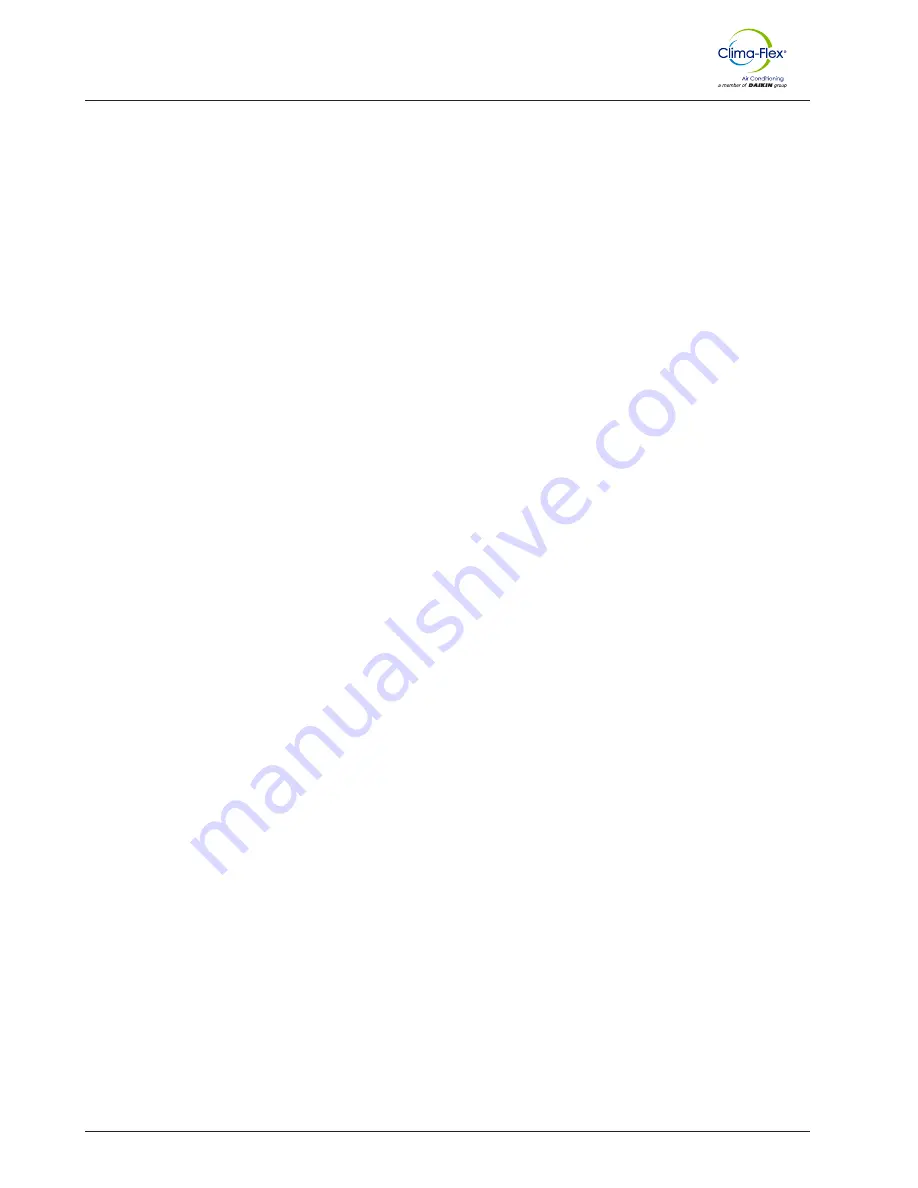
iom-cliv-cf-eng
www.clima-flex.com
41
Unit Maintenance
COMPRESSOR MAINTENANCE
Service or maintenance of these units should be performed
by experienced personnel with specific refrigeration training.
Safety devices should be checked repeatedly and cycling control
components should be analyzed and corrected before resetting
is initiated.
The simplified design of the refrigeration circuit totally eliminates
potential problems during regular operation of the unit. No
maintenance is required on the refrigeration circuit as long as the
unit is operated on a regular basis.
Ease of maintenance has been considered during the design
phase; thus, the unit is easily accessible for service and
maintenance. By accessing the panel located on the front of the
unit, service and maintenance of the unit can be performed easily.
The electrical components are located in the terminal box on the
top of the front panel, which allows easy access to them.
Under normal circumstances, this water chiller only requires a
check and cleaning of the air inlet through the coil surface. This
can be done on a monthly or quarterly basis depending on the
environment in which the units are installed.
When the environment is constantly invaded with grease or dust
particles, the coils should be cleaned by an air conditioning
service technician on a regular basis to ensure adequate cooling
capacity and therefore efficient operation of the unit. The regular
life span of the unit can be shortened if proper service is not
performed.
For consistent durability and performance of the unit, proper
maintenance should always be performed on a regular basis.
During extended periods of operation, the heat exchanger will
become fouled, impairing the effectiveness and reducing the units
performance. Consult your local supplier regarding the cleaning
of the heat exchanger.
The internal water circuit does not require major maintenance or
service, except for water pump failure. It is recommended that
the water filter be checked regularly and replaced if it is dirty or
clogged.
Always check the water level in the system to protect the moving
components in the hydraulic kit from overheating and excessive
wear.
NOTE: The company is not responsible for the malfunction
of the unit if the main cause is lack of maintenance
or the operating conditions of the unit do not
correspond to those recommended in this manual.
MAINTENANCE
GENERAL
Routine checks and maintenance should be performed during
initial operation as well as periodically during start-up. These
include verification of liquid lines, condensation and suction
pressure measurements, as well as checking the unit for normal
overheating and undercooling. A maintenance schedule is
recommended at the end of this section.
The internal pressure and surface temperature of the compressor
are DANGERs and can cause permanent injury.
Operators, installers and maintenance personnel require proper
skills and tools.
Tube temperatures can exceed 100°C and cause severe burns.
Perform periodic service inspections to ensure system reliability.
To avoid system-related compressor problems, periodic
maintenance is recommended:
• Verify that safety devices are operational and properly
configured.
• Make sure that the system is airtight.
• Verify compressor current consumption.
• Confirm that the system is operating in a consistent manner,
check previous maintenance records and environmental
conditions.
• Verify that all electrical connections are properly tightened.
• Keep the compressor clean and verify the absence of rust
and oxidation on the compressor, frame, tubing and electrical
connections.
ELECTRICAL TERMINALS
Electrical connections should be inspected and tightened if
necessary. Heat and vibration can cause connections to loosen
and fall out, thus causing arc flash stress.
For servicing electrical components:
• Disconnect main power lines before repairing or replacing
any components or cables.
• Tighten all wire connections attached to the terminal block
and/or components.
• Check connectors, cables and/or components for burn marks,
frayed wires, etc. If any of them present these conditions, they
should be repaired. or replaced.
• The voltage on the equipment should be checked with a meter
periodically to ensure adequate power supply.
NOTE: Each unit comes with complete wiring. Have the
diagrams handy when making connections.
Electrical connections required at the time of
installation are: Power line to power inlet and
control wiring for the remote control. Do not wire
the remote control with high voltage wires. High
voltage may interfere with the control signals and/
or may cause erratic or poor operation.