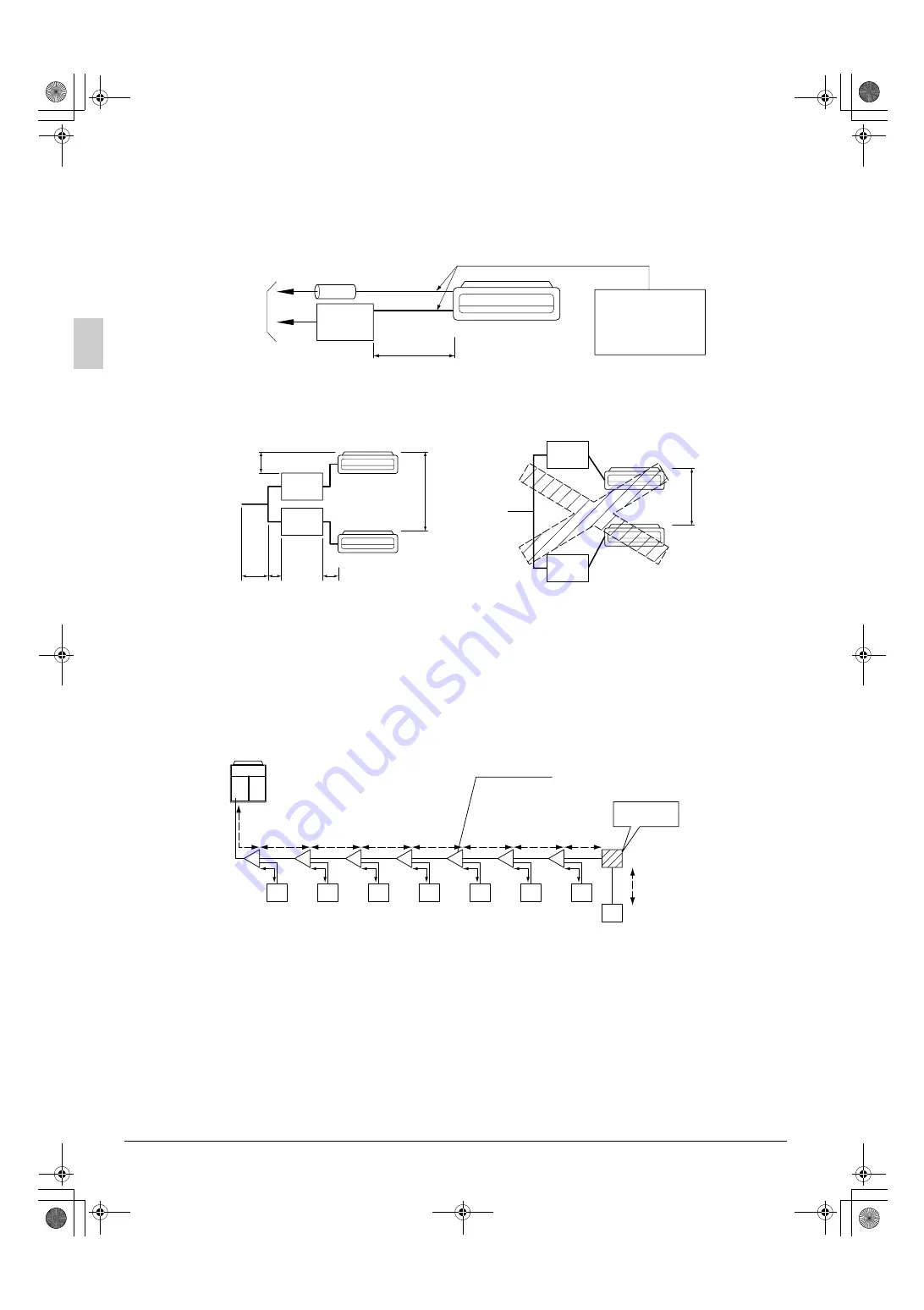
10
English
Piping connection procedure
•
Make sure the length of the refrigerant piping between the BEV unit and the indoor unit is no more than 5m
and that the difference in height is at least 4m.
(1) Connection example for the indoor unit
•
Only one indoor unit may be connected to each BEV unit.
(2) Height difference between indoor units
•
Install the BEV unit in the 15m range of difference in height between the indoor units.
•
Make sure the difference in height between the BEV unit and the indoor unit is no more than 4m.
(3) Allowable length after split (actual piping length)
B+C
≤
35m (length from the first branch piping to the indoor unit)
(4) Additional refrigerant amount
When measuring the amount of additional to refrigerant to fill, include the length of the liquid piping
between the BEV unit and the indoor unit.
Additional filling amount = a+b+c+d+e+f+g+h+i+j+k+l+m+n+p+q
Refer also to the installation manual included with the outdoor unit.
7. ELECTRIC WIRING WORK
7-1 GENERAL INSTRUCTIONS
•
All field supplied parts and materials and electric works must conform to local codes.
•
Use copper wire only.
•
For electric wiring work, refer to also
“
WIRING DIAGRAM
”
attached to the control box lid.
•
For remote controller wiring details, refer to the installation manual attached to the remote controller.
•
All wiring must be performed by an authorized electrician.
Outdoor unit
BEV unit
Gas piping
Liquid piping
L = 5m or less
Adjusted to fit the
size of the piping
connection hole on
the indoor unit.
Fig. 12
BEV
unit
BEV
unit
BEV
unit
BEV
unit
A
B
C
4m or
less
15m or less
15m
Outdoor unit
Outdoor unit
Fig. 13
Example of refrigerant branch using a REFNET joint
REFNET joint
Outdoor unit
Indoor unit (1-8)
BEV unit
a
b
h
i
j
k
l
m
n
q
c
d
e
f
g
p
1
2
3
4
5
6
7
8
Fig. 14
A
B
C
D
E
F
G
3P084604-2A_Eng.fm Page 10 Wednesday, March 3, 2004 10:01 AM