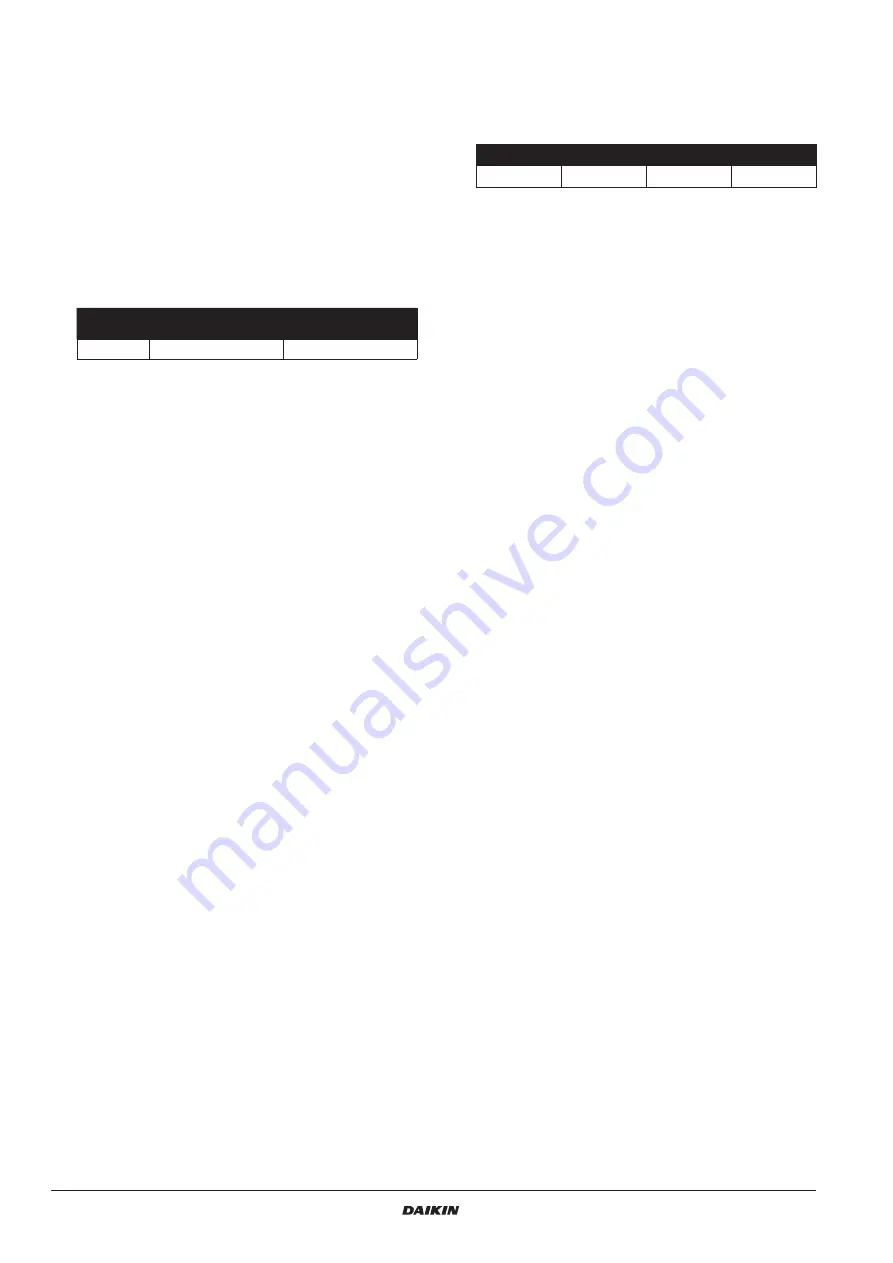
DEIMHP0140521_00EN
6
EWYT~CZ / EWAT~CZ
refrigerants, or flammable or toxic materials shall be stored as
required by national regulations.
■
Open (naked) flames shall not be permitted in machinery rooms,
except for welding, brazing or similar activity and then only provi-
ded the refrigerant concentration is monitored and adequate
ventilation is ensured. Such open flames shall not be left unat-
tended.
