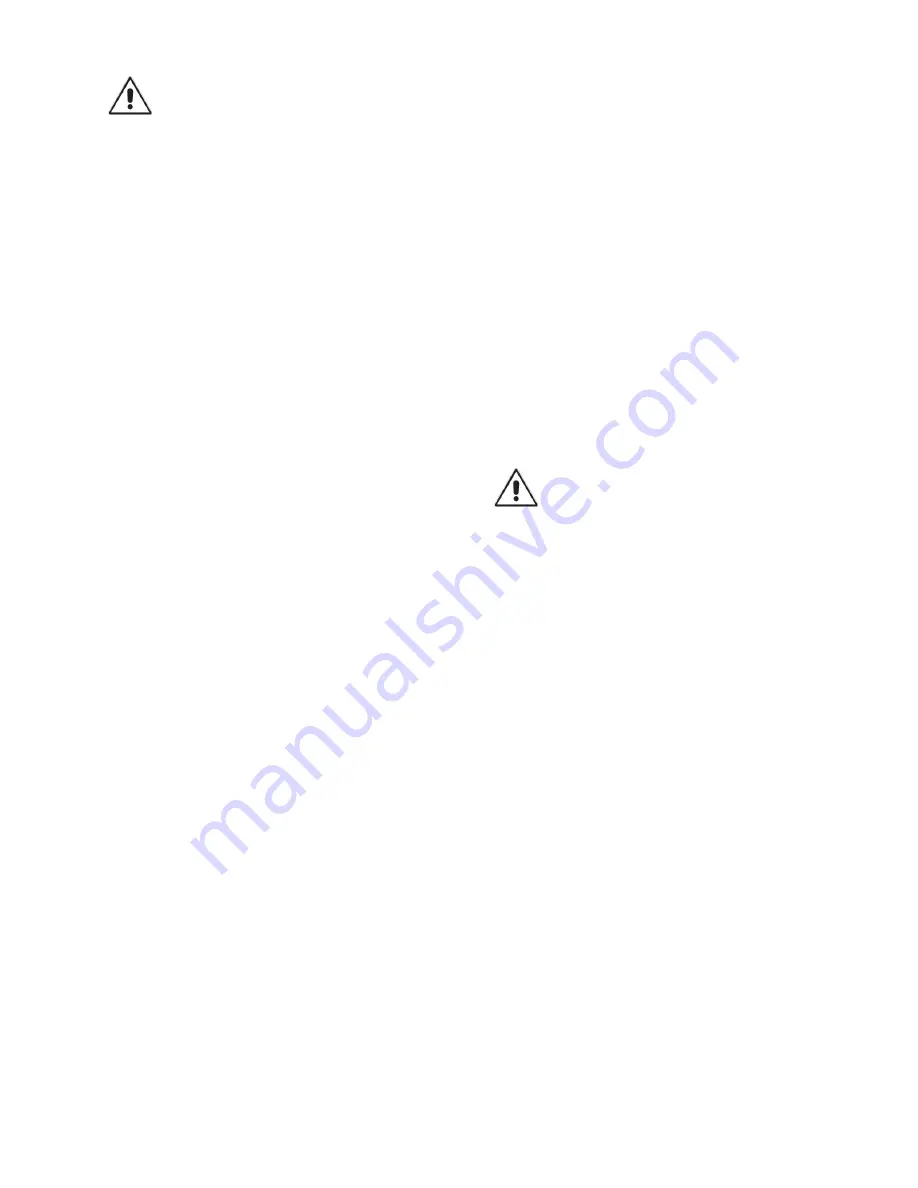
11
valves or the units are spaced.
CAUTION ! - When check valves are not used
and a series system is accidentally shut down
instantaneously (power failure), sufficient time
must be allowed for pump impellers to stop
rotating backwards before restarting.
NOTE:
Pressure inside 3” discharge pumps or smaller should
not exceed 100 PSI (231 ft of Head). Pressure inside 4”
discharge pumps or larger should not exceed 200 PSI (462
ft. of Head).
D-3.1) Report:
Included at the end of this manual are two start-up report
sheets, these sheets are to be completed as applicable. Return
one copy to the Prosser Pumps Service Department and store
the second in the control panel or with the pump manual if no
control panel is used. It is important to record this data at initial
start-up since it will be useful to refer to should servicing the
pump be required in the future.
D-3.2) Identification Plate:
Record the numbers from the pump’s identification plate on
both START-UP REPORTS provided at the end of the manual
for future reference.
D-3.3) Insulation Test:
Before the pump is put into service, an insulation (megger)
test should be performed on the motor. The resistance values
(ohms) as well as the voltage (volts) and current (amps) should
be recorded on the start-up report.
