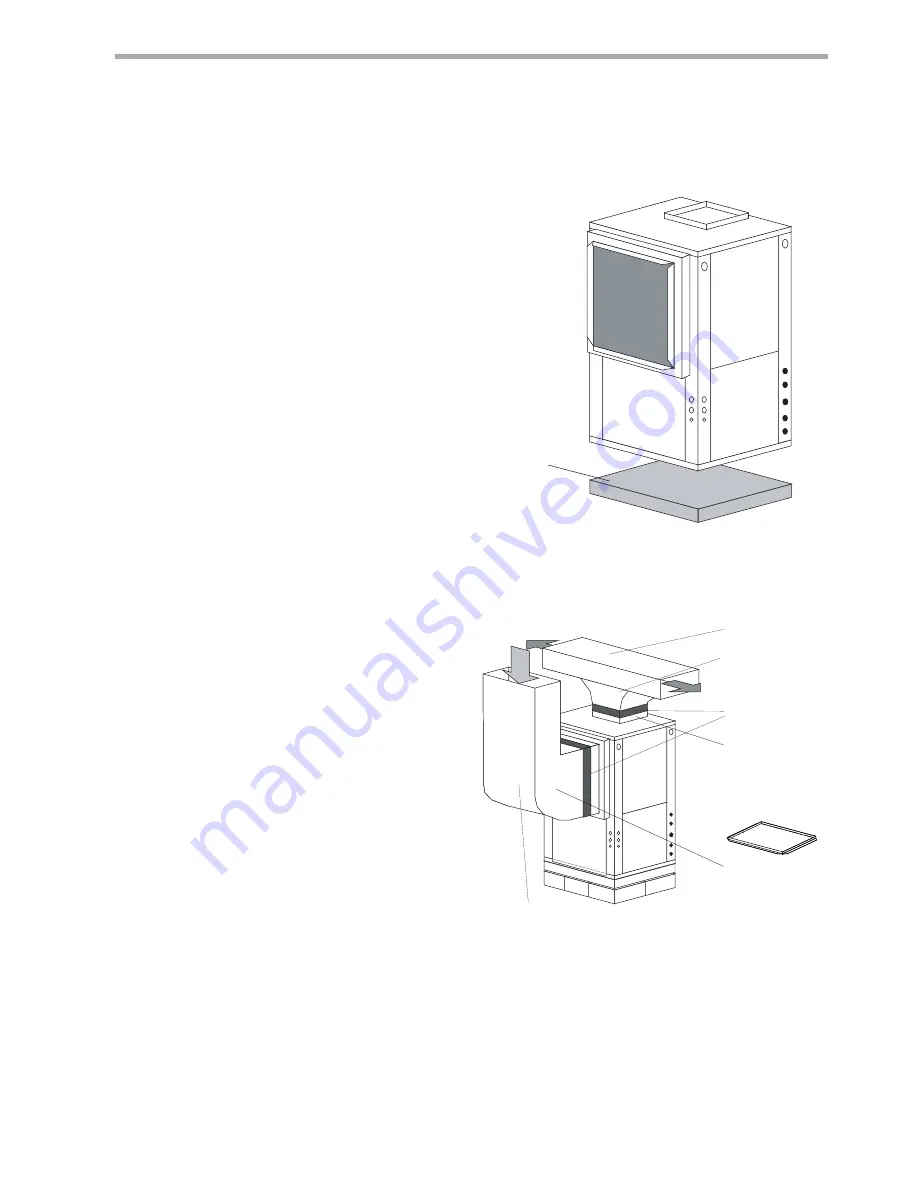
T H E S M A R T S O L U T I O N F O R E N E R G Y E F F I C I E N C Y
13
c l i m a t e m a s t e r. c o m
Tr a n q u i l i t y 1 6 ( T C ) S e r i e s
R e v. : 2 5 J u l y, 2 0 1 7
Vertical Installation
Vertical Unit Location
Units are not designed for outdoor installation. Locate
the unit in an INDOOR area that allows enough space
for service personnel to perform typical maintenance
or repairs without removing unit from the mechanical
room/closet. Vertical units are typically installed in a
mechanical room or closet. Never install units in areas
subject to freezing or where humidity levels could
cause cabinet condensation (such as unconditioned
spaces subject to 100% outside air). Consideration
should be given to access for easy removal of the fi lter
and access panels. Provide suffi cient room to make
water, electrical, and duct connection(s).
If the unit is located in a confi ned space, such as a
closet, provisions must be made for return air to freely
enter the space by means of a louvered door, etc. Any
access panel screws that would be diffi cult to remove
after the unit is installed should be removed prior to
setting the unit. Refer to Figures 7 and 8 for typical
installation illustrations. Refer to unit submittal data or
engineering design guide for dimensional data.
1. Install the unit on a piece of rubber, neoprene or
other mounting pad material for sound isolation.
The pad should be at least 10mm to 13mm in
thickness. Extend the pad beyond all four edges
of the unit.
2. Provide adequate clearance for fi lter replacement
and drain pan cleaning. Do not block fi lter access
with piping, conduit or other materials. Refer to
unit submittal data or engineering design guide
for dimensional data.
3. Provide access for fan and fan motor maintenance
and for servicing the compressor and coils without
removing the unit.
4. Provide an unobstructed path to the unit within
the closet or mechanical room. Space should be
suffi cient to allow removal of the unit, if necessary.
5. In limited side access installations, pre-removal of the
control box side mounting screws will allow control
box removal for future servicing (TC units only).
6. Provide access to water valves and fi ttings
and screwdriver access to the unit side panels,
discharge collar and all electrical connections.
Flexible canvas duct
connector to reduce
noise and vibration
Use turning vanes in
supply transition
Internally insulate supply
duct f
RUILUVWP
each way
to reduce noise
Internally insulate return
transition duct to reduce noise
Rounded return
transition
5HPRYHVXSSO\GXFW
IODQJHVIURPLQVLGHEORZHU
FRPSDUWPHQWDQGLQVWDOO
on supply air opening of
unit. Do not use a supply
DLUSOHQXPGXFWVPDOOHU
than the size of the supply
duct flanges.
Figure 8: Typical Vertical Unit Installation Using
Ducted Return Air
Air Pad or extruded
polystyrene insulation board
Figure 7: Typical Vertical Unit Mounting