■
A remote switching (emergency type) for stopping the refrigera-
ting system shall be provided outside the room (near the door). A
similar acting switch shall be located at a suitable location inside
the room.
■
All piping and ducting passing through floors, ceiling and walls of
machinery room shall be sealed.
■
Hot surfaces shall not exceed a temperature of 80 % of the autoi-
gnition temperature (in °C) or 100 K less than the autoignition
temperature of the refrigerant, whichever is lower.
Refrigerant
Self ignition
temperature
Maximum surface
temperature
R32
648 °C
548°C
■
Machinery rooms shall have doors opening outward and suffi-
cient in number to ensure freedom for persons to escape in an
emergency; the doors shall be tight fitting, selfclosing and so de-
signed that they can be opened from inside (antipanic system).
■
Special machinery rooms where the refrigerant charge is above
the practical limit for the volume of the room shall have a door
that either opens directly to the outside air or through a dedica-
ted vestibule equipped with selfclosing, tightfitting doors.
■
The ventilation of machinery rooms shall be enough both for nor-
mal operating conditions and emergencies.
■
Ventilation for normal operating conditions shall be in accordan-
ce with national regulations.
■
The emergency mechanical ventilation system shall be activated
by a detector(s), located in the machinery room.
■
This ventilation system must be:
• independent of any other ventilation system on the site.
• provided with two independent emergency controls one
located outside the machinery room, and the other inside.
■
The emergency exhaust ventilation fan shall:
• Be either in the air flow with the motor outside the airflow
or rated for hazardous areas (according to the asses-
sment).
• Be located to avoid pressurization of the exhaust ductwork
in the machinery room.
• not cause sparks to occur if it contacts the duct material.
■
Airflow of the emergency mechanical ventilation shall be at
least:
V = 0,014 × m⅔
Where
V
is air flow in m³/s;
m
is the amount of refrigerant present in the machine room,
in kg;
0,014
is a conversion factor.
■
Mechanical ventilation shall be operated continuously or shall
be switched on by the detector.
■
Detector shall automatically activate an alarm, start mechanical
ventilation and stop the system when it triggers
■
The location of detectors shall be chosen in relation to the refri-
gerant and they shall be located where the refrigerant from the
leak will concentrate
■
The positioning of the detector shall be done with due considera-
tion of local airflow patterns, accounting for location sources of
ventilation and louvers. Consideration shall also be given to the
possibility of mechanical damage or contamination.
■
At least one detector shall be installed in each machinery room or
the occupied space being considered and/or at the lowest un-
derground room for refrigerants heavier than air and at the hi-
ghest point for refrigerants lighter than air.
■
Detectors shall be continuously monitored for functioning. In the
case of a detector failure, the emergency sequence should be
activated as if refrigerant had been detected.
■
The preset value for the refrigerant detector at 30 °C or 0 °C, whi-
chever is more critical, shall be set to 25 % of the LFL. The detec-
tor shall continue to activate at higher concentrations.
Refrigerant
LFL
Threshold level
R32
0.307 kg/m³
0.7675 kg/m³
36000 ppm
■
All electrical equipment (not only the refrigerating system) shall
be selected to be suitable for use in the zones identified in the
risk assessment. Electrical equipment shall be deemed to com-
ply with the requirements if the electrical supply is isolated when
the refrigerant concentration reaches 25 % of the lower flam-
mable limit or less.
■
Machinery rooms or special machinery rooms shall be
clearly
marked
as such on the entrances to the room, together with
warning notices indicating that unauthorized persons shall not
enter and that smoking, naked light or flames are prohibited. The
notices shall also state that, in the event of an emergency, only
authorized persons conversant with emergency procedures
shall decide whether to enter the machinery room. Additionally,
warning notices shall be displayed prohibiting unauthorized ope-
ration of the system
■
The owner / operator shall keep an updated logbook of the refri-
gerating system.
Summary of Contents for EWAT016CZN-A1
Page 2: ......
Page 28: ...Notes...