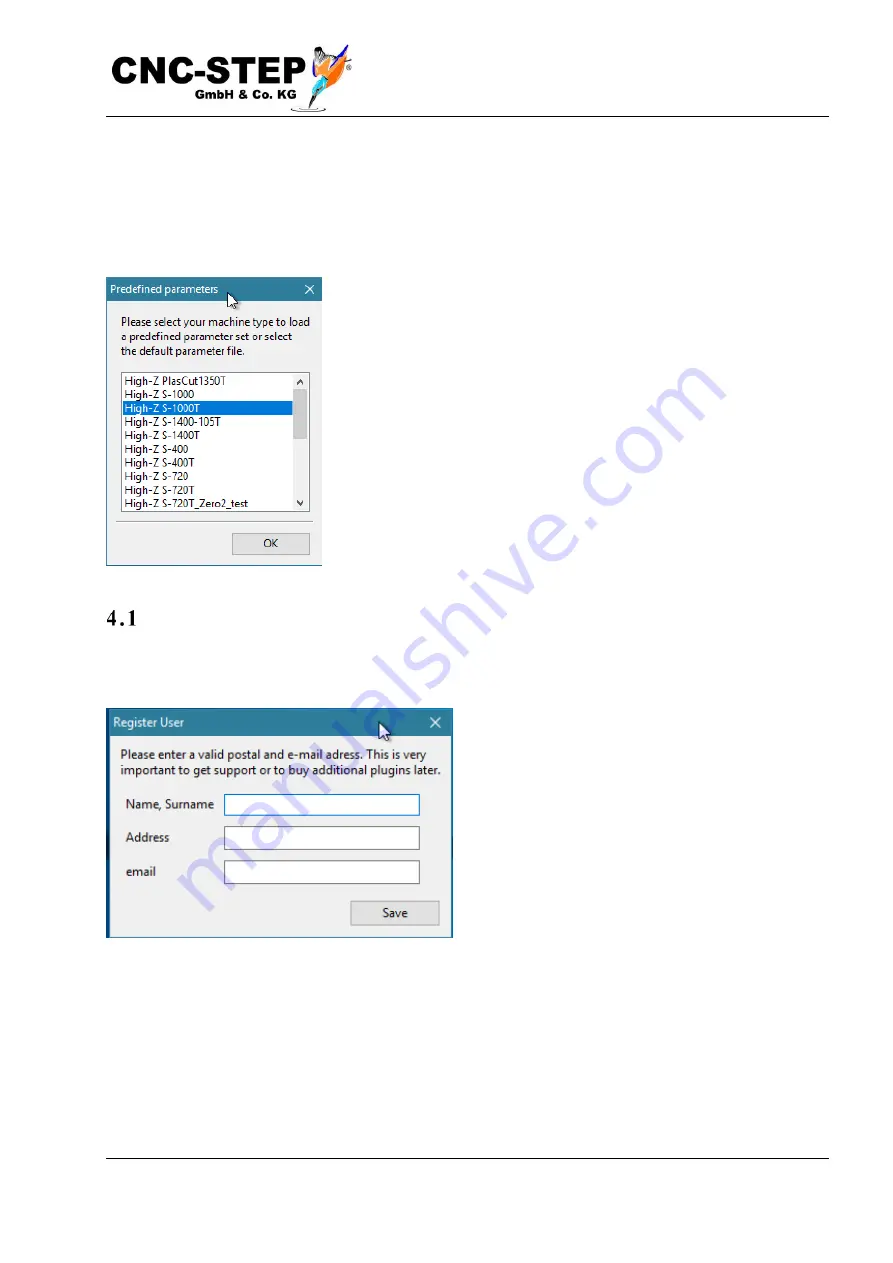
KinetiC-NC
User Manual
CNC-STEP GmbH & Co. KG ▪ Siemensstrasse 13-15 ▪ 47608 Geldern ▪ Germany
Page 22
Support: +49 (0)2831/91021-50
10.11.2018
4
Initial Sta rt-up
The first time you start the software, you will be asked for the language first .
Then a list of known machines is displayed, for which there are already predefined parameter.
U s e r i n f o r ma t i o n
During the first start of the software its necessary to enter the user details. This can be important if
you need support or you want to add additional options.