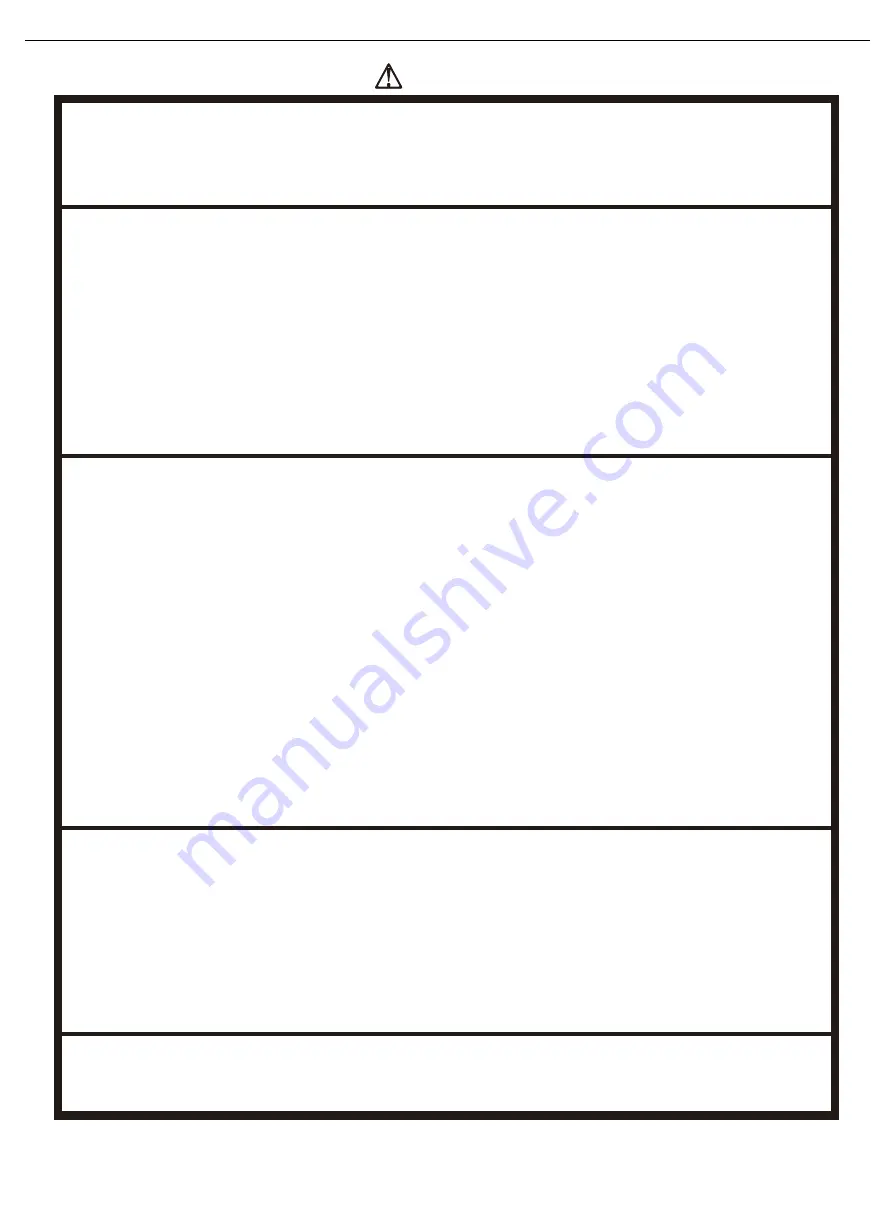
5
WARNING
10.
Detection of flammable refrigerants
• Under no circumstances shall potential sources of ignition be used in the searching for or detection of
refrigerant leaks.
• A halide torch (or any other detector using a naked flame) shall not be used.
11.
Leak detection methods
The following leak detection methods are deemed acceptable for systems containing flammable refrigerants:
• Electronic leak detectors shall be used to detect flammable refrigerants, but the sensitivity may not be
adequate, or may need re-calibration. (Detection equipment shall be calibrated in a refrigerant-free area.)
• Ensure that the detector is not a potential source of ignition and is suitable for the refrigerant used.
• Leak detection equipment shall be set at a percentage of the LFL of the refrigerant and shall be calibrated to
the refrigerant employed and the appropriate percentage of gas (25 % maximum) is confirmed.
• Leak detection fluids are suitable for use with most refrigerants but the use of detergents containing
chlorine shall be avoided as the chlorine may react with the refrigerant and corrode the copper pipe-work.
• If a leak is suspected, all naked flames shall be removed/ extinguished.
• If a leakage of refrigerant is found which requires brazing, all of the refrigerant shall be recovered from the
system, or isolated (by means of shut off valves) in a part of the system remote from the leak.
• Oxygen free nitrogen (OFN) shall then be purged through the system both before and during the brazing
process.
12.
Removal and evacuation
• When breaking into the refrigerant circuit to make repairs – or for any other purpose
–conventional procedures shall be used.
• However, it is important that best practice is followed since flammability is a consideration.
• The following procedure shall be adhered to:
Remove refrigerant;
Purge the circuit with inert gas;
Evacuate;
Purge again with inert gas;
Open the circuit by cutting or brazing.
• The refrigerant charge shall be recovered into the correct recovery cylinders.
• The system shall be “flushed” with OFN to render the unit safe.
• This process may need to be repeated several times.
• Compressed air or oxygen shall not be used for this task.
• Flushing shall be achieved by breaking the vacuum in the system with OFN and continuing to fill until the
working pressure is achieved, then venting to atmosphere, and finally pulling down to a vacuum.
• This process shall be repeated until no refrigerant is within the system. When the final OFN charge is used,
the system shall be vented down to atmospheric pressure to enable work to take place.
• This operation is absolutely vital if brazing operations on the pipe-work are to take place.
• Ensure that the outlet for the vacuum pump is not close to any ignition sources and there is ventilation
available.
13.
Charging procedures
• In addition to conventional charging procedures, the following requirements shall be followed:
- Ensure that contamination of different refrigerants does not occur when using charging equipment.
- Hoses or lines shall be as short as possible to minimise the amount of refrigerant contained in them.
- Cylinders shall be kept upright.
- Ensure that the refrigeration system is earthed prior to charging the system with refrigerant.
- Label the system when charging is complete (if not already).
- Extreme care shall be taken not to overfill the refrigeration system.
- Prior to recharging the system it shall be pressure tested with OFN.
• The system shall be leak tested on completion of charging but prior to commissioning.
• A follow up leak test shall be carried out prior to leaving the site.
14.
Decommissioning
Before carrying out this procedure, it is essential that the technician is completely familiar
with the equipment and all its detail.
It is recommended good practice that all refrigerants are recovered safely.
DC Inverter E
-
Series
Duct Type
Unit