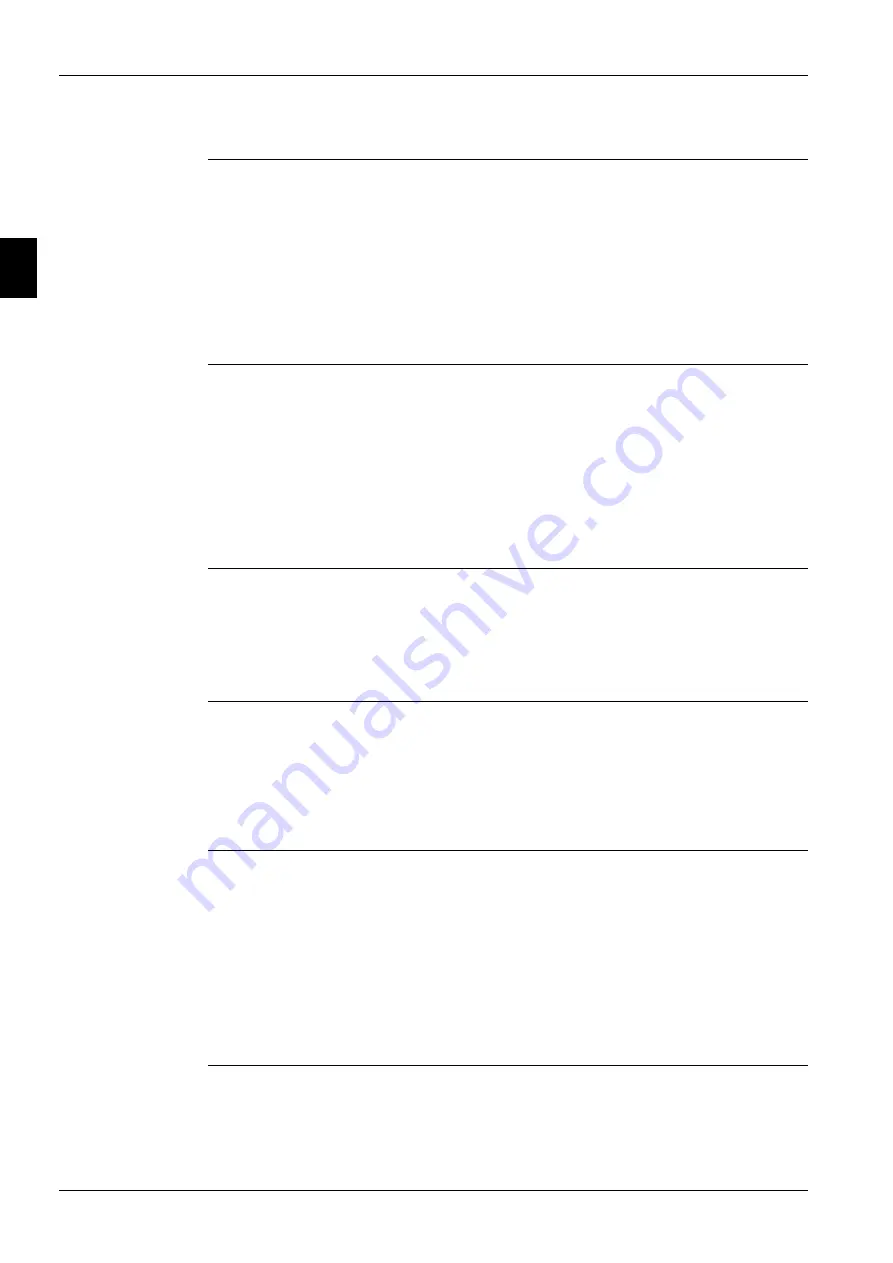
Functional Control
ESIE10-01
2–38
Part 2 – Functional Description
3
1
2
4
5
2.2.10 Unit Capacity Overrides
Unit capacity limits can be used to limit total unit capacity in Cool mode only. Multiple limits may be
active at any time, and the lowest limit is always used in the unit capacity control.
Soft load, demand limit, and network limit should use a deadband around the actual limit value, such
that unit capacity increase is not allowed within this deadband. If unit capacity is above the deadband,
capacity should be decreased until it is back within the deadband.
■
For 2 circuit units, the deadband should be 7%.
■
For 3 circuit units, the deadband should be 5%.
■
For 4 circuit units, the deadband should be 4%.
Soft load
Soft Loading is a configurable function used to ramp up the unit capacity over a given time. The set
points that control this function are:
■
Soft Load - (ON/OFF).
■
Begin Capacity Limit - (Unit %).
■
Soft Load Ramp - (seconds).
The Soft Load Unit Limit increases linearly from the Begin Capacity Limit set-point to 100% over the
amount of time specified by the Soft Load Ramp set-point. If the option is turned off, the soft load limit
is set to 100%.
Demand limit
The maximum unit capacity can be limited by a 4 to 20 mA signal on the Demand Limit analog input
at the unit controller. This function is only enabled if the Demand Limit set point is set to ON.
