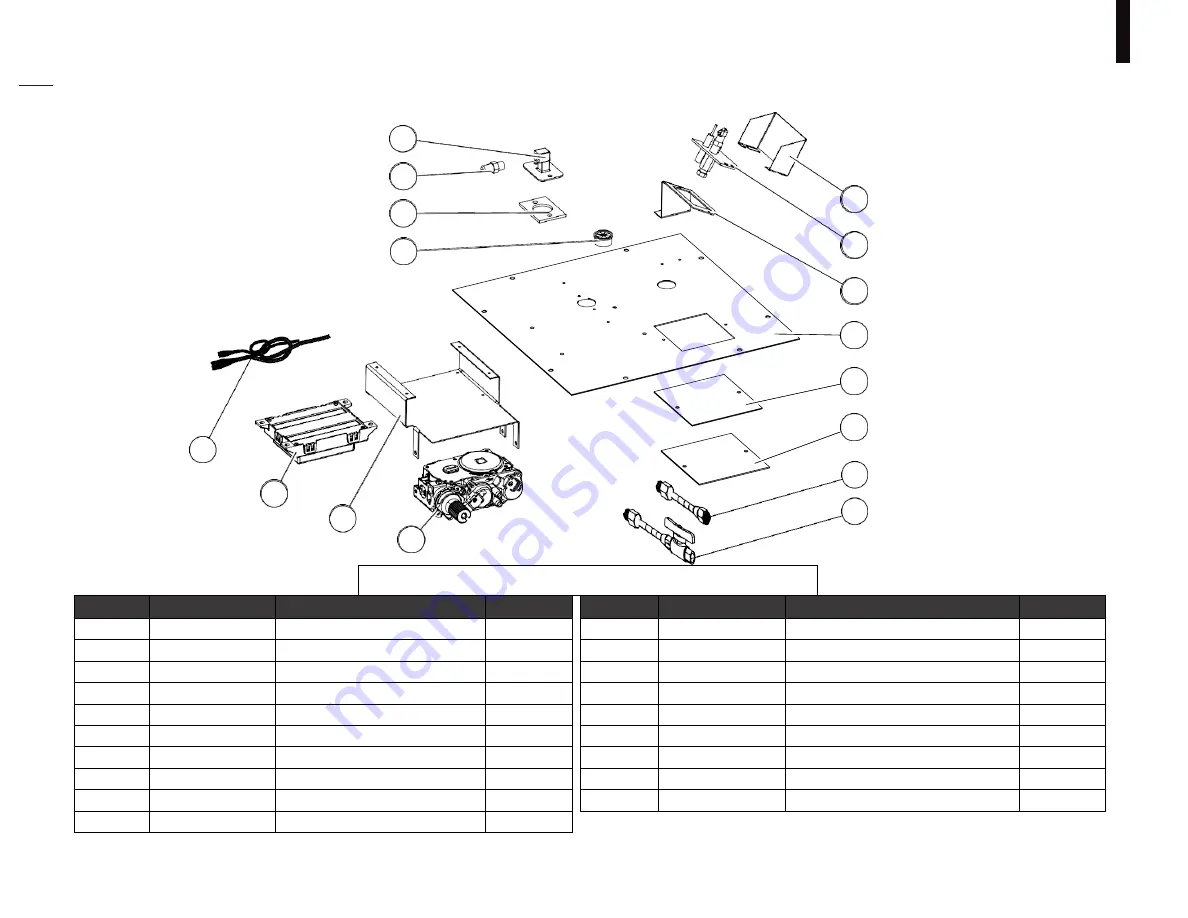
glass burner valve train assembly
Items may not appear exactly as illustrated
Ref. No. Part number
Description
Stocked
Ref. No.
Part number
Description
Stocked
1
W432-0103
Gas manifold
9
W585-0790-SER Pilot shield
2
W456-0037
Burner orifice #37 (NG)
Yes
10
W010-3024
Pilot assembly (NG)
Yes
2
W456-0052
Burner orifice #52 (P)
Yes
10
W010-3024
Pilot assembly (P)
Yes
3
W290-0157
Manifold gasket
Yes
11
W080-1304-SER Pilot bracket
4
W105-0001
Bushing
12
W035-0337-SER Valve train base
5
W010-1985
Wire harness assembly
Yes
13
W200-0456
Valve access cover
6
W190-0072
Control board
Yes
14
W290-0247
Valve access gasket
Yes
7
W080-1366
Valve bracket
15
W175-0311
3/8” Flex connector
8
W725-0065
Valve (NG)
Yes
16
W175-0217
Flex connector c/w valve
Yes
8
W725-0066
Valve (P)
Yes
1
2
3
4
9
8
190
1
11
0
1
12
1
1
13
2
1
13
4
5
5
6
1
13
5
6
7
1
13
6
7
8
re
pl
ac
e
me
nts
EN
58
W
4
1
5
-1283
/ F
/ 0
4
.3
0
.1
8