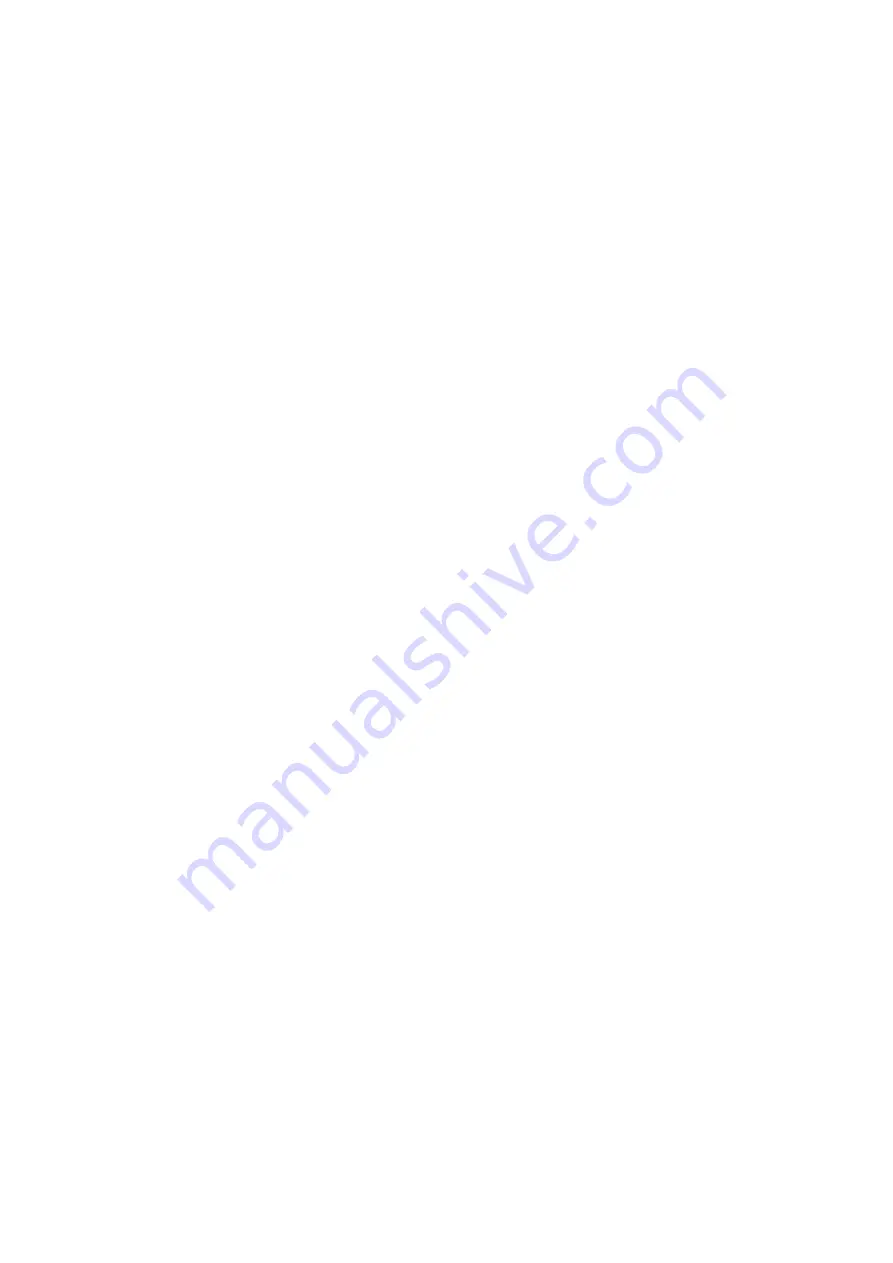
-
42
-
10.
OPERATION
(Continued)
(2) Fine adjustment of anti-stick(burn-back) Voltage : F2
Anti-stick(burn-back) voltage means the voltage which is output when processing is carried out
to prevent wire from sticking to the base metal at the end of welding. Anti-stick(burn-back)
voltage is preset to proper conditions according to welding method and wire diameter at
shipment, but it can be finely adjusted by setting F2. The standard anti-stick(burn-back) voltage
is preset to “0”. When required set F2 in the negative direction to reduce anti-stick voltage, or
set F2 in the positive direction to raise the voltage. The fine adjustment range is 0V to ±9.9V.
(3) Fine Adjustment of Slow Down Speed: F3
Slow-down speed means the speed to feed wire that is slower than the feed rate at normal
welding during the period from triggered torch switch to arc start. The slow down speed is preset
to proper conditions according to welding methods and diameters at shipment, but it can be
finely adjusted by activating F3. The standard slowdown speed is preset to “0” When the
slowdown speed is set in the negative direction, it decrease. When set F3 in the positive
direction, it increase. The fine adjustment range is 0 m/min – ±1.0 m/min. When poor arc start
occurred, lower the slow-down speed. Even when arc start is good, the slow-down speed can
be increased to shorten tact time.
NOTE: The minimum slow-down speed is 0.4 m/min.
10.2.1 Setting of Internal Function (continued)
(4) Switch of Auto/Semi-automatic Mode: F4
Set F4 to “0” to switch to “semi-auto” mode.
In “semi-auto” mode, the “operation stop” status can be canceled only after turning on the
power supply again.
The default factory setting is “semi-auto” mode.
Set F4 to “1” or “2” to switch to “auto” mode. The “auto” mode has the following features:
⚫
To release “operation stop” status just by re-short-circuiting the Operation Stop Terminals.
⚫
After anti-stick (burn-back) voltage time, the voltage is applied for approximately 0.2
second for prevent wire stick on base metal.
Set F4 to “1” when connected to automatic welding equipment to input welding current or
voltage command by means of external voltage signal. When F4 is set to “2”, current or voltage
adjustment can only be performed through a remote control box or the control panel, but not
by means of external voltage signal. In “semi-auto” mode, the setting values by the control
panel will be applicable, even if voltage signal is externally input to the socket for remote control
box.