As the signal varies from 4 mA up to 20 mA, the maximum unit capacity changes by steps of 1% from
100% to 0%. The unit capacity shall be adjusted as needed to meet this limit, except that the last
running compressor cannot be turned off to meet a limit lower than the minimum unit capacity.
Network limit
The maximum unit capacity can be limited by a network signal. This function is only enabled if the unit
control source is set to network. The signal will be received through the BMS interface on the unit
controller.
As the signal varies from 0% up to 100%, the maximum unit capacity changes from 0% to 100%. The
unit capacity shall be adjusted as needed to meet this limit, except that the last running compressor
cannot be turned off to meet a limit lower than the minimum unit capacity.
Current limit
Current Limit control is enabled only when the current limit enable input is closed.
Unit current will be calculated based on the 4-20 mA input that receives a signal from an external
device. The current at 4 mA is assumed to be 0, and the current at 20 mA is defined by a set point. As
the signal varies from 4 to 20 mA, the calculated unit current varies linearly from 0 amps to the amp
value defined by the set point.
The current limit should use a deadband centered around the actual limit value, such that unit capacity
increase is not allowed when current is within this deadband. If unit current is above the deadband,
capacity should be decreased until it is back within the deadband. The current limit deadband should
be 10% of the current limit.
Maximum LWT
pulldown rate
The maximum rate at which the leaving water temperature can drop shall be limited by the Maximum
Rate set point, only when the LWT is less than 15°C.
If the pulldown rate is too fast, the unit capacity will be reduced until the rate is less than the Maximum
Pulldown Rate set point.
Summary of Contents for EWAD620-C17C-SS
Page 2: ......
Page 8: ...ESIE10 01 1 2 Part 1 System Outline 3 1 1 5...
Page 111: ...ESIE10 01 General Outline Part 1 System Outline 1 105 3 1 4 5 1 36 1 Power Compressor 1 2...
Page 112: ...General Outline ESIE10 01 1 106 Part 1 System Outline 3 1 1 4 5 1 36 2 Power Compressor 3...
Page 113: ...ESIE10 01 General Outline Part 1 System Outline 1 107 3 1 4 5 1 36 3 Kit Pumps...
Page 122: ...General Outline ESIE10 01 1 116 Part 1 System Outline 3 1 1 4 5 1 36 12 Digital Inputs Board...
Page 123: ...ESIE10 01 General Outline Part 1 System Outline 1 117 3 1 4 5 1 36 13 Digital Outputs Board...
Page 124: ...General Outline ESIE10 01 1 118 Part 1 System Outline 3 1 1 4 5 1 36 14 Digital Outputs Board...
Page 127: ...ESIE10 01 General Outline Part 1 System Outline 1 121 3 1 4 5 1 36 17 Extension Control Fans 4...
Page 131: ...ESIE10 01 General Outline Part 1 System Outline 1 125 3 1 4 5 1 36 21 EEXV Compressor 1...
Page 134: ...General Outline ESIE10 01 1 128 Part 1 System Outline 3 1 1 4 5 1 36 24 EEXV Compressor 2...
Page 137: ...ESIE10 01 General Outline Part 1 System Outline 1 131 3 1 4 5 1 36 27 EEXV Compressor 3...
Page 138: ...General Outline ESIE10 01 1 132 Part 1 System Outline 3 1 1 4 5 1 36 28 Pumps Control...
Page 139: ...ESIE10 01 General Outline Part 1 System Outline 1 133 3 1 4 5 1 36 29 Terminals M1 M2...
Page 140: ...General Outline ESIE10 01 1 134 Part 1 System Outline 3 1 1 4 5 1 36 30 Terminals M3...
Page 141: ...ESIE10 01 General Outline Part 1 System Outline 1 135 3 1 4 5 1 36 31 Terminals M5 MQ...
Page 148: ...General Outline ESIE10 01 1 142 Part 1 System Outline 3 1 1 4 5...
Page 150: ...ESIE10 01 2 2 Part 2 Functional Description 3 1 2 5...
Page 170: ...The Digital Controller ESIE10 01 2 22 Part 2 Functional Description 3 1 2 4 5...
Page 200: ...Functional Control ESIE10 01 2 52 Part 2 Functional Description 3 1 2 4 5...
Page 202: ...ESIE10 01 3 2 Part 3 Troubleshooting 3 1 3 5...
Page 254: ...Alarms and Events ESIE10 01 3 54 Part 3 Troubleshooting 3 1 3 4 5...
Page 266: ...Controller Inputs and Outputs ESIE10 01 3 66 Part 3 Troubleshooting 3 1 3 4 5...
Page 280: ...ESIE10 01 4 2 Part 4 Commissioning and Test Run 3 1 4 5...
Page 286: ...Pre Test Run Checks ESIE10 01 4 8 Part 4 Commissioning and Test Run 3 1 4 5...
Page 289: ...ESIE10 01 Running Data Part 4 Commissioning and Test Run 4 11 3 4 5 1...
Page 290: ...Running Data ESIE10 01 4 12 Part 4 Commissioning and Test Run 3 1 4 5...