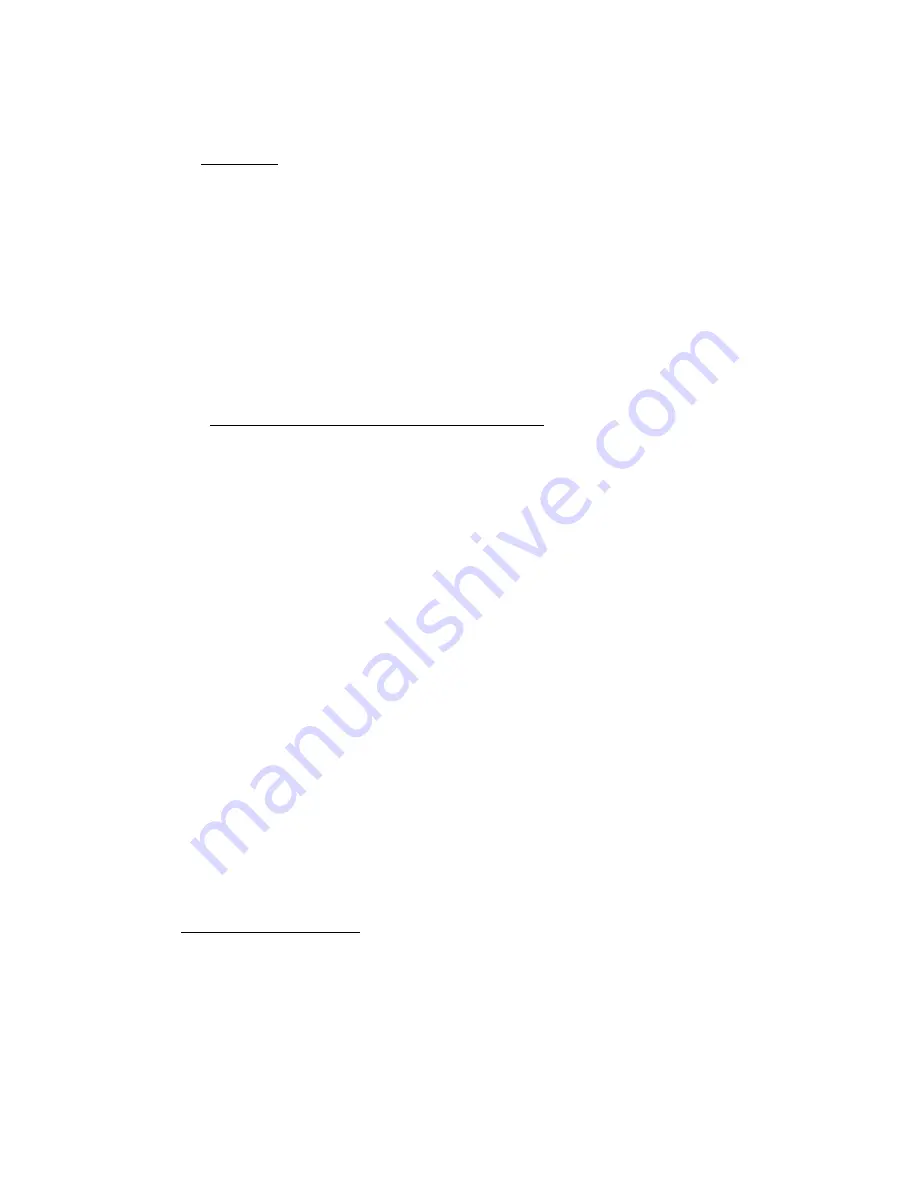
SECTION 6
Page 33
6.4
(continued)
9.
Remove the masking tape; and, as soon as the
gel coat has cured, block-sand it with 400 grit
sandpaper and water to remove orange peel and any
lap lines that may have developed. Hand-sand if
necessary to smooth stubborn areas.
5.
Wet-sand with 600 grit sandpaper.
6.
To restore gloss, buff with harsh grit buffing compound and
heavy duty polisher.
6.4.1
Finishing Large Areas with Epoxy Enamel
when a large area needs to be refinished, it is recommended that the
entire section be done with a good quality epoxy enamel.
Manufacturers of epoxy enamels supply application instructions on the labels
of the cans and in published booklets. The manufacturer's instructions should
be followed since different types require different solvents and/or handling.
The following is a typical epoxy enamel finishing system which can be used as
a guide.
TOOLS
MATERIAL
Suction spray gun or
Sanding surfacer - if
Paint brushes (good
required by enamel
quality bristle)
manufacturer
White cloth
100, 400, 600 grit wet
Epoxy enamel of desired color
or dry sandpaper
Thinner - as specified by
manufacturer
Masking tape
Sanding block
Paper
Stirring sticks
H.
Preparing the Surface
1.
Prepare the surface as instructed in Section
6.2.
Summary of Contents for Coronado 25
Page 1: ......
Page 21: ......
Page 22: ......
Page 23: ......
Page 24: ......
Page 25: ......
Page 26: ......
Page 27: ......
Page 28: ......
Page 29: ......
Page 30: ......
Page 31: ......
Page 32: ......
Page 33: ......
Page 34: ......
Page 35: ......
Page 36: ......
Page 37: ......
Page 38: ......
Page 39: ......
Page 40: ......
Page 41: ......
Page 42: ......
Page 43: ......
Page 44: ......
Page 45: ......