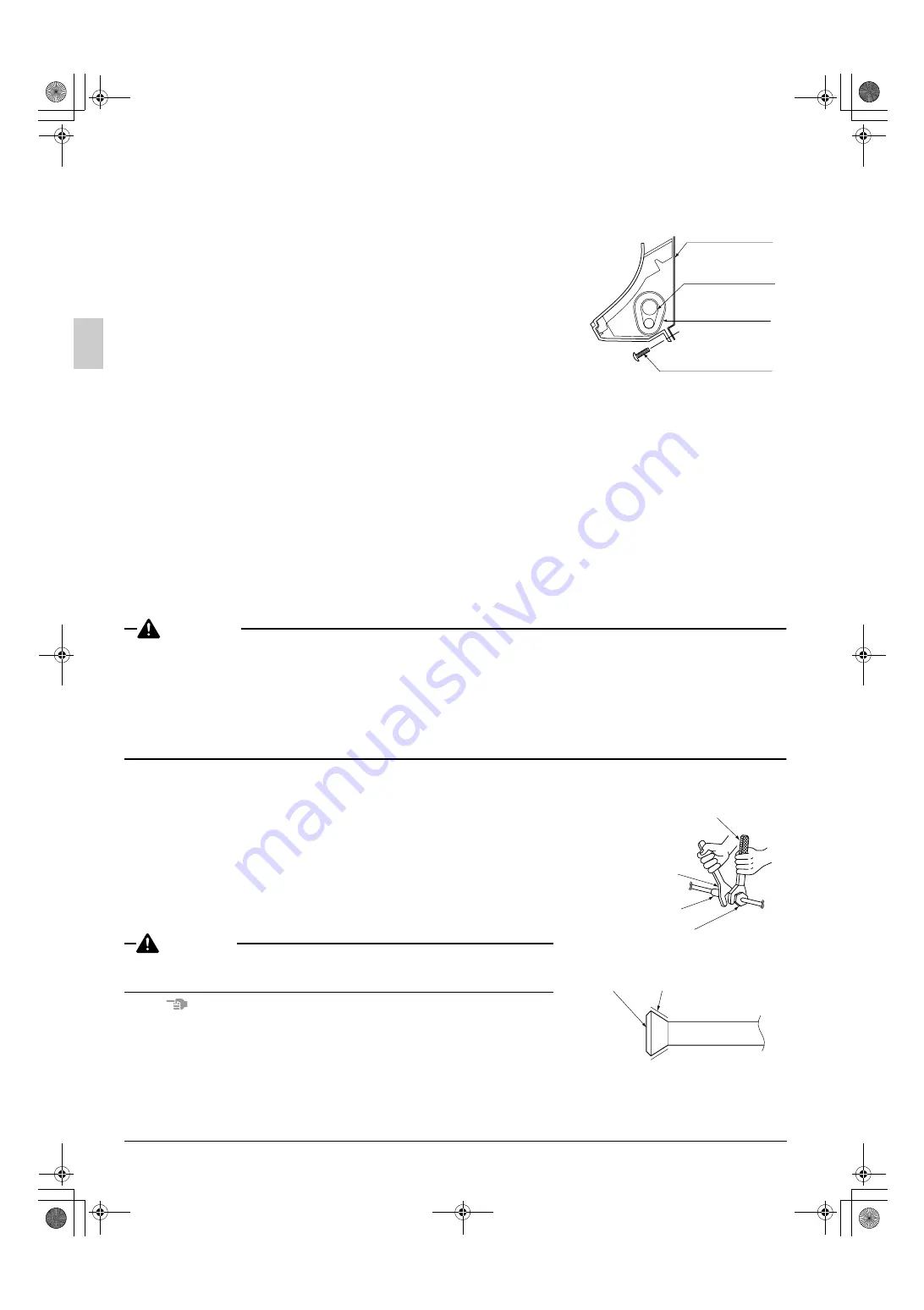
9
English
•
Make sure wiring the units, ground wiring and remote controller wiring are not caught inside the indoor
unit.
■
When screwing in the indoor unit
•
Remove the front grill.
(Refer to Fig. 7)
•
Secure the indoor unit to the installation panel (1) with the securing
screws (6).
(Refer to Fig. 11)
5. REFRIGERANT PIPING WORK
〈〈〈〈
For refrigerant piping of outdoor units, see the installation manual attached to the outdoor unit.
〉 〉 〉 〉
〈〈〈〈
Execute heat insulation work completely on both sides of the gas piping and the liquid piping.
Otherwise, a water leakage can result sometimes.
〉 〉 〉 〉
(When using a heat pump, the temperature of the gas piping can reach up to approximately 120°C, so use
insulation which is sufficiently resistant.)
〈〈〈〈
Also, in cases where the temperature and humidity of the refrigerant piping sections might exceed
30°C or RH80 %, reinforce the refrigerant insulation. (20 mm or thicker) Condensation may form on the
surface of the insulating material.
〉〉〉〉
〈〈〈〈
Before refrigerant piping work, check which type of refrigerant is used. Proper operation is not pos-
sible if the types of refrigerant are not the same.
〉〉〉〉
CAUTION
• Use a pipe cutter and flare suitable for the type of refrigerant.
• Apply ester oil or ether oil around the flare section before connecting.
• To prevent dust, moisuture or other foreign matter from infiltrating the tube, either pinch the end
or cover it with tape.
• Do not allow anything other than the designated refrigerant to get mixed into the refrigerant
circuit, such as air, etc. If any refrigerant gas leaks while working on the unit, ventilate the room
thoroughly right away.
•
The outdoor unit is charged with refrigerant.
•
Use copper alloy seamless pipes (ISO 1337)
•
Be sure to use both a spanner and torque wrench together, as shown
in the drawing, when connecting or disconnecting pipes to/from the
unit.
(Refer to Fig. 12)
•
Refer to “Table 2” for the dimensions of flare nut spaces.
•
When connecting the flare nut, coat the flare section (both inside and
outside) with ester oil or ether oil, rotate three or four times first, then
screw in.
(Refer to Fig. 13)
CAUTION
Over-tightening may cause the flare nuts to crack or the refrigerant to
leak.
NOTE
•
Use the flare nut included with the unit main body.
Installation panel
(accessory) (1)
Refrigerant piping
Insulating tape
(accessory) (4)
M4 × 12L
(accessory) (6)
Fig. 11
Torque wrench
Spanner
Piping union
Flare nut
Fig. 12
Ester oil or ether oil
Fig. 13
01_EN_3P083811-3T.fm Page 9 Friday, September 3, 2004 10:17 AM