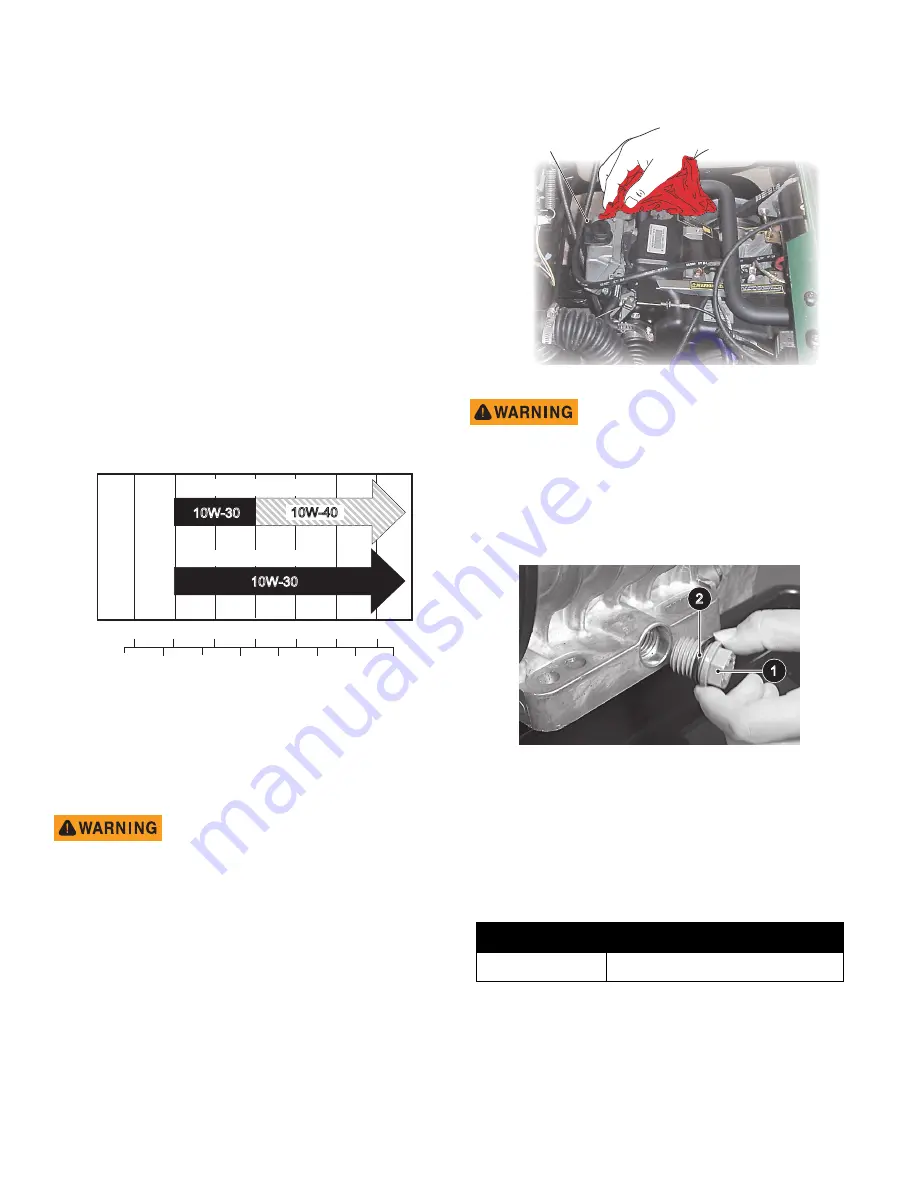
B
114
Repair and Service Manual
ENGINE
Read all of SAFETY and this section before attempting any procedure. Pay particular attention to Notices, Cautions, Warnings and Dangers.
653045
Changing the Oil
Tool List
Qty.
Socket, 19 mm.............................................................1
Ratchet ........................................................................ 1
Extension, 8" ...............................................................1
Oil Filter Wrench..........................................................1
Oil Drain Pan ...............................................................1
Shop Towels .............................................................AR
For maximum performance and longevity, the engine oil
should be replaced after the first 8 hours of operation.
After the initial oil change, it should be changed every 125
hours of operation or semi-annually, whichever comes
first.
The selection of oil is dependent upon the service that the
vehicle will perform. Most vehicles require 10W-30 oil,
whereas vehicles used at capacity or near capacity load
applications will utilize 10W-40 oil after a break-in period
Fig. 3 Oil Viscosity Chart
NOTICE: If vehicle is to be stored over the winter
months, it can be stored with the old oil left in
engine. The oil should be changed as part of spring
maintenance to remove any moisture that has accu-
mulated during storage.
Engine fluids can be hot and con-
tact with the skin can cause severe
burns. Wear rubber gloves to pro-
tect skin from exposure to the old oil and degreaser.
The oil should be changed with engine warm. Park the
vehicle on a level surface, engage parking brake and
remove the key from the vehicle (Ref. Fig. 4).
Fig. 4 Cleaning Top of Engine
Be careful of hot oil when drained. It
may be hot enough to burn you
severely.
1.
Wipe the top of the engine clean with a cloth.
Remove the oil fill cap.
2.
Place an oil drain pan under the oil drain plug (1)
(Ref. Fig. 5) found at the rear of the engine base.
3.
Remove the drain plug (1). Allow the oil to drain into
the drain pan.
Fig. 5 Oil Drain Plug
4.
Before installing the drain plug (1), clean the area
around the drain plug hole with a lint free cloth.
5.
Inspect the drain plug (1) for damage; replace if nec-
essary (Ref. Fig. 5). If the o-ring (2) on the drain plug
is damaged, replace it with a new one.
6.
Tighten the drain plug (1) to the torque value speci-
fied below.
At the first oil change,
small
metal particles can be pres-
ent. This is normal and is a result of the engine break-in
process. Inspect the filter at every oil change. The pres-
ence of large metal chips can indicate possible damage to
-20
0
20
40
60
80
100
-30
-20
-10
0
10
20
30
40
C
F
0
0
10W-30
10W-40
HEAVY DUTY WORK
LIGHT DUTY WORK
(AIR TEMPERATURE)
10W-30
Item
Torque Specification
1
61 in. lbs (7 Nm)
Oil Fill Cap
1
2
Property of American Airlines