SECTION E: PREVENTIVE MAINTENANCE:
Prosser pumps are CSA approved. The following procedure
must be followed to assure proper pump operation and unit
CSA approval integrity.
1.)
General Safety:
Frequent inspection shall be made. All
electrical parts, including the portable cable and wiring, shall
be kept in a safe condition.
KEEP CABLE GLAND NUTS
TIGHT, CHECK FREQUENTLY.
There shall be no openings
into the casing of the electrical parts. The machine frame shall
be effectively grounded. The power wires shall not be used
for grounding. The operating voltage shall match the voltage
rating of the motor(s).
2.)
Servicing:
Pump and control enclosures shall be restored
to the state of original safety with respect to all lead entrances,
etc., following disassembly.
3.)
Renewals and Repairs:
Special care shall be taken in
making renewals or repairs. Leave no parts off. Use replacement
parts furnished by the manufacturer. When any lead entrance
is disturbed, the original leads or exact duplicates thereof shall
be used.
4.)
Fastenings:
All bolts, nuts, screws and other means of
fastenings and also threaded covers, shall be in place, properly
tightened and secured.
5.)
Cable Requirements:
A heavy usage, type SOW
submersible cable shall be used. Special care shall be taken
in handling the cable against mechanical injury and wear.
Connections and wiring to the power source shall be in
accordance with all local electrical and safety codes.
6.)
Shaft Seals:
The seals should be inspected every
1500 operating hours for wear (more often if abrasives are
present). To make a quick check of the seal’s condition, drain
and inspect the oil in the seal chamber (See Section F-1).
If oil removed from the pump contains water or abrasives,
replace seals.
7.)
Amperage:
Amperage should be checked periodically
(at least weekly) to be certain that it does not exceed limits
recommended by manufacturer on pump nameplate.
8.)
Volts:
If a generator is the power source, check daily for
variation of voltage and cycles.
This pump is equipped with prelubricated bearings.
When a job is completed and before pumps are stored,
drain the oil from the seal chamber (a must before freezing
weather). If dirt or water are found in the oil, replace seals,
bearings, lower “O” rings and oil.
SECTION F: SERVICE AND REPAIR
NOTE:
All item numbers in ( ) refer to Figures 14 & 15 for
10-15HP and 16 & 17 for 25-50HP.
WARNING ! - Electrical power to the pump motors
must be disconnected and locked out to prevent
any dangerous electrical hazards or personnel
danger before any service work is done to the
pump.
F-1) Electrical Inspection:
When pumps are returned from a field operation, or when
a pump needs repair, prior to disassembly, and after
disconnecting the unit from the power source, make electrical
inspection of the pump, cable and control box. The test can
be done by using a megger and an ohmmeter.
F-1.1) Insulation Resistance - Cable & Control:
Use the megger to measure the insulation resistance. Attach
the megger probes to the pump lead side of the circuit breaker
in the control box, one probe to the ground lead and one
probe to a pump power lead. Acceptable values of insulation
resistance are 10 megohms or greater. If insulation resistance
is below 10 megohms, the motor leads should be disconnected
from the cable assembly so that the cable and motor can be
tested separately.
Should the cable show insulation resistance of less than 10
megohms, disconnect from control box and attach megger
probes to the individual leads within the cable. Values below
10 megohms of insulation resistance would indicate damage
or moisture and cable should be replaced. Low values of
insulation resistance below 10 megohms for the circuitry within
the control box would indicate damage or moisture, Any bad
parts should be replaced.
F-1.2) Insulation Resistance - Motor:
The insulation resistance of the motor stator can be measured
by attaching one probe of the megger to the motor power
leads and the other probe to the motor ground lead or to bare
metal of the pump frame. Insulation resistance values under
10 megohms would indicate presence of excessive moisture
within the stator winding. Such moisture can be removed from
the stator by placing the stator and frame assembly in an oven
and baking the assembly at 250°- 275°F for two to three hours.
Following such baking, re measure the insulation resistance
to verify that a minimum of 10 megohms has been attained, if
Summary of Contents for PROSSER STANDARD-LINE 9-81000 Series
Page 5: ...5 inches mm MODEL A B 9 81000 27 38 696 24 00 610 9 81500 29 12 740 25 75 654 A B ...
Page 6: ...6 inches mm MODEL A B 9 82500 33 95 862 30 69 780 9 85000 36 68 932 33 69 856 A B ...
Page 14: ...14 FIGURE 9 ...
Page 19: ...19 FIGURE 14 PUMP SERIES 9 81000 9 81500 ...
Page 20: ...20 FIGURE 15 PUMP SERIES 9 81000 9 81500 ...
Page 23: ...23 FIGURE 16 PUMP SERIES 9 82500 9 85000 ...