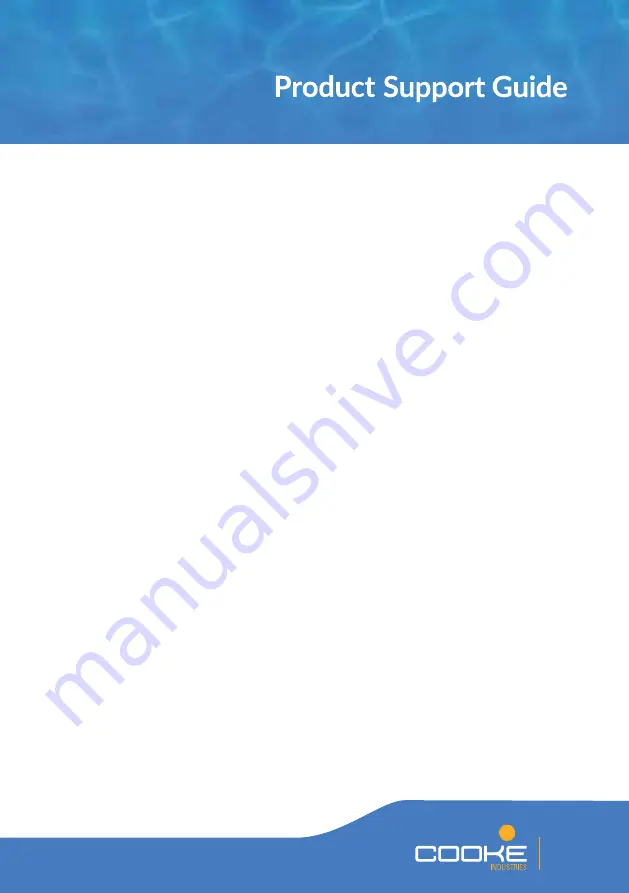
01
INDEX
Compliance notice
Page 02
Product applications and warnings
Page 03
Product components and part numbers
Page 04
Control box installation
Page 05
Sensor installation
Page 06
Solenoid installation
Page 08
Alternative installation options
Page 10
Start-up process
Page 12
Test and time delay modes
Page 13
Operation of indicator lights
Page 14
Troubleshooting process
Page 15
Other faults
Page 19
Maintenance & specifications
Page 20
Warranty notice
Page 21