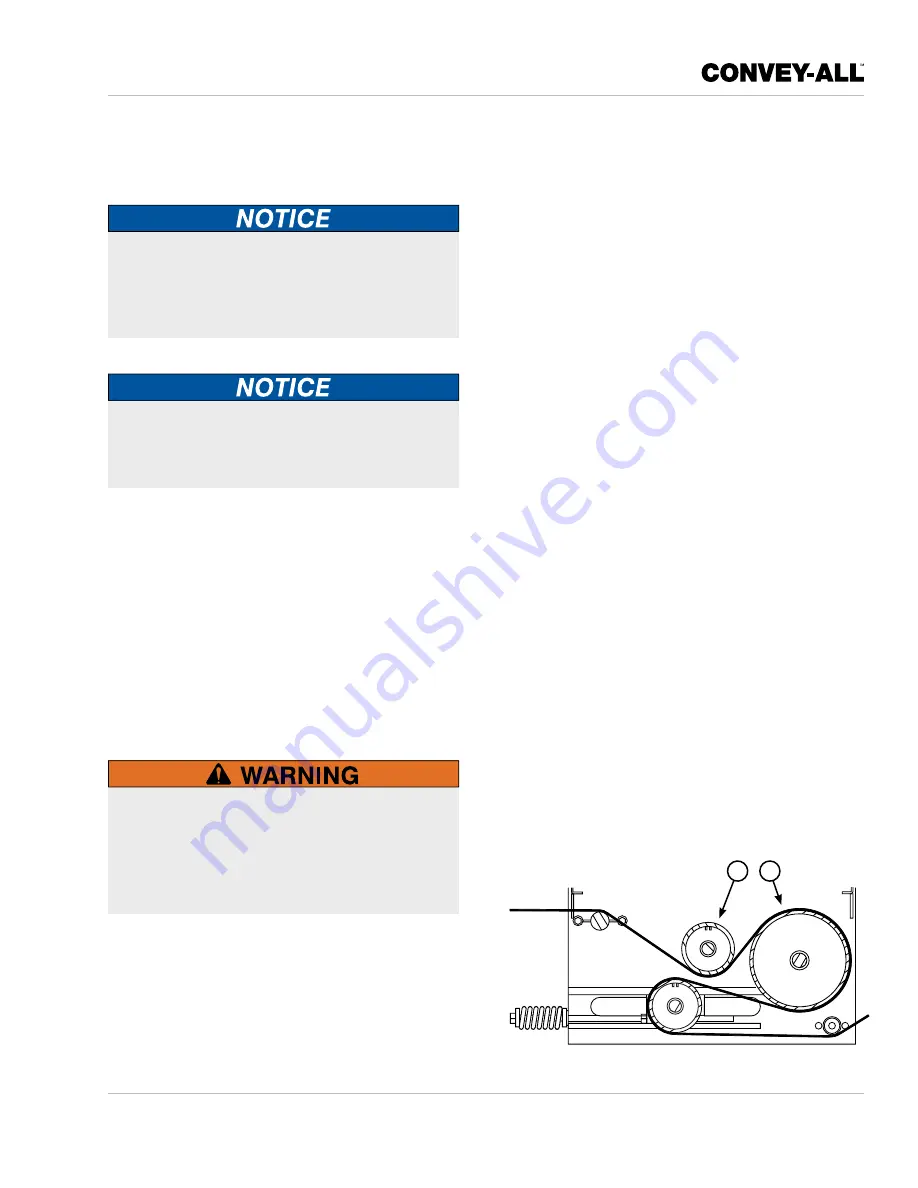
08.2020
4-9
Operator’s Manual: 1600-FL Series Conveyor
4.3.2 Conveyor Belt Alignment:
BELT DAMAGE HAZARD
Alignment of the belt must be checked at the
hopper, drive box (if equipped) and discharge.
Inspect weekly. Unaligned belt will cause
damage and void warranty.
BEARING FAILURE
If a roller is replaced, ensure both ends are
evenly aligned with the frame before running.
If not, bearing failure may occur.
The belt is properly aligned when it runs in the
centre of all rollers.
Check frequently during the first few minutes
of operation with a new belt, and then several
times during the first 10 hours.
The new belt normally seats itself during the
first 10 hours of operation and can be checked
weekly after that.
ROTATING BELT HAZARD
Idle the engine,
then rotate the belt slowly when checking
the alignment.
Turn off engine when adjusting rollers.
Note:
If belt is out of alignment,
it will move to the loose side.
Tighten loose side or loosen tight side.
Belt Alignment at Tail and Transition Roller:
1. Rotate the conveyor belt slowly, and check
the position of the belt on the tail roller.
2. Adjust one side of roller at a time.
- Loosen bearing housing, then adjust bolt.
3. Tighten the tail roller bearing housing.
4. Rotate the conveyor belt slowly, and check
the position of the belt on the hopper roller.
- Repeat steps until the belt is centred.
5. Replace housing guard.
Belt Alignment inside Drive Box (if equipped):
If necessary to adjust the position of the belt
inside the drive box, use drive roller to make the
adjustments.
6. Adjust one side of the drive roller at a time.
- Loosen the bearing housing, then adjust.
7. Tighten the bearing housing.
8. Run the belt a couple of revolutions and
check the alignment.
- Repeat steps until the belt runs centred.
9. Replace the bearing housing guard.
Fig 50 - Drive box; 5” pinch roller (a), 10” drive roller (b)
a
b
Summary of Contents for 1635-FL
Page 1: ...FIELD LOAD CONVEYOR 1635 FL 1645 FL OPERATOR S MANUAL...
Page 4: ...This page intentionally left blank...
Page 8: ...1 2 08 2020 Operator s Manual 1600 FL Series Conveyor This page intentionally left blank...
Page 20: ...2 12 08 2020 Operator s Manual 1600 FL Series Conveyor This page intentionally left blank...
Page 48: ...4 14 08 2020 Operator s Manual 1600 FL Series Conveyor This page intentionally left blank...
Page 54: ...5 4 08 2020 Operator s Manual 1600 FL Series Conveyor This page intentionally left blank...
Page 57: ...08 2020 6 3 Operator s Manual 1600 FL Series Conveyor This page intentionally left blank...