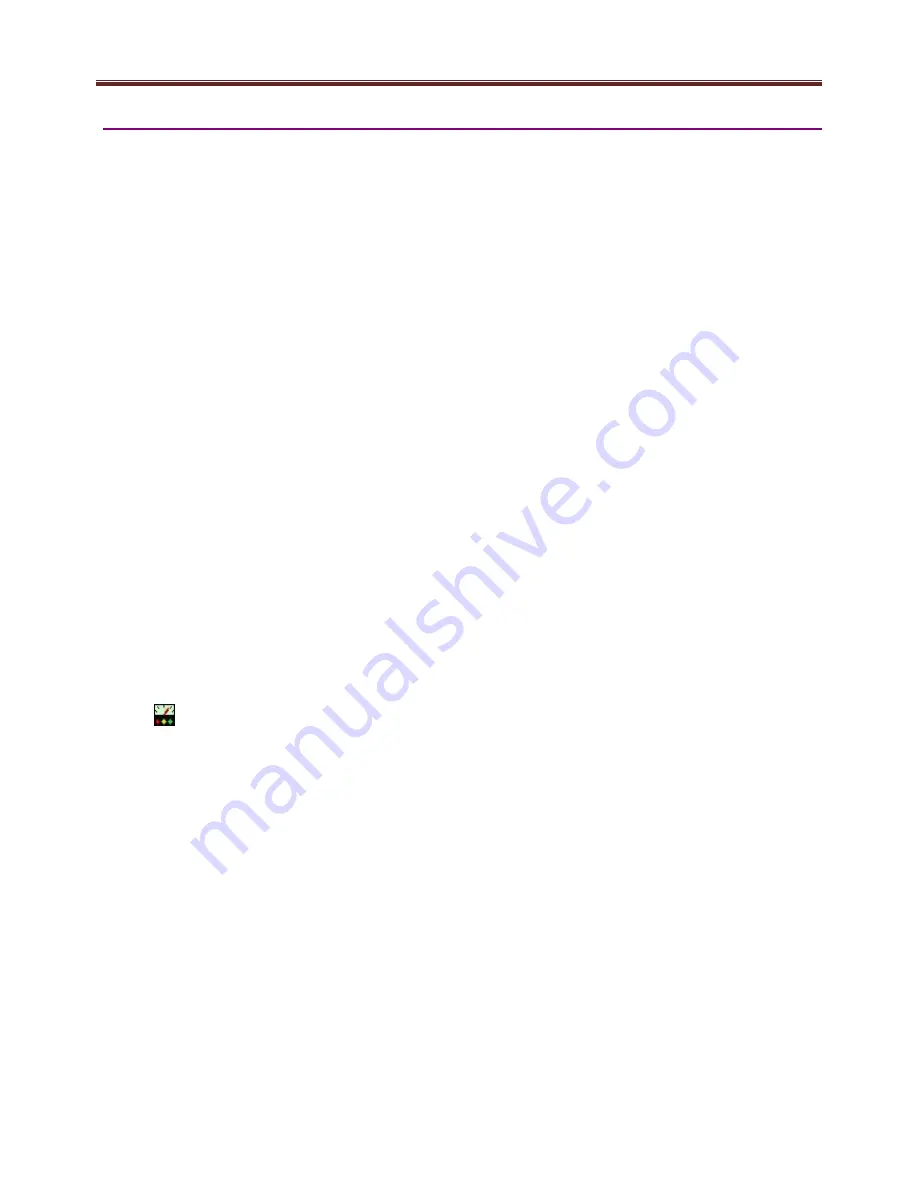
Xenus Plus User Guide
16-01344 Rev 06
Copley Controls
53
2.7.5: Following Error Fault Details
Position Error Reaches Fault Level
As described earlier, position error is the difference between the limited position output of the
trajectory generator and the actual position. When position error reaches the programmed Following
Error Fault level, the drive faults (unless the following error fault is disabled.) As with a warning,
a status bit is set. In addition, the fault is recorded in the error log.
Additional responses and considerations depend on whether the fault is non-latched or latched,
as described below.
Drive Response to Non-Latched Following Error Fault
When a non-latched following error fault occurs, the drive drops into velocity mode and applies the
Fast Stop Ramp deceleration rate to bring the motor to a halt. The drive PWM output stage remains
enabled, and the drive holds the velocity at zero, using the velocity loop.
Resuming Operations After a Non-Latched Following Error Fault
The clearing of a non-
latched following error depends on the drive’s mode of operation. Issuing a
new trajectory command over the CAN bus or the ASCII interface, will clear the fault and return
the drive to normal operating condition.
If the drive is receiving position commands from the digital or differential inputs, then the drive
must be disabled and then re-
enabled using the drive’s enable input or though software
commands. After re-enabling, the drive will operate normally.
Drive Response to a Latched Following Error Fault
When a latched following error fault occurs, the drive disables the output PWM stage without
first attempting to apply a deceleration rate.
Resuming Operations After a Latched Following Error Fault
A latched following error fault can be cleared using the steps used to clear other latched faults:
•
Power-cycle the +24 Vdc to the drive
•
Cycle (disable and then enable) an enable input that is configured as
Enables with Clear Faults or Enables with Reset
•
Access the CME Control Panel and press Clear Faults or Reset
•
Clear the fault over the CANopen network or serial bus
Summary of Contents for XEL-230-18
Page 1: ...123123 P N 16 01344 Revision 06 August 30 2019 Xenus Plus User Guide...
Page 2: ...Xenus Plus User Guide 16 01344 Rev 06 This page for notes...
Page 9: ...Xenus Plus User Guide 16 01344 Rev 06 Copley Controls 9 This page for notes...
Page 18: ...Xenus Plus User Guide 16 01344 Rev 06 Copley Controls 18...