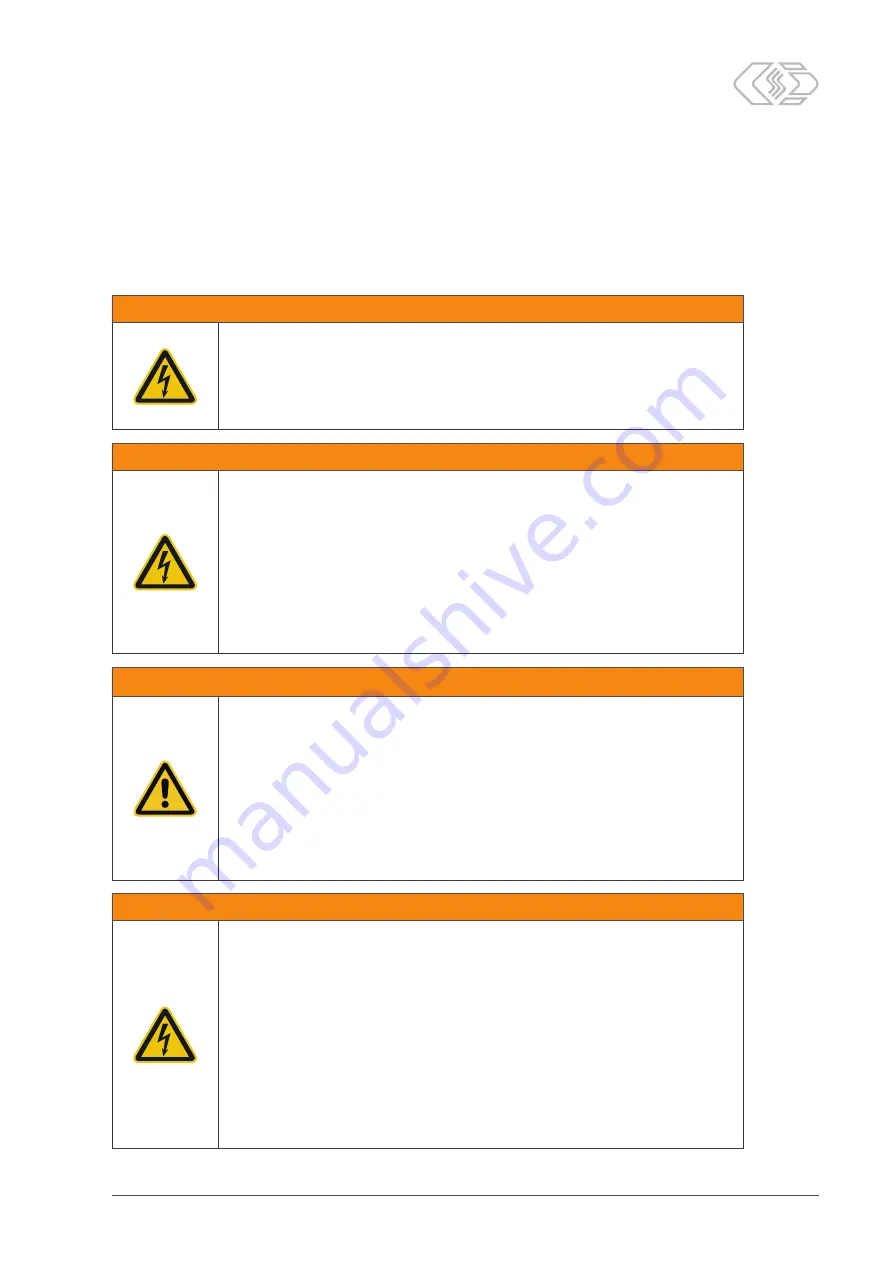
HV Breakout Module – Safety Instructions
Installation Manual
2
Version 01.20 // 2021
2 Safety Instructions
This chapter contains important safety information. Please read the following paragraphs
carefully.
2.1 General safety instructions
WARNING!
HV Breakout Modules (HV BM) are used in high-voltage applications.
Improper handling of HV Breakout Modules may result in electrical
shocks which are dangerous to life.
)
Use only qualified and trained personnel.
)
Observe safety instructions.
WARNING!
The orange cover of the housing may be opened to mount or remove the
HV power cables.
)
Before handling, especially before opening the cover, make sure that the
HV power cables have been disconnected.
)
HV BM 1.1/1.2: Fasten HV power cables only with the supplied or, alterna-
tively, suitable ring terminals and nuts.
)
Observe the mounting instructions in this installation manual. It is parti-
cularly important that cover and PG glands are properly mounted in order
to ensure the tightness of the housing.
WARNING!
When using
HV power cables
made of aluminum
and ring terminals made
of an electrochemically nobler metal (copper), the contact resistance
between the two components increases.
This can lead to a massive increase in temperature and in the worst case
to the development of fire.
"
If ring terminals made of copper are used for connecting HV Breakout
Modules, make sure that only HV power cables made of copper are used.
HV power cables made of aluminum
require a specific connection technique.
Please contact our technical support for further information.
WARNING!
The improper opening of the device housing impairs the operational safety
of the HV measurement module and entails the risk of life-threatening
electrical shocks.
)
Open the housing only to connect the HV power cables and then close it
carefully.
)
Do not carry out any mechanical or electrical modifications on the
HV measurement module.
)
Do not replace the shunt module.
)
Only operate the measurement module when the housing is closed.
HV Breakout Modules are not integrated into the interlock loop. When
the cover is open, there may be high-voltage on the exposed contacts.