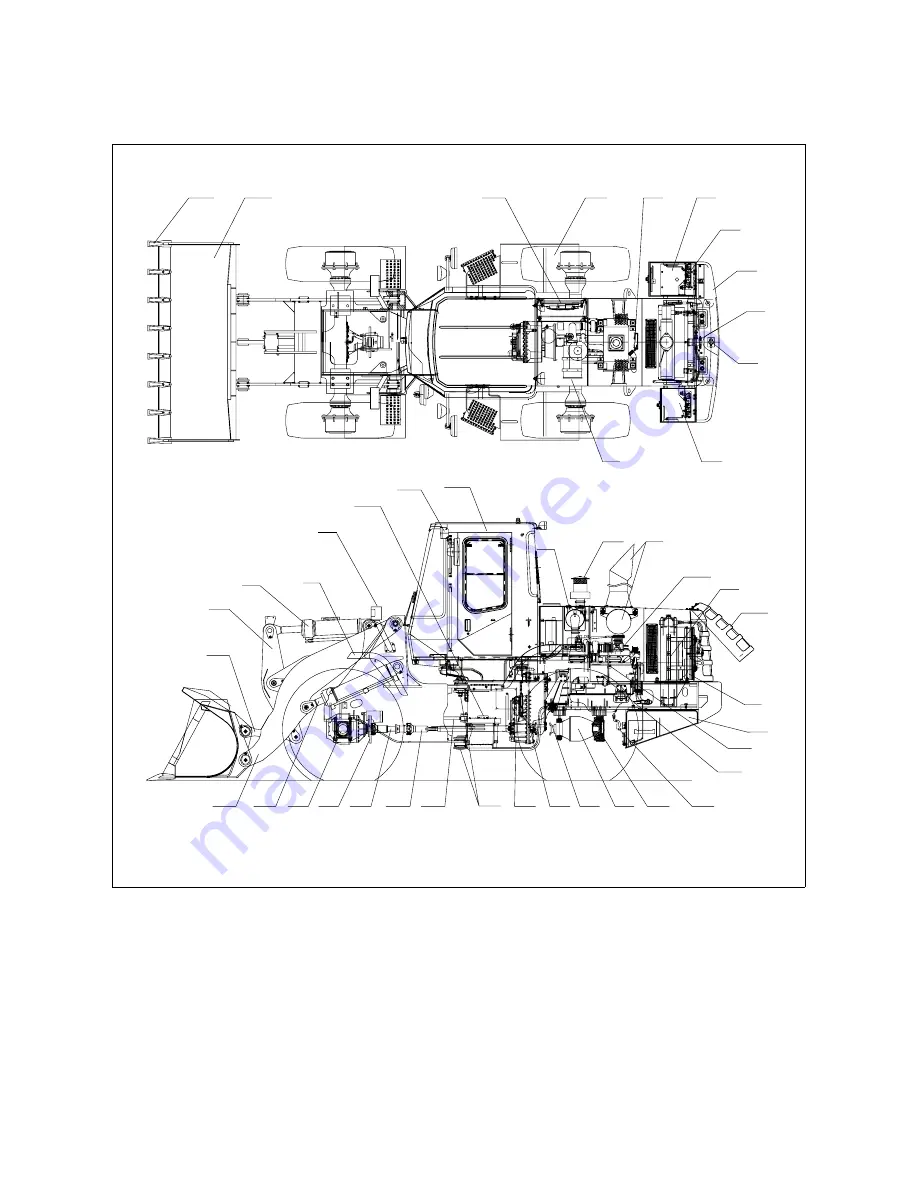
2-4 Operating Controls
022-00028AE Operation and Maintenance Manual
MEGA 200-V (Tier II)
(Tier I - European low noise kit)
The following figure identifies the location of major machine components.
1
2
3
4
5
6
7
8
10
11
12
13
14
15
16
17
18
19
20
21
22
23
24
25
30
29
28
27
26
31
32
33
34
35
36
44
43
42
41 40 39
38
37
APO0020L
9
Figure 2