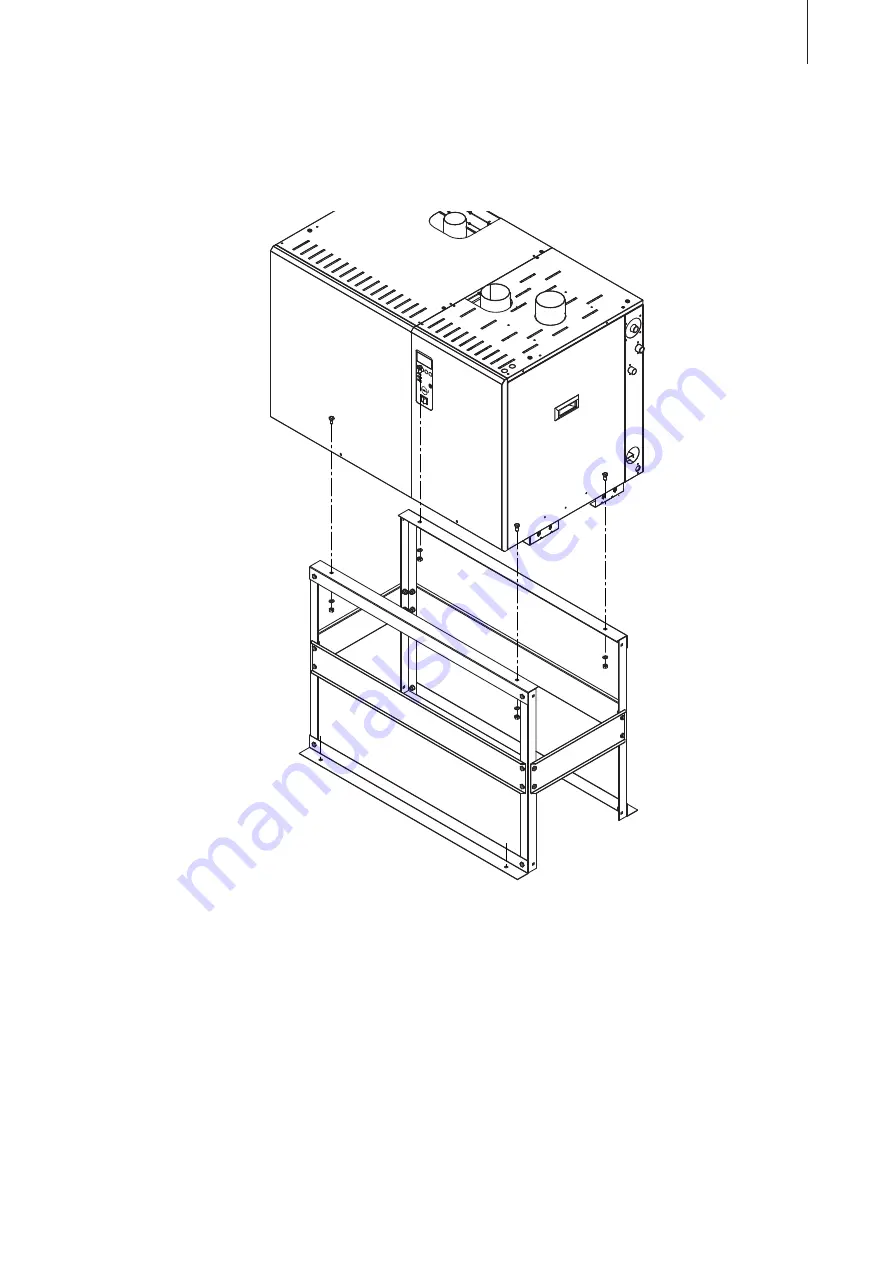
2
The Condair GS humidifiers must be mounted on the unit stand
supplied with the unit
. If mounting
on the unit stand supplied is not possible in your particular case, select a method of mounting that
is of similar stability. In case of doubt, please contact your Condair supplier.
5.2.2 Mounting the humidifier
Mounting instructions
1. Assemble the unit stand as shown in the separate installation instructions. Hand tighten all bolts
only.
2. Lift up humidifier with a lifting device approx. 900 mm above the floor.
. Position unit stand below the humidifier.
4. Lower the humidifier and align with the holes of the unit stand.
5. Fasten the humidifier to the unit stand using the bolts, cup washers and nuts provided.
6. Tighten all nut and bolt pairs to 22.6 Nm (200 lb-in) or until secure.
7. Position the entire assembly to the desired location. Make sure the humidifier is stable, shimming
of the floor below the support legs of the unit stand may be necessary.
8. Fix the unit stand to the floor (mandatory) via the four holes in the support plates of the unit stand.
Summary of Contents for GS 40 Series
Page 2